Aptean Industrial Manufacturing ERP, WorkWise Edition - Master Production Scheduling
Aptean Industrial Manufacturing ERP, WorkWise Edition - Master Production Scheduling
Aptean Industrial Manufacturing ERP, WorkWise Edition - Master Production Scheduling
29 May 2020
Aptean Staff WriterHeadline
- Making True Time-Based Manufacturing a Reality
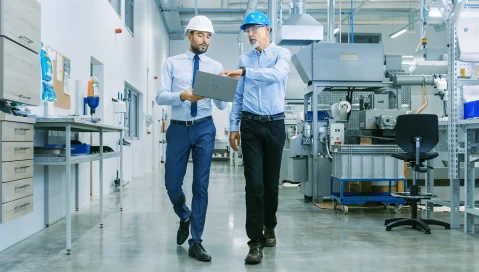
What is a Master Production Schedule?
A Master Production Schedule is a plan that outlines which individual commodities should be produced in each time period such as production, staffing, inventory, etc. This type of plan is typically linked to manufacturing because it helps to indicate when and how much of each product is needed.
Establish A Consistent Production Schedule
The MPS (Master Production Schedule) application is typically the most critical function in a Ship from Stock / Make to Stock (MTS) environment. Creating a solid Build Plan that both balances the supply and demand and provides feedback on the accuracy of your forecast is critical. It ultimately provides a stable environment for your production area, which is a key to efficiency.
A Master Production Schedule increases your material requirement predictability by establishing a consistent production schedule that considers both forecast and customer orders. Best of all, your customer service is improved through available–to–promise features that allow you to check item availability and to quote an achievable promise date.
Master Production Schedule Benefits
Avoid Scheduling Mishaps. Helps your company avoid last minute scheduling and shortages.
Efficient Company Distribution. Efficiently allocate company resources and cost control.
Simple Data Recalculation. Easily recalculate the schedule if change in demand occurs.
Master Production Schedule Key Features
Net Change and Regenerative. Allows a quick analysis after changing a time fence or other calculation factor.
Demand Consumption. Production can be based on Forecast or Actual, whichever is greater or a Reach Back/Look Forward formula that smooth’s forecast error.
Demand and Planning Time Fences. Multiple Time Fences are provided to allow the consumption formulas to vary based on time frame.
Rough-Cut Capacity Planning. A sanity check of the Production Plan against critical work areas and other resources can help avoid downstream problems by pointing out unrealistic production requirements.
Planning Bills. Family groupings can help to smooth forecast error by forecasting at a group level and then distributing the forecast by % to the members of the group.
Safety Check. Can be optionally used to protect swings in demand and can be either located at a time fence or pro-rated between the demand and planning time fences.
Exception Notices. Alerts to potential problems allow the Master Scheduler to adjust the plan.
Forecast Management. As an alternative to using the Aptean Industrial Manufacturing ERP WorkWise Edition Forecasting function, base sales or usage data can be loaded from history and then manipulated using multiple techniques such as quantity or % changes, fixed quantities, or ramp-up/ramp down.
At Aptean, we know manufacturing. From computers and electronics to fabricated metals, our ERP is designed to conquer the challenges discrete manufacturers face—today and every day.
Want to find out how our industrial manufacturing ERP, Aptean Industrial Manufacturing ERP, can help your business? Contact us today to chat with one of our experts or schedule a demo to see for yourself.
Request a callback from a manufacturing ERP expert
We’ve got the specialised ERP solutions you need to conquer your industry challenges.
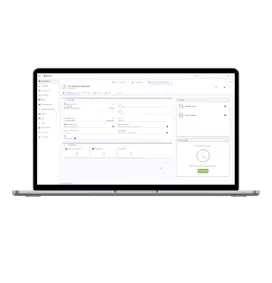