Featured in this post
5 Hidden Costs in Industrial Manufacturing (And How to Reduce Them)
5 Hidden Costs in Industrial Manufacturing (And How to Reduce Them)
18 May 2023
Aptean Staff Writer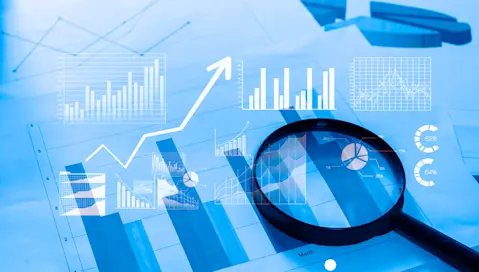
When external costs go up, internal costs need to go down. Otherwise, you’re in a race to the bottom. But are industrial manufacturers finding every opportunity to run more efficient and profitable businesses?
To help you drive growth in a challenging market, Aptean has released an eBook on How to Propel Growth by Reducing Your Cost of Doing Business. However, it’s not just the obvious areas that your industrial manufacturing business needs to optimize.
Often, there are hidden costs within your end-to-end production that can erode your profit margin. Addressing them could prove critical to driving company growth at a time of high material, labor, energy and other costs.
What are these hidden costs in industrial manufacturing? And, more importantly, how can you reduce them? Let’s take a look.
of industrial manufacturers are still reliant on manual quoting and estimating processes.
of industrial manufacturers are concerned about the rising cost of raw materials.
of industrial manufacturers have reducing waste as one of their core targets for this year.
of organizations have already completed digital transformation projects and are realizing the benefits.
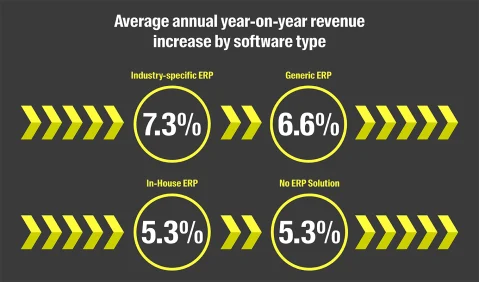
Eliminate Hidden Costs with Aptean Industrial Manufacturing ERP
Driving growth in a challenging market means seizing every opportunity to reduce business costs. By looking beyond the obvious optimizations for hidden costs in industrial manufacturing, you’re finding money-saving opportunities that other industrial manufacturers can’t see.
Of course, identifying these hidden costs is only half the solution. The next step is to eliminate them—something that is much easier to achieve with industry-specific ERP software. Aptean Industrial Manufacturing ERP software is an end-to-end solution for manufacturers in dynamic “to-order” environments.
We have developed industry-specific features onto a fully web-based platform with modern easy-to-learn interfaces. From shop floor to delivery, our ERP for discrete manufacturers delivers visibility, control and efficiency. All of which will help to lower your cost of doing business.
Book a personalized demo of our Aptean Industrial Manufacturing ERP software. Or, for more industry insights, download Aptean’s 2023 Manufacturing Forecast.
Related Content


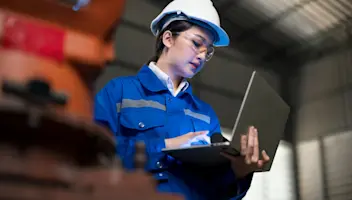
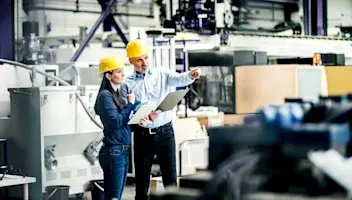
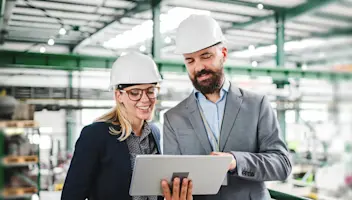
Start transforming your mixed-mode operation today
If you’re ready to take your industrial manufacturing business to the next level, we’d love to help.
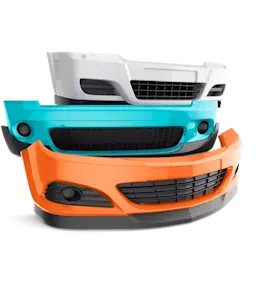