Featured in this post
Manufacturing ERP: Everything You Need To Know
Manufacturing ERP: Everything You Need To Know
5 Apr 2024
Aptean Staff Writer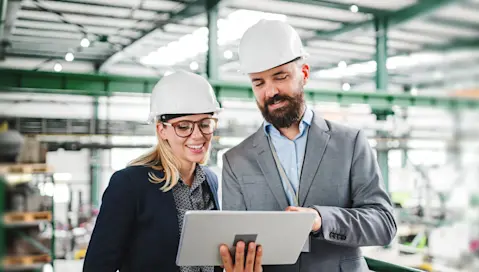
Whether you’re a manufacturer looking to replace outdated software, switch to a new provider or you’re just starting out on your enterprise resource planning (ERP) journey, selecting and implementing a broad-reaching system can feel like a high-stakes and time-consuming commitment.
As such, it’s critical to invest time and effort in the research and evaluation phase of the project. Because, while the right manufacturing ERP will streamline your end-to-end operations, maximizing efficiency and driving profitability, choosing a system not fit for your business purposes can leave you out of pocket and needing to undertake the entire process again.
To help you navigate the challenge of investing in or upgrading your ERP software, we've created this guide to manufacturing ERP that covers everything from what it is, important features to look for, key benefits and much more. Whatever your manufacturing ERP questions, we’ve got the answers. Read on.
What Is ERP for Manufacturing?
Manufacturing enterprise resource planning software is designed to digitize and optimize every aspect of manufacturing operations, from demand forecasting and production planning to supply chain and inventory management. So you can run your enterprise more efficiently, save time and money, increase the accuracy and speed of production, and improve customer satisfaction.
An ERP for manufacturing provides complete real-time data visibility and comprehensive reporting functionality empowering you to analyze every aspect of production, utilize resources effectively and make stronger strategic decisions. Not only does this streamline day-to-day operations, but it allows you to enact a cycle of continuous improvement that future-proofs your business and boosts profits long term.
There are many different types of manufacturing ERP solutions available on the market—we’ll talk about this in greater depth later. However, most ERP platforms include a core set of features that support front-office, back-office and shop floor operations, including:
Order management
Inventory management
Customer relationship management (CRM)
Warehouse management
Supply chain management
Finance and accounting
The best manufacturing ERP software will also offer specialized functionality, modules and integrations catering to manufacturing-specific needs.
Which Businesses Can Use a Manufacturing ERP?
Regardless of size or setup, every manufacturing business can benefit from an ERP system to streamline operations, from order receipt to delivery and customer support.
Small and Medium Enterprises (SMEs)
For smaller enterprises, manufacturing ERP provides a platform that works across your company, connecting departments and removing silos that can limit growth. In addition, ERP software streamlines and automates core manufacturing operations like quality control, material procurement and production scheduling, allowing you to maximize resource utilization and focus on developing your business.
Large Scale Enterprises
To optimize extensive or global operations, large manufacturers require cutting-edge ERP systems supported by artificial intelligence (AI), business intelligence (BI), machine learning and advanced analytics. These systems can smooth the complexity of your large operation, providing a central system to ensure everyone is working from the same, accurate information—improving collaboration, maximizing productivity and controlling operating costs.
Manufacturing Mode
Whether you’re running on a just-in-time, make-to-order, make-to-stock or batch manufacturing model, there are ERP systems available to solve the unique challenges of your sector. Whether it’s lot traceability and formula recipe management for batch manufacturers, or highly sophisticated forecasting and analytics capabilities to accurately model future demand for make-to-stock manufactures, there’s an ERP with your name on it.
4 Signs Your Manufacturing Business Needs an ERP Solution
Efficiency is the key to a thriving manufacturing business; but when you’re busy with the day-to-day grind, how can you understand whether your existing software is helping or hindering the growth of your business? How do you know if you could be better managing your inventory, increasing production output or reducing operating expenses?
Here are the top four signs that indicate it's high time to update to a specialist manufacturing ERP.
Your business operations are manual and error-prone: Are you and your staff drowning in manual processes, time-consuming tasks and laborious workarounds? Does this lead to delays, errors and inaccuracies? A modern manufacturing ERP automates tasks, streamlines workflows, removes paperwork, reduces errors and maximizes productivity.
Your departments are disconnected from each other: Are your teams working in silos? Is departmental data kept in disparate systems with limited visibility across your operation? With an ERP you gain a central platform for all departments and a single source of truth for your operational data, fostering collaboration and improving communication across your entire organization.
Your demand forecasting and production planning are inefficient: Do you often have to delay customer orders, experience stoppages on your production lines, or face regular shortages and surpluses? Do you lack real-time visibility into your inventory and supply chain? An ERP can streamline your scheduling, optimize inventory management and give you complete transparency across your operations—helping you maximize output and fulfill orders on time.
You’ve difficulty tracking production costs: Struggling to track and manage production costs? Think you’re spending more than you should be? An ERP provides real-time cost insights, helping you reduce expenses, identify areas for improvement and optimize your bottom line.
What Are The Benefits of Using Manufacturing ERP Software?
Investing in ERP software for the manufacturing industry empowers you to master many common business challenges. Straight out of the gate it can significantly improve scheduling, boost output and help you achieve faster scaling compared to relying on manual processes or legacy technology. This translates to several benefits, including:
Real-Time, 360-Degree Data Visibility: So every person in your organization can access accurate information and use this data to make informed decisions. For manufacturers in highly regulated or scrutinized industries, such as food and beverage or cosmetics, this visibility enables end-to-end traceability to fulfill both regulatory and consumer demands for transparency.
Intelligent Scheduling Capabilities: Rather than tackling jobs in chronological order, you can choose how to group them. For example, you can prioritize high-value customers to maintain satisfaction levels or group like-for-like jobs to limit time lost changing machinery settings.
Accurate Inventory Management: With better scheduling and complete data integration, you can plan and manage inventory requirements in line with work orders to minimize outages, reduce overstock and source materials from multiple suppliers.
Standardized Working Processes: If everyone is using the same manufacturing ERP software, your processes and procedures will be consistent for every job. You can also use an ERP for manufacturing to incorporate essential health and safety checks, quality control and industry compliance to ensure a continually high standard of production.
Continual Analysis and Improvement: Selecting a manufacturing ERP solution with built-in BI tools enables you to track the progress and profitability of every job. This way, you can understand the true value of customers and job types, focusing new business development on areas that yield the greatest profit.
6 Essential Features To Look for in a Manufacturing ERP System
So now you know what a manufacturing ERP is and what benefits it can provide, it’s time to evaluate your choices. With many options on the market, it can be hard to understand which is the right ERP for your manufacturing business.
You’ll need to decide what functionality your operation needs. To help you get started, here are some essential features you should consider while evaluating manufacturing ERP systems.
Shop Floor Management: A manufacturing ERP provides your team with insights into what’s happening across the shop floor, with accurate data on inventory, work orders, delays and more. This eliminates confusion, allows free-flowing communication and improves productivity. What’s more, ERP automates tedious tasks like generating work orders—saving time and freeing up staff for more complex activities.
Quoting and Estimating: With past quote data and vendor pricing all available at their fingertips, a manufacturing ERP system allows your team to create accurate quotes and improve future pricing strategies based on actual revenue compared to past estimates.
Production Scheduling: With manufacturing ERP providing accurate demand forecasting and data on capacity, inventory and staff availability, you can optimize production scheduling. This minimizes disruption, improves efficiency and ensures timely delivery of your products. An ERP solution also offers flexibility and easy adjustment to prioritize important work orders—ultimately, reducing downtime and maximizing profitability.
Inventory Control: With real-time inventory data, manufacturing ERP software helps your team compare the availability of materials or ingredients with your orders and plan according to the data. It can also assist in handling complex purchase orders with multiple vendors, so you can leverage discounts and vendor-specific pricing to ensure you get the best deals on raw materials while always having the right amount of stock to hand.
Financial Management: ERP software offers you real-time financial and operational data, helping you make better financial predictions. It automates processes and provides complete visibility allowing your team to react quickly with accurate information from quote to cash collection.
Supply Chain Management: With the supply chain management tools a manufacturing ERP offers you gain greater flexibility and resilience. By streamlining every step of your supply chain from supplier relationships and inventory control to resource allocation and logistics, ERP software enhances agility and keeps you on track for timely completions and deliveries.
What Types of Manufacturing ERP Are Available?
Not all ERPs are created equal, and not all ERPs can provide the features your manufacturing business will need. So, let’s now look at the three different types of ERP solutions available to manufacturers.
1. Generic ERP software, which can be used by companies in multiple sectors, offers most of the features we mentioned above, but is not designed specifically for manufacturers. So, while it may be tempting to choose generalist software if you’ve never had an ERP system before, you’ll miss out on valuable key functionality if you choose to buy a generic solution. And if your business is using a general manufacturing ERP system already, but it’s not delivering the specific functionality you need, then it’s time to upgrade to something more specific.
2. Broad manufacturing ERP systems can be used in any manufacturing sub-sector. They provide more value than generic ERP software because they include features built specifically for manufacturers' needs. For example, they include tools for managing shop floor process changes and machine maintenance scheduling capabilities.
As we mentioned, general manufacturing ERP delivers more value than software designed to work in any industry. However, if you decide to go with a generic or broad ERP system, you could end up needing to bolt-on additional modules or customize your platform to get the exact functionality you need—which makes deploying, running and upgrading your ERP software more complex and impacts return on investment (ROI).
For true investment value, your business should be looking for industry-specific ERP that delivers functionality tailored to your sector. Speaking of which…
3. Industry-specific manufacturing ERP solutions include such systems as process manufacturing ERP, discrete manufacturing ERP and food manufacturing ERP. These are the most popular choices for manufacturing organizations, as they provide you with specific features needed to run your business efficiently.
Process manufacturing ERP software includes formula/recipe management modules to calculate and scale ingredient quantities for batch manufacturing control. Process ERP systems also include lot traceability to support accurate labeling, industry compliance and quality control processes, and help with product recalls.
Discrete or industrial manufacturing ERP software enables manufacturers to turn quotes and estimates into a bill of materials (BoM) to streamline the sales process and accurately match upcoming orders with component availability.
For more information on these two categories, read our blog post: Discrete vs Process Manufacturing ERP Software: What’s The Difference?
Food ERP software includes complete traceability tools, quality assurance capabilities, built-in compliance and food safety functionalities and inventory management features that reduce perishable food wastage. It also facilitates automated real-time data capture to ensure the integrity and accuracy of your records. To learn more, read our Ultimate Guide to Food ERP.
Specialist vendors will also provide ERP systems for manufacturers in distinct verticals such as fashion and apparel ERP, personal care and cosmetics ERP, fabricated metals ERP and even specific food sub-sectors including fresh produce and beverages.
What’s Better: On-Premise or Cloud Manufacturing ERP?
Once you’ve decided whether to invest in general manufacturing ERP software or an industry-specific ERP solution, there’s another important decision to make: your deployment option.
There are two types of software available to manufacturers: cloud based manufacturing ERP software and on-premise ERP - but what's the difference and which is best for your business?
On-Premise Manufacturing ERP
On-premise ERP, is installed on your company’s servers, so it will only be accessible via specific networked devices you maintain. Your chosen vendor will need to be on-site to deploy the system, and your technology may need upgrading or replacing to be compatible with the latest software packages.
Some manufacturers choose on-premise ERP solutions because business data is stored on-site, and the system uses an internal network connection that is accessible even if your internet connection isn’t working. However, the cost of maintaining and upgrading on-premise software can be significant, and you’re responsible for the software updates, security, IT personnel and related costs.
Pros:
Provides control over the data
Less dependency on vendor
Cons:
Requires high upfront investment
Burden of maintenance and security
Cloud-Based Manufacturing ERP
In contrast, cloud-based manufacturing ERP software can be accessed on any device with a web connection; there’s no need for face-to-face contact. It’s quicker and easier to deploy than on-premise ERP because it can be done remotely—including any technical support you require post-implementation.
Cloud ERP is commonly offered using a Software as a Service (SaaS) model. This means that the upfront investment is lower than on-prem alternatives and ensures that the service provider is responsible for ongoing maintenance, updates, performance and security patches.
A study by Industry Arc shows that the value of the cloud manufacturing market will touch USD 200 billion by 2030, growing at a CAGR of 16.1% from 2023 to 2030. This shows that as more and more manufacturers invest in digital transformation strategies, cloud manufacturing ERP is quickly becoming the gold standard and businesses that delay are not only missing out on significant benefits, but also risk falling behind the curve.
Pros:
Lower initial costs
Improves scalability and agility
Cons:
Less direct control
Higher-long term costs
For more information, read our compelling case for cloud manufacturing ERP.
Things To Check When Choosing a Manufacturing ERP Vendor
Choosing the right manufacturing ERP provider is as important as the features and benefits of the software itself. The market overflows with ERP vendors promising various functionality and capabilities, but choosing one without careful consideration can expose your company to unnecessary risk and ultimately mean you have to replace the system quickly.
1. Vendor Experience and Expertise in Your Manufacturing Industry
Even though many vendors claim to address the needs of manufacturing companies, only a few truly excel in this area. But how do you evaluate industry credibility?
Well, you can start by taking an in-depth look at the features offered for your specific industry—for example, if you’re a food manufacturer, does the vendor offer allergen or catch weight management functionality? And don’t forget to ask for a product demonstration to see these capabilities in action for yourself.
Also, to ensure potential suppliers truly have the industry experience and reputation they say they do, you can review customer testimonials, awards and recognitions, and ask peers for honest reviews.
2. Scalability and Support for Future Digital Transformation Initiatives
You need an ERP solution that can grow with your business. As such, it’s important to check your vendor’s ability to offer a scalable solution that will continue to meet your specific needs as your business grows.
In addition, ERP is often the first system manufacturers implement in their digital transformation journey. If your business is considering other systems—such as product lifecycle management (PLM), overall equipment effectiveness (OEE), electronic data interchange (EDI) software—checking if your potential vendors offer other pieces of the manufacturing software puzzle can help you maintain consistency as you grow your software ecosystem.
3. Support and Training
After implementing an ERP for your manufacturing business, your vendor should address your recurring needs, like training, technical support and system updates. First of all, ask your vendor candidates for a breakdown of what training is included in the initial implementation process and then enquire what packages are available for ongoing support.
In addition, checking what other customers have said about your vendor’s support team and responsiveness is crucial. Remember, ERP is one of the most important manufacturing software systems you’ll implement, so you’re looking for a long-term partner that can offer support and best-practice advice throughout the lifetime of your software.
4. Product Roadmap and Investment in Research and Development (R&D)
As well as industry expertise, you’ll want to ensure your chosen vendor has in-house development teams to continue enhancing the product, as well as a commitment to staying at the forefront of technological advancements.
Whether it’s leveraging new developments in AI, adding new functionality to meet evolving regulatory changes in your industry or keeping on top of security patches and standards, your vendor should be able to demonstrate that their product is enhanced regularly.
Best Practices for a Successful Manufacturing ERP Implementation
We’ve discussed how to pick the right solution for your business, choose a suitable deployment option and evaluate potential vendors. But now, it’s time to look inward at the best practices and actions required of your team to achieve a successful ERP implementation.
First, you need to ensure all your key internal stakeholders are on board with the project. Even with industry-specific manufacturing ERP software and an experienced vendor, your implementation will only work if your colleagues are fully bought-in and willing to get involved. Consider assembling an internal steering group that can help drive the project forward and deploy your ERP solution in a manner that drives rapid value for your organization.
Next, set clear objectives for onboarding your new ERP software with measurable key performance indicators (KPIs) against them. The best way to demonstrate the value of any new technology investment is to agree up-front what you want it to transform first, and to quantify what success looks like so you can demonstrate to senior leaders that you’ve hit your key targets.
Finally, make sure you have a clear plan for your data migration. You’ll want your manufacturing ERP to be an accurate single source of truth, but that means inputting data that’s correct from the start. So now is a great time to evaluate your current data sources, define the standards and consistent fields you’d like to use moving forward, cleanse existing data sets and plan a clear migration plan.
For more information on planning your ERP data migration check out this in-depth blog: 4 Steps for a Successful ERP Data Migration
What ERP Solutions for Manufacturing Does Aptean Offer?
As you now know, choosing the right purpose-built ERP, implementing it effectively and utilizing its full potential will streamline your business operations and help you boost efficiency, customer satisfaction and profitability.
Here at Aptean, we offer a suite of industry-specific ERP solutions, all designed for the specific needs of your industry, whether that’s food and beverage, fashion and apparel, discrete manufacturing and many more. Moreover, we have extensive experience working with manufacturing organizations in various sectors, including automobiles, beverages, chemicals, cosmetics, electronics, fabricated metals manufacturing, food manufacturing, furniture upholstery and pharmaceuticals to name a few.
Combining our extensive industry experience and technical expertise, we deliver advanced solutions to help you conquer your most pressing challenges and continue thriving as your industry evolves.
With dedicated in-house development and support teams—and more than 10,000 customers across the world—you can trust us to be a by-your-side partner, helping you build success, now and in the future.
Get in touch with our industry experts today, or, schedule a personalized demo of one of our industry-tailored ERPs to see how you could benefit.
Related Content


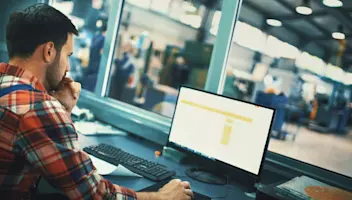
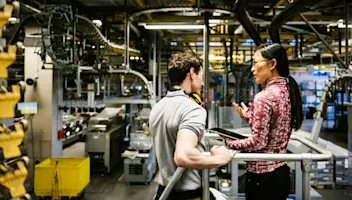

Discover industry-tailored software built by the experts
With deep technical know-how and a commitment to innovation, we deliver tailored software to businesses like yours. Reach out today for your free, no-obligation consultation with an industry expert.
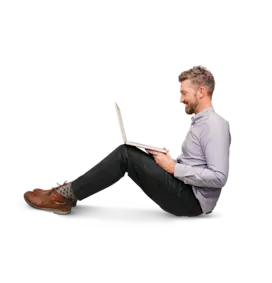