Featured in this post
Achieving Success With Equipment ERP: How to Maximize Your Efficiency
Achieving Success With Equipment ERP: How to Maximize Your Efficiency
7 Dec 2023
Aptean Staff Writer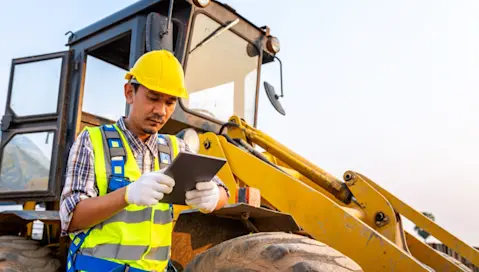
In the ever-changing industrial machinery world, leveraging technology to master the art of equipment dealer management isn't just a choice—it’s a decision that defines the future of your business. This is especially worth considering if your organization still employs inefficient manual processes that deter growth.
The utility of enterprise resource planning (ERP) systems stands out in the dynamic industrial machinery and equipment business landscape. From optimizing maintenance schedules to tracking inventory with pinpoint accuracy, an ERP system can be your ally in achieving operational excellence, reducing equipment maintenance downtime and ensuring your capital assets remain at peak performance.
Whether your fleet includes agriculture machinery, heavy construction equipment or power generation, the path to success begins with effective equipment management software.
In this blog, we'll explore the most common challenges faced in your industry, the benefits an industry-specific equipment ERP provides to help you tackle those issues and offer guidance on how to choose the best system to level up your digital transformation.
Let’s dive in and first learn more about the most common challenges your industry faces.
4 Common Challenges That Can Slowdown Your Equipment Management Business
While inventory management is the biggest pain point forecasted by one agricultural equipment manufacturer in a recent article, there are also other industry challenges and those are exacerbated by legacy systems or manual processes that could be holding back your business while limiting profitability and potential growth. These pain points impact equipment sellers, rental companies and service providers across the industry.
1. Complicated Equipment Landscape
Navigating the complex environment of equipment management often resembles a hard-to-solve jigsaw puzzle. Take, for instance, the difficulties involved in managing the data of all your assets. You could be dealing with a diverse array of heavy machinery—excavators, bulldozers, earthwork trucks and more, each with its own maintenance schedule. Consolidating this wealth of information into a cohesive whole becomes paramount for informed decision making.
Furthermore, if you’re still using a legacy system, you’re likely working in a siloed environment and have disparate solutions. This could pose a problem if you have a huge volume of historical data stored in your outdated system that you want to share or access in other software.
2. Balancing Maintenance and Resource Allocation
When you’re executing maintenance planning and resource allocation, striking a balance is crucial. You need to ensure your fleet of heavy equipment, in constant operation, undergoes regular preventive maintenance to avoid unforeseen issues and extends its lifespan. Achieving the right equilibrium in resource allocation for these tasks is difficult if you’re doing everything manually.
Efficiency extends to dealer management as well while managing multiple maintenance and service tasks across various locations can be challenging. You need to ensure every asset you have is always in good shape, so your customers see you as a reliable partner.
3. Rising Cybercrime Incidents
Data security and privacy are now common concerns of businesses. Ransomware, for example, is a serious threat that could create significant costs for your business. In 2022, there were more than 493 million ransomware attacks detected. Sensitive financial data involving transactions with equipment renters or other customers could be compromised, disrupting your operations if one of your staff accidentally clicks a malicious link.
Safeguarding your data against cyber threats and ensuring compliance with privacy regulations is like building an impenetrable fortress—and your sensitive data could be at risk if you’re still using a legacy system.
4. Poor Inventory Management
With complicated components and a variety of machinery models, managing fleet inventory and parts is a rigorous task if your team members still use an outdated system, or even worse, if they’re still jotting important information down on a piece of paper. Optimizing what parts you currently have, or don’t have, in your warehouse is essential to ensure you’re maximizing your resources.
Equipment ERP: A Powerhouse Software Solution
Implementing a robust ERP system brings forth a multitude of benefits, turning everyday operational woes into success stories and helping you address the common industry challenges we just discussed. Unlike generic, off-the-shelf solutions, industry-specific software can help you manage the numerous issues facing your business today.
1. Streamline Overall Operations and Increase Efficiency
Your team could face significant difficulties if equipment data is scattered across various platforms and is still primarily managed manually; communication could be hampered and the chances of inaccuracies increase. Having a single source of truth for data is crucial for heavy equipment manufacturers and dealers.
Consolidation of data to one platform streamlines processes, making it easier for teams to access, update and utilize data effectively across the organization even with multiple locations—taking your business to the next level.
For instance, Equipment Depot, a well-established material handling business in the United States, has a footprint of over 50 service locations in 23 different states across America. Not only does the company have a wide-ranging set of operations but has a diverse product mix ranging from forklifts to telehandlers. Equipment Depot decided to adopt a new, purpose-built platform to address the difficulty in managing its complex operations and have an affordable, fully integrated, long-term solution.
Now, more effectively managing over 5,000 pieces of rental assets after implementing our equipment ERP designed for the needs of serialized equipment dealers, Equipment Depot’s 900-and-counting technicians receive and fulfill service requests in the field, more quickly and efficiently than before.
2. Improve Maintenance Management and Reduce Downtime
Your heavy machinery is the backbone of your operation—your customers cannot afford a sudden breakdown in the middle of a project. Unplanned downtime can wreak havoc on productivity and budgets—and your reputation. Thanks to predictive maintenance capabilities fueled by data analytics, such a common scenario will become a thing of the past.
With equipment ERP you can seamlessly gather data from telemetry devices installed to your assets, predicting when a component might fail. This foresight allows for scheduled maintenance, preventing costly breakdowns and ensuring that projects stay on track.
