50% of Enterprise Software Users Claim Their Software Cannot Manage Their Processes
50% of Enterprise Software Users Claim Their Software Cannot Manage Their Processes
50% of Enterprise Software Users Claim Their Software Cannot Manage Their Processes
13 Mar 2019
Aptean Staff Writer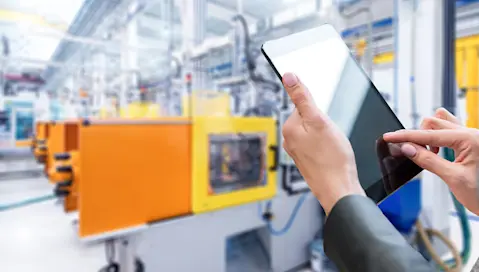
“Nobody ever got fired for buying IBM.”
So goes the popular 1970’s phrase that gave rise to the gold standard of office computers. IBM machines were simply trusted to run the business of so many organizations that the purchase decision was fairly easy.
Today, that same phrase can be used interchangeably with an array of enterprise software systems. ERP, WMS and accounting solutions have grown enormously popular over the past two decades and dominate installations across thousands of organizations in hundreds of industries.
But is the safe option always the best option? Not necessarily, according to the recent State of Software Workarounds report.
Software Users Prefer Industry-Specific Software
Fifty-two percent of all enterprise software users rated their current software as “somewhat effective” or worse in handling processes specific to their industry. More than half of enterprise software users believe their systems are not designed to manage their organization’s specific operational processes. This data suggests a strong correlation between software effectiveness and industry specialization.
Trying to shoehorn a specific process into one-size-fits-all enterprise software systems can be challenging. Food manufacturers often use the same enterprise software to run their organizations as automotive manufacturers. While these operations may share similar functional needs, their operational footprints differ vastly from each other, as do their manufacturing requirements, accounting practices, reporting needs and compliance tracking.
Generic Software Slows Down Production
Implementing generic software solutions can sometimes feel like trying to fit a square peg into a round hole. Making software work within a very specific operational environment may be possible but requires heavy customization and workarounds. Those workarounds have a detrimental effect on production and may only complicate problems further.
As a result, organizations end up modifying their operational processes to fit the requirements of their generic software. The same study noted that 50 percent of organizations admitted to modifying their processes to fit their software. This can be a very effective way to improve your operations when the software is built to handle very specific industry processes and is ingrained with decades of industry best practices, but it can be very worrisome when it is not.
What makes an organization successful often lies at the very heart of its uniqueness. Modifying operational processes to acquiesce to the functional capabilities of a generic solution introduces a great amount of risk. To retain their operational advantage, identifying software that enhances and improves their industry specialization rather than genericizes it is key to increasing efficiencies and speeding up production.
What Happens If You Select the Wrong Software?
Researching, investigating and comparing ERP systems is a very lengthy process. While each buyer’s journey is unique, it generally involves a large team of people from multiple departments whittling down a large list of potential vendors over the course of a year. Considering that most ERP systems take six months to two years to implement, and the system is likely to be in place for the next decade, this due diligence is completely necessary.
Sometimes, even the most diligent search ends in the selection of software that is not a fit. When companies select software that is not built for their industry, workarounds happen. These workarounds slow down production and create opportunities for errors.
The alternative to modifying your processes to fit your software is to abandon the software. When asked if they often resort to the old way of doing things because the new process wasn’t as effective, 50 percent of respondents said yes.
This data sheds light on the fact that many organizations revert to their old ways, sacrificing the control, efficiency, and intelligence benefits of the software. Given the cost and time of this investment, this is a significant sacrifice to make.
In that same study, 47 percent of enterprise software users agreed they were paying for unnecessary capabilities while creating customizations for the things they do need. They felt that their software had features and functionality outside of their needs while they were paying more to make the software fit their processes.
Respondents were clearly frustrated by the difference between what they thought they were buying and what it took to achieve the functionality they needed. Fifty percent agreed that their software vendors are still building out functionality that should be standard.
One user summed it up perfectly by stating that “it’s frustrating to know that you will have to ‘wait’ and ‘request’ changes to be developed and implemented then pay for changes that should be included in the software from the start.” When the wrong software is purchased workarounds become necessary, and they become a new organizational problem.
“It takes entirely too much time to manage the various workarounds. Typically we are the ones who put a stop to them.” Workarounds spawn other workarounds that then require processes and procedures to manage, creating more inefficiency and opportunity for error.
Calculating Your Next Steps
Determining the best way forward is ultimately a calculation of short-term pain versus long-term impact. Will continual tweaking of software solve process issues, or will it only delay the inevitable as it becomes harder to upgrade, integrate and add new functionality?
Changing course by moving to industry-specific software may not be the most attractive short-term option, but doing nothing could end up being the most costly and painful option of all.
Learn how Aptean’s ERPs can produce better results for your business. Contact us today, or request a personalized demo.
Related Content


Request a callback from a manufacturing ERP expert
We’ve got the specialised ERP solutions you need to conquer your industry challenges.
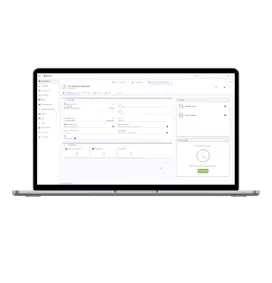