Featured in this post
Three Critical Measures Impacting Your OEE Productivity
Three Critical Measures Impacting Your OEE Productivity
15 Jan 2020
Aptean Staff Writer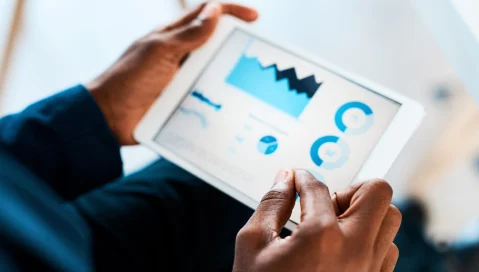
Overall equipment effectiveness (OEE) is a set standard used in measuring manufacturing productivity. In simple terms, OEE is a term used to evaluate how efficiently a manufacturing plant is being utilized. Therefore, we can say OEE is used in manufacturing to help production managers or plant operators determine a problem in their operations, identify the percentage of manufacturing time impacted, provide a solution and provide a standard gauge for tracking progress. It goes without saying the main objective of OEE is continuous improvement.
How Does OEE Measure Manufacturing Productivity?
From the above overview of what OEE is, we can rightly and simply say it’s a powerful measurement. This is for the simple reason OEE is able to provide meaningful data in a single number. There is more than one-way OEE is used to measure manufacturing productivity (i.e. through availability, performance, and quality) and it’s upon the manufacturing manager to interpret it correctly and use the information to significantly maximize their production. More often than not, OEE is used as a benchmark to compare a number of things such as the efficiency of in-house equipment.
Some of the OEE standard benchmarks include the following;
100% OEE. This score is considered perfect production in the sense that a manufacturing firm is only producing quality parts as quickly as possible with no downtime.
85% OEE. This score represents a world-class score for discrete manufacturers and many manufacturers strive to achieve this score as their long-term goal.
60% OEE. This is a normal pass mark score for most manufacturers and it only indicates that there’s room for improvement.
40% OEE. This is thought to be a low score for most manufacturers but it’s a normal score for most manufacturers as they start to track and improve performance. This score can be easily turned around through the adoption of easy-to-apply measures such as implementing OEE or using Aptean MES Objective Edition.
Although the absolute numbers can be meaningful, the most important thing is that there’s a positive evolution and trend and that you can see an improvement in the number because of the actions taken.
Overall Equipment Effectiveness is arguably the best tool for production managers and for improving the performance of employees working on the plant floor. Some of the terms used in the plant floor metrics include:
Target. A term used to represent a real-time production target.
Actual. This is used to represent the actual production count.
Efficiency. The actual percentage (%) of how far ahead or behind the production is.
Downtime. This term is used to represent the time the equipment is not used. This number is updated in real-time and it includes all the unplanned stoppage time for each shift.
Common Terms Used in OEE
Before going into the depths and breadths of overall equipment effectiveness, let’s see some of the common terms you’ll come across;
Fully Productive Time. It simply means production time after all losses have been taken into consideration.
Planned Production Time. This represents the total time a piece of equipment or system is expected to produce.
Ideal Cycle Time. This denotes the time it takes a piece of equipment to manufacture one part.
Run Time. This is simply the time your system has been planned for production and is running.
Total Count. It simply means the total of all parts produced including those with defects.
Good Count. This represents the parts produced that satisfied quality-control standards
Good Parts. This represents the parts that have been produced and are meeting the set standards and consequently do not need to be redone.
Quality. This term is used to describe the manufactured parts that meet quality-control standards.
Performance. This term represents the total number of times there are slowdowns or brief stops in production. As earlier indicated, a perfect performance (100% score) means the operation is running as quickly as possible. The formula for calculating performance is (Ideal Cycle Time * Total Count) / Run Time.
Availability. It is a term used to describe planned and unplanned stoppage time. A perfect score for availability describes an operation that is constantly running during planned production time. It is determined by: Run Time / Planned Production Time.
So, How Do You Calculate OEE?
Perhaps the first stop before we get to calculate overall equipment effectiveness is to, first of all, distinguish the difference between the terms effectiveness and efficiency.
Broadly speaking, effectiveness is the relationship between what is technically possible to produce and the actual product produced at the end of a production period. For instance, if you have equipment which technically can produce 100 products per hour and it produces only 80, then we can say your equipment is 80% effective. Simple, right?
This calculation, however, doesn’t take into consideration many things that go into a production cycle, including; the number of operators, energy and the materials required for the machine to make 80% effectiveness. Therefore, the above calculation does not tell us how efficient the machine is. For instance, let’s say a machine runs at 60% effective when operated by one employee, but the same machine runs at 75% effective when operated by 2 employees. Well, we can say the machine is now running at the effectiveness of 75%, but efficiency has decreased by 50% because of labor.
There are a number of ways of calculating OEE. However, we’ll look at two main ones in this article:
Simple Calculation. This is arguably the simplest way of calculating OEE and it is determined by the ratio of fully productive time to planned production time. OEE = (Good Count x Ideal Cycle Time) / Planned Production Time.
Preferred Calculation. It is a commonly used formula and it’s arrived by taking into consideration three OEE factors (availability, performance, and quality). OEE = Availability x Performance x Quality. The term must have been coined due to its all-inclusive nature in calculating OEE. This simply means you not only get an accurate OEE score, how well you’re doing, but also get specific scores in the three factors, thereby letting you know specific causes of your losses.
Availability
Let’s look at the preferred calculation in action. In a certain manufacturing plant, a normal shift takes 480 minutes. Those working as machine operators take breaks during their shift which total 60 minutes. They also do 2 changeovers during the shift with a total of 60 minutes of machine downtime resulting in an overall total of 180 minutes of lost time. Therefore, we can calculate the availability by subtracting 180 minutes from the total 480 minutes, which comes down to 300 minutes or 62.5% availability.
Performance
Coming to the performance part of the same manufacturing plant, let’s assume the plant produces 60 products per minute. From the availability minutes (300 minutes) above, the plant is able to produce 18000 products. Let’s assume the machines are not running at a 100% capacity, instead they are running slower at 1.5 seconds of cycle time, thereby slowing the maximum speed by two-thirds. Therefore, the actual performance is significantly reduced to 12,000 products or 66.7% performance.
Quality
Let’s now look at how to calculate the quality part of this manufacturing plant. Say out of the 12,000 units produced, 3,000 don’t meet quality-control standards, thus making the quality rate of the units produced to be 75% i.e. (12,000 – 3,000 defects) / 12,000 * 100 = 75% quality.
From the above data, we can now calculate the OEE by multiplying the metrics of Availability x Performance x Quality = OEE.
OEE = 62.5% * 66.7% * 75% = 31.25%.
This means the plant has the capacity to produce 28,800, units but it is only producing 9,000 units.
These Are Losses Associated With OEE
As I mentioned earlier, the goal of adopting the Overall Equipment Effectiveness (OEE) program is to eliminate or reduce the most common causes of machine-related productivity loss. They are famously known as the six big losses. These losses are, however, divided into three main OEE categories; availability, performance, and quality.
1. Losses associated with Availability OEE
Losses caused by equipment failure: these are losses coming as a result of equipment not running when it is scheduled for production, thus causing unplanned downtime. Some common examples of equipment failure include; machine breakdown, tooling failure, and unplanned maintenance.
Losses due to setup and adjustments; these are losses due to production downtime caused by changeovers, machine, and tooling adjustments, planned maintenance, inspections, and setup
2. Losses as a result of Performance OEE
Losses caused by idling and minor stops. Commonly referred to as small stops because it is when a machine stops for a short period of time. Idling and minor stops are experienced due to jams, flow obstructions, wrong settings or cleaning. As you can see they are small issues normally resolved by the operator.
Losses due to reduced speed. These are losses experienced when a machine is not running at the highest speed normally referred to as ideal cycle time (the fastest possible time). Reduced speed is sometimes known as slow cycles. Some of the common causes of reduced speed are; bad environmental conditions, worn-out or poorly maintained equipment, and poor lubrication practices.
3. Losses due to Quality OEE
Process defects. These are losses due to the production of any defective part produced during stable production. These parts can be scrapped parts and parts requiring rework. Process defects come as a result of incorrect machine settings, operator or equipment errors.
Reduced yield. They are more or less the same as process defects only that they are produced from startup until stable production is achieved. They also include scrapped parts and parts requiring rework. Just like process defects, reduced yields come about due to changeovers, incorrect settings, and machine warm-ups.
Benefits of Using OEE to Improve Production
Adopting and implementing OEE can prove to be the difference between a great manufacturing plant and a good one. It is the best tool for production managers striving to achieve their production targets. Here are some amazing benefits you’ll get by implementing OEE.
Return on Investment (ROI) for equipment. We all know companies spend a great deal of money on acquiring machinery. So, why don’t you maximize the return on this investment? The simplest way to do that is to use an OEE strategy which will easily see you produce 15% more units using the same equipment and the same amount of time.
Increase competitiveness. It is always the aim of manufacturers to reduce losses during production thus achieving maximum competitiveness. Implementing OEE will help you get real-time data on bottlenecks or production weaknesses thus giving you a chance to take immediate action.
Reduced machinery costs. One of the profound advantages of using OEE is its ability to produce an accurate performance of your equipment so that you know whether it’s working efficiently. Another great advantage of using OEE is the alerts it gives you on potential machine breakdowns and repairs. This allows you to address the issue before it gets out of hand, thereby reducing maintenance costs and downtime.
Maximize workforce productivity. OEE provides crucial information on the reasons why you experience operator downtime, gives you productivity data and points out long changeovers or setup times. You can use this information to appropriately allot resources, determine where excess capacity is occurring and help you decide whether you need new employees.
Easily visualize performance. In essence, OEE is all about visibility. It is all about visualizing the production process from the beginning to the end, thus letting you visualize production problems instead of having to rely on your best guess. By doing so, you can easily see what’s working and where improvement is needed.
How OEE Is Managed by the MES and WMS
Technically speaking a manufacturing execution system is a system whose main purpose is to connect and monitor machines and work centers on the factory floor. The objective of MES is basically to improve production efficiency and ensure the effective execution of manufacturing operations.
It can be argued that MES is one of the foundations of an integrated, connected Manufacturing Operations Management (MOM) environment. In its simplest terms, Manufacturing Execution System (MES) can be seen as an automated control system designed to manage and monitor all the work-in-process (WIP) on a factory floor.
The Aptean MES and WMS Objective Edition
Aptean is the solution leader in MES and WMS integrated software and services for the optimization of production and logistics operations. Our software solution serves as the management and operator interface between state-of-the-art ERP systems and a broad variety of production machinery. This gate-to-gate solution positions our clients to achieve their goal of mastering manufacturing and system transparency, improving operational efficiencies, realizing meaningful data and increasing corporate profitability.
The Aptean MES Objective Edition system is an integrated single-platform solution that combines MES (Manufacturing Execution System) and WMS (Warehouse Management System) to solve complex processes and discrete production logistics.
Dynamic performance that generates significant ROI value - increased OEE, reduced lost inventory, reduced logistics movement and inventory count, and more.
Solves “Track and Trace” quality management issues with an integrated MES / WMS. Helps meet regulatory requirements and eliminate audit issues.
Easily integrates with your ERP systems and PLC / SCADA / IIOT machines.
One standardized configuration for your multi-site operation and 24/7 system support.
Warehouse Management: Gate-To-Gate Material Flow Handling and Traceability
Gain complete handling and tracking of all material movements in your plant from supplier receipt to customer shipment. The solution provides detailed material traceability and inventory inspections, including Lot and Serial Nr Level. This single platform solution provides real-time integration between production and logistics.
Production Logistics Engine provides just-in-time and just-in-sequence delivery of components to the production line — check stock, release stock, group pick tasks, check tasks to the group. Perform value-added logistics, such as kitting and repack, as an extra service for the end customer.
System Direct Logistic Task Tool displays the optimal usage of people and transport resources.
Task Interleaving and Storage Management achieves optimal task movement and storage processes, including bulk stock, pallet stock, mobile racks, staging, high bay areas, and AGV’s.
Production Management: Optimize Processing Operation and Production Output
Achieve optimal production levels from your machine and human resource capabilities with this single solution. The system defines how to produce your product using version-controlled bill-of-material and bill-of-routing specifications. It handles detailed shop floor production order planning and release. So, you can easily adjust production planning from a timeline view and all related operations will optimize automatically. The easy-to-use operator production view gives your operator start and stop control and the ability to complete order related registrations. And the system ensures all labeling and printing are correct and easy to manage (e.g. best before date).
Register — automatically or manually:
Manhours and machine hours.
Production output data and determine Yield, First Time Right, Scrap & Repair KPI’s.
Process alarms and interrupts including non-order related indirect operator hours (e.g. meeting time).
Product registration.
Material Management: Material Traceability to Stock Status and Lot/Serial Registration
Get detailed registration of consumed bulk or pallet-based components and output in real-time. The solution enables full material traceability by inline registration of the lot and/or serial number for Lot Genealogy reports and full product passports. View the real-time stock status and availability right on the production line.
Quality Management: Track and Trace Production Quality With SPC
Manage and define quality checks, inputs and measurements to be completed manually or automatically throughout the entire production order process. Define detailed operator instructions to enable paperless work at the operator station. Then attach documents and standard operating procedures to a production order. The solution enables a fully automated setup of machine parameters and line printers. Use the double sign off the option to restrict release until validation by a second user.
Summary: OEE’s Impact to Your Bottom Line
OEE has been used in the recent past to give a glimpse of how well a manufacturing process is doing. While that’s one of its main objectives, the true value of implementing OEE will only be seen by using those metrics to improve; since what gets measured gets done. OEE improvement is one of the continuous improvement measures that impact the bottom line of businesses. The value of OEE can be quickly seen in less machine downtime, better quality and more product out the door which equals more profitability.
So why not consider what Aptean MES Objective Edition and Aptean WMS Objective Edition can do to help you improve your OEE efficiency today? Contact us or schedule a personalized demo.
Related Content
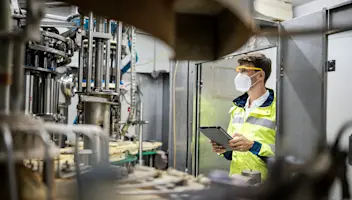
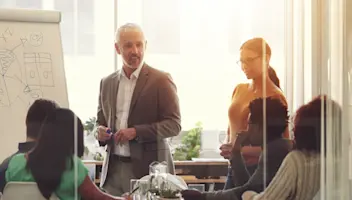
Discover industry-tailored software built by the experts
With deep technical know-how and a commitment to innovation, we deliver tailored software to businesses like yours. Reach out today for your free, no-obligation consultation with an industry expert.