3. Data-Driven Decision Making
Imagine a situation where you need to make crucial choices about managing your company’s equipment. In the past, the deciding factors were often based on gut feelings and limited data.
However, with advanced reporting and analytics tools, ERP technology does the heavy lifting—allowing you to access raw financial data, comprehensive insights into equipment usage, maintenance history and performance metrics. Accurate, up-to-date information empowers data-driven decisions, leading to optimized equipment utilization and strategic replacement strategies.
Consider the case of Cardinal Carryor, a material handling dealership based in Louisville, Kentucky, related to using a legacy system. After implementing equipment ERP, they were able to increase efficiency in their parts management and accounting processes, have better visibility in their availability tree and make more informed decisions across the business.
Moreover, we all know about the critical compliance aspect in heavy equipment maintenance. Keeping up with regulations and policies can be a daunting task. ERP systems come to the rescue by offering robust tracking and reporting features—helping you ensure maintenance activities are aligned with regulatory demands, giving you peace of mind.
An industry-specific equipment ERP acts as the catalyst, transforming the management landscape into an environment of streamlined operations, efficient maintenance and data-driven decisions—propelling your business toward unprecedented success in the industry.
Considerations When Choosing Equipment ERP
Embarking on a huge project like ERP implementation could be overwhelming if you’re unfamiliar with the process—because your business is unique, you want to ensure the entire organization will benefit from the investment.
While the process is a significant undertaking, choosing the right solution could realize your long-term goal of improving efficiency and functionality in your organization. There are many factors to consider in the planning stages of ERP implementation.
1. Scalability and Customization
Scalability is one of the critical aspects to consider as your fleet grows, and your processes evolve. Your system should seamlessly adapt to accommodate these changes. Additionally, customization options play a pivotal role in aligning the ERP with the specific needs of equipment manufacturers and dealers.
Leveraging a purpose-built ERP system for your specific, tailored requirements ensures that it becomes an asset in your operations, streamlining processes and enhancing efficiency.
2. Integration Capabilities
Efficient equipment management extends beyond the ERP itself. You need to evaluate the integration capabilities of each solution in your list. In today's interconnected world, integrating Internet of Things (IoT) technologies such as the aforementioned telemetry devices and sensor technology is no longer a unique feature—it’s a standard. Real-time monitoring of heavy equipment through IoT integration provides invaluable insights, helping you proactively manage maintenance and optimize resource allocation.
3. User-Friendly Interface and Training
Ease of use and support are also key considerations when selecting an equipment ERP. Choose a solution that has an intuitive and user-friendly interface—like an ERP that’s built upon the Microsoft Business Central platform. This simplifies tasks, reduces training time and ensures a smoother transition to the new system. Additionally, the availability of training and support resources is crucial for a successful ERP implementation, so that your team can harness the full potential of the ERP solution.
4. Vendor Reputation and Support
Software vendor selection is a pivotal decision within the equipment industry—it’s a choice that warrants meticulous consideration. Carefully evaluating reputations and customer reviews specific to your industry is a prudent initial step. Doing your due diligence will reveal how software vendors have delivered for other businesses, shedding light on their proven capabilities.
In equal measure, a comprehensive evaluation of the support services offered by each vendor becomes paramount. A steadfast support system becomes a linchpin in realizing significant operational enhancements, because it can ensure you're fully utilizing the features of the software and choosing a company with a team of industry experts who can offer best practices and advice.
Achieving Business Success Starts With Implementing the Right Software Solution
Implementing an equipment ERP is your gateway to heightened efficiency, reduced downtime and smarter equipment management. Featuring inbuilt scalability, customizations and seamless integration with existing software and IoT technology, our software meets these critical needs in today's competitive landscape.
And what's more, we have your equipment sector in mind—in addition to the aforementioned equipment industry applications, our software could also benefit companies with aerial lifts, earthmoving vehicles, load handling, trucks, trailers, intermodal containers, municipal assets and other similar businesses.
When looking for an equipment ERP solutions partner, consider working with a vendor with collective decades of experience within your industry. Browse our additional articles whether you want to navigate the RFP process, integrate mobile technology, or if you’re considering moving your system to the cloud.
Ready to revolutionize your equipment business? Get in touch with our team of equipment ERP experts today.
Related Articles

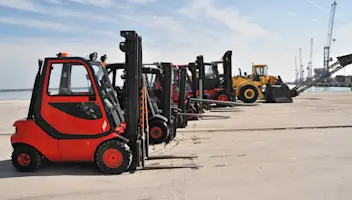
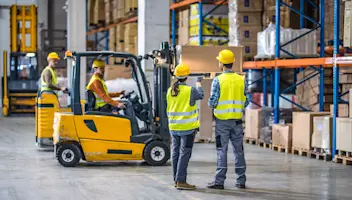
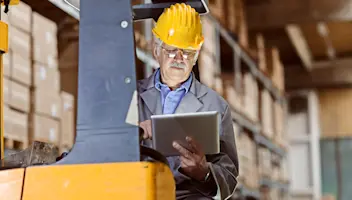
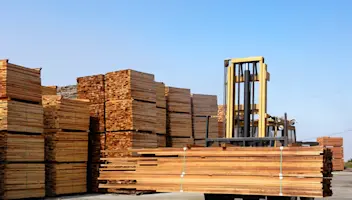
Get in touch today to speak to an expert in equipment dealer management
We’ve got the specialised industry software to help your organisation thrive.
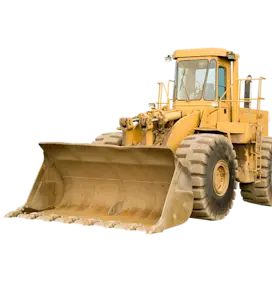