How Are Fabricated Metal Manufacturers Adapting to New Market Demands?
How Are Fabricated Metal Manufacturers Adapting to New Market Demands?
How Are Fabricated Metal Manufacturers Adapting to New Market Demands?
24 Mar 2022
Andy Pickard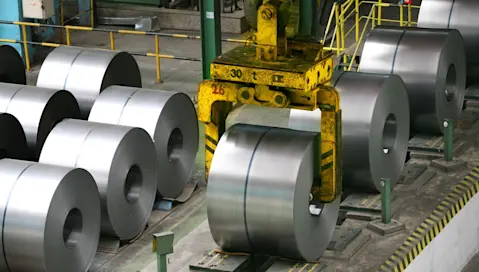
The mood is buoyant in fabricated metal manufacturing. 96% of organizations predict their sales and revenue will increase this year, according to new Aptean research, driven by recovery and growth in the construction and commercial air travel sectors.
But while confidence is high, metal fabricators are operating in markedly different conditions than they were 18-24 months ago. The pandemic and other global events have impacted people, processes, suppliers and customer relationships. And managing these changes means becoming more agile and technology-driven.
To help fabricated metal manufacturers navigate changing market demands, Aptean has produced a new ebook, Pedal to the Metal: How Can Fabricated Metal Manufacturers Accelerate Company Growth?
Here are four of the key challenges our ebook covers—along with strategic guidance on how to meet industry challenges head-on:
Challenge 1: Finding Skilled Manufacturing Workers
Although the level of automation in manufacturing is increasing, people are still pivotal to business success. Yet many organizations are struggling to maintain their full workforce.
44% of the fabricated metal manufacturers we surveyed said skills shortages were their top barrier to growth in 2022, while 28% cited staff shortages as being a critical issue. As metal fabrication has a higher percentage of smaller businesses than many other manufacturing sectors, shortage of ‘boots on the ground’ can significantly impact production rates, which in turn affects customer delivery capabilities.
Rather than worrying about recruitment issues, however, many manufacturers are looking at how to strengthen the role and value of their existing workforce. And digital manufacturing software plays a pivotal role in maximizing employee productivity.
Our research found that 62% of fabricated metal manufacturing companies want to formally capture insights through technology, to minimize the impact of staffing changes. And half (52%) want better contingency planning, so that tech can enable their employees to work effectively, even during periods of market volatility.
Many metal fabricators are also automating business processes to reduce their reliance on manual operations. Among the top technology investment areas are quoting and estimating (52% of companies have already automated this task) and calculating bill of materials (which has been automated by 48% of fabricated metal manufacturers).
"The pandemic and other global events have impacted people, processes, suppliers and customer relationships. And managing these changes means becoming more agile and technology-driven."
Challenge 2: Dealing With Supply Chain Disruption
The pandemic and other global events disrupting the manufacturing supply chain have been well documented. But they’re still a major discussion point for metal fabricators, who are facing continued material shortages and delays.
56% of the fabricated metal manufacturers who participated in our research said their lead times remain longer than usual, which is much higher than the general manufacturing industry average of 32%. And these delays are impacting the end customer experience; 64% admitted to extending customer deadlines as a result of supply chain issues.
While supply network constraints are beginning to ease, fabricated metal manufacturers need to reorganize the supplier model to protect their business from future disruptions. But how?
For most metal fabricators, supply chain technology is the solution. Only 28% of organizations have automated supplier management currently, which is much lower than the general manufacturing industry average of 42%. Deploying digital workflows will enable manufacturers to view the impact of supply changes and respond quickly to future disruptions, to limit their overall impact. It’s also worth noting that 56% of fabricated metal manufacturers intend to spread their orders across a wider number of suppliers in 2022, with many investing in nearshore sourcing to counteract international vulnerabilities.
Challenge 3: Accurately Managing Inventory
We’ve mentioned the impact of supply chain disruption on customers already, but that’s not the only area where metal fabricators are experiencing problems. Constant fluctuations in material availability also make inventory harder to manage.
According to our research, 1 in 4 fabricated metal manufacturing companies believe maintaining inventory levels is a major business challenge. And almost a third are struggling to align their production schedule with available inventory, making production stop/start at times.
Forward-thinking manufacturers are solving this issue by prioritizing inventory management in their digital transformation strategies. By automatically matching available materials with current and upcoming orders, they’re able to maximize output even during times of supply chain uncertainty.
And with 64% of fabricated metal manufacturers planning to automate inventory management over the next 12 months, digitized decision-making will soon become the standard way to safeguard production from stock-outs.
of North American fabricated metal manufacturers plan to automate inventory management over the next 12 months.
Challenge 4: Achieving End-to-End Traceability
With market demand accelerating, many metal fabricators are managing more work orders than they were pre-pandemic. Delivering on these demands means maintaining speed of production while ensuring high levels of quality control and compliance; something that challenges many organizations.
Only half (56%) of fabricated metal manufacturers are currently able to trace materials from end-to-end, which means a significant percentage of companies still have gaps in their visibility. This leaves them vulnerable to regulatory and reliability issues, which can affect the quality, legality and regularity of customer deliveries.
Using integrated data insights to drive production make it much easier for metal fabricators to increase their pace of work without compromising on quality. However, many organizations aren’t able to trace components through the value chain because they aren’t adopting end-to-end processes.
To deliver long-term performance and scalability, fabricated metal manufacturers need a holistic digital transformation strategy.
Targeted technology investment can solve a particular problem quickly and effectively. But using niche solutions to optimize every operational area creates a costly, complex infrastructure. Instead, companies should be considering solutions like fabricated metal ERP software, which enhance multiple business areas through one platform.
Connecting Operations to Solve Critical Metal Fabrication Challenges
After a difficult couple of years, it’s encouraging to see fabricated metal manufacturers feeling confident about the year ahead. But they must optimize operations, adapt to market disruption and prepare for future change if they want to convert sentiment into sales.
Establishing a well-considered digital transformation will accelerate automation, particularly if it incorporates fabricated metal ERP software to connect end-to-end operations and solve problems across the workforce, supply chain and inventory management.
Download your copy of Aptean’s fabricated metal manufacturing report for further insights and growth strategies. Or book your free fabricated metal ERP demo to see how our technology transforms critical processes.
Related Articles

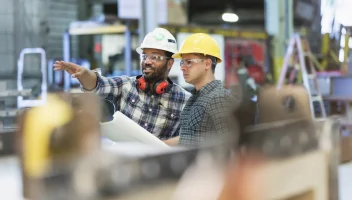
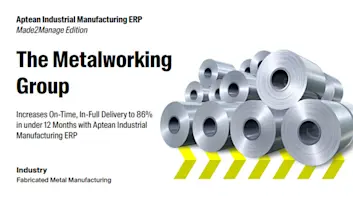
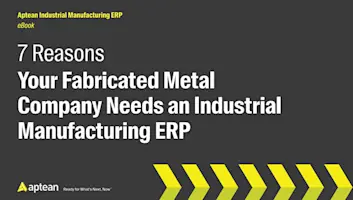
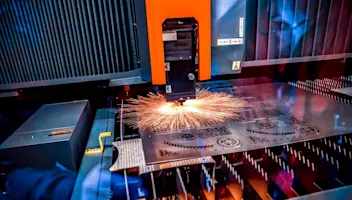
Start transforming your operation today
If you’re ready to take your fabricated metals business to the next level, we’d love to help.
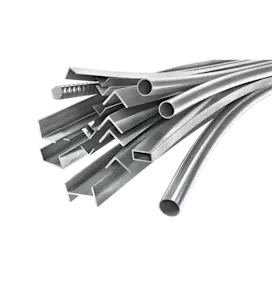