Featured in this post
Enterprise Asset Management Capabilities: What Does Your Business Need?
Enterprise Asset Management Capabilities: What Does Your Business Need?
19 Jul 2022
Aptean Staff Writer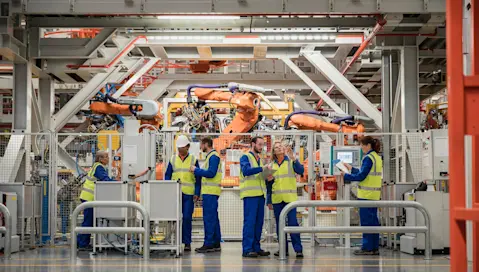
With rising costs and endless supply chain disruption, being able to keep your operations running efficiently and cost effectively has become a competitive advantage. An Enterprise Asset Management (EAM) solution ensures that your plant’s assets are healthy and running smoothly so that you can guarantee delivery to your customers. Whether you want to replace a legacy system, or this is your first venture into the world of EAM, you know that you need an efficient, data-driven and future-ready approach to managing your assets and creating value for the business.
Gone are the days of managing maintenance with spreadsheets, or worse, with pen and paper. You need to monitor and optimize your assets. And at the end of their lifecycle, you need to make smart replacement decisions—all of which requires a new approach to maintenance and repair. To implement this new method, you’ll need full visibility into current work orders, maintenance schedules and parts inventory, and you’ll need to be able to create status reports so that everyone in the enterprise has the same information.
EAM solutions offer asset-heavy businesses a holistic view of company assets by providing them real-time visibility of their performance and historical records of past maintenance activities. However, there are specific features that you will need in order to get to an intelligent, data-driven asset management strategy. These capabilities should help you:
Avoid unscheduled downtime
Increase asset performance and longevity
Streamline and automate maintenance operations
Improve plant efficiency, and more importantly, your bottom line
Read more if you’d like a more comprehensive overview of what EAM is and what it does, but if you already know you need an EAM and want to narrow down your potential vendors, then read on for the four must-have features to look for in EAM packages. If a possible vendor doesn’t offer all of them, move on to the next.
1. Advanced Analytics and Reporting
To stay competitive and avoid costly downtime, your maintenance can’t be a reactive activity. With your EAM system, you get a complete overview of your maintenance operations, but you also need to be able to report on strategic questions, such as understanding the costs of your maintenance activities. This means you’ll need to look for an EAM that will offer you advanced reporting capabilities and in-depth operational insights.
For example, you should know the maintenance department’s activity in real time, as well as current asset performance to eliminate frequent problems and reduce unexpected downtime. Aptean EAM will help you track key performance indicators (KPIs).
You can examine KPIs like:
Maintenance costs
Mean Time to Failure (MTTF)
Schedule compliance ratio
Incident resolution and response time
Asset downtime
Failure frequency
Spare parts costs
Aptean EAM has configurable, granular reporting that allows you to drill down and find the root cause of recurring issues. For example, if your management team wants to see weekly updates on labor costs, you can set it up so that report runs automatically.
With the right set of analytical tools, you’ll be able to quickly discover issues and make strategic decisions. For instance, you run a report and you see that in one of your facilities there was a massive jump in labor costs last week for the maintenance team. You analyze the report a bit further and discover that the main asset in that facility has been temperamental, and parts for it are expensive. You can compare the current costs and make decisions on whether to replace the asset or if it would be cheaper to continue a planned maintenance schedule and restock spare parts.
Aptean's exclusive analytics and reporting tools provide your team with flexible instruments that allow you to create customized reports and analysis—with pre-defined templates included.
2. Work Order Management
Your work orders are the backbone of your maintenance plan and help you keep detailed records of your maintenance activities. A work order delineates the resources needed to conduct work on an asset. It should not only tell your team in detail what work must be performed, but it should also give everyone information about the task. For example, if you have a new tech, the work order could include the previous records and the manual for the asset.
A work order can help you track the type of labor performed and prioritize work by sending teams to mission-critical assets first. As the maintenance plan progresses, you’ll be able to analyze maintenance data about work orders, helping you determine whether it’s more cost-effective to replace or to repair a piece of equipment.
Work order management tools within EAM solutions help you keep track of labor, parts and miscellaneous maintenance costs, as well as help you estimate and track labor on upcoming maintenance projects. Robust reporting shows outstanding work orders for each day, week or even by month. You can perform downtime tracking reports and send notifications to employees based on the type of work and status. Aptean EAM software has user-friendly, configurable dashboards so that you can easily track every detail of your open work orders, including status, parts and downtime hours.
3. Robust Inventory Management
Inventory management capabilities are an absolute must-have feature for any asset-intensive business. When your equipment needs repair, your technicians need to know if the spare part is in stock, where it’s located and if they have the proper tools to complete the job. EAM with inventory management functionality provides just that. In addition, it helps prevent stock outs of important parts and reduces excess and obsolete inventory.
The inventory management functionality of your EAM will send you notifications when the quantity of parts goes below a specific threshold, which ensures that you keep the right number in stock. Technicians can go into the work order and check if the part they need is in stock before they begin work. If a part isn’t in your warehouse, advanced search allows you to check warehouses throughout the enterprise and have one sent from other locations.
To keep tabs on your most commonly used parts, you can create reports and drill down to see specific locations where the parts are being used and even which techs are using it. This helps you eliminate superfluous parts, and with real-time inventory reporting, you get a bird's-eye view of all parts as well as a cost breakdown.
4. Audit and Regulatory Compliance
If you work in a manufacturing enterprise, you know that inspections and audits can happen anytime. Equipment and instruments need to be running safely and to code and with proper paperwork. When auditors come in to inspect your facility, they will often examine the equipment first, so you need to ensure that you can answer any questions about procedures and protocols. If not, you could face hefty fines or even shutdowns until any issues are addressed.
With the right EAM, you can ensure that your operations are consistent with regulatory standards for your industry, which gives you peace of mind in your maintenance processes. You can also perform inspections from anywhere. Here is where your EAM really shines—by consolidating all maintenance, parts inventory and reports in one system, you can easily produce any pertinent paperwork for the auditor with a few clicks of a mouse.
You’ll reduce safety risk with incident analysis and corrective action traceability tools. With SaaS software and mobile apps for the techs, you’ll have a clear audit trail of all paperwork because it will be saved in the cloud. Therefore, your techs don’t have to hand write reports and then add them to the system later; instead, they can type in work orders and information as they complete the job, which ensures that they can be reviewed in a timely manner.
Electronic paperwork reduces incorrect data entry and lets your techs know if data is keyed in incorrectly. With EAM, maintenance is standardized throughout the organization. Calibration events are logged, and if an issue arises, the EAM will trigger a report. That means that you will have consistency across all your facilities and the digital paper trail to back it up.
Beyond Functionality: What to Consider When Examining EAM Solutions
We’ve covered the top enterprise asset management capabilities that you should be looking for when comparing systems, but your decision will need to encompass far more than functionality. Here are a few other things to consider as you evaluate both solutions and vendors:
Industry experience: You want your EAM provider to understand your industry’s needs. Even better, your vendor should provide software that’s customized to your industry. For example, Aptean EAM was created by industry experts for industry experts.
Support and service: To get the most from any software solution, you need the backing of an experienced and knowledgeable team. Aptean will be a partner throughout the lifetime of the software.
Scalability: Your EAM solution should be agile and expand to empower your business as it grows. Aptean has you covered on this front—the system includes a computerized maintenance management system (CMMS) for smaller organizations so that the software can grow with you.
Asset-heavy businesses like yours must overcome several challenges; namely, to increase equipment uptime, improve asset utilization and reduce maintenance costs. To facilitate these processes, your enterprise must work on a continuous improvement loop in your maintenance operations.
However, you can’t do it alone. With Aptean EAM, you get a flexible, agile maintenance solution that helps you continuously perfect your maintenance operations on the road toward shop floor excellence.
Want to learn more about how EAM can boost your operation’s visibility and efficiency? Reach out—we’d love to talk.
Related Articles
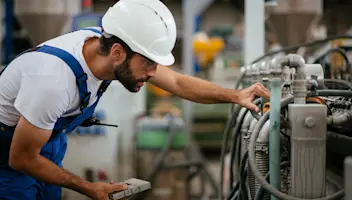
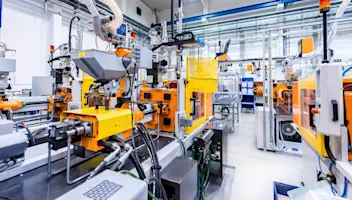
Ready to start transforming your business?
We’ve got the specialized EAM solutions you need to conquer your industry challenges.
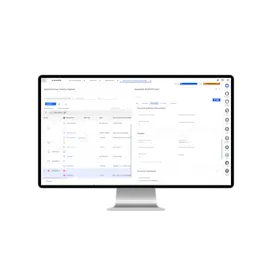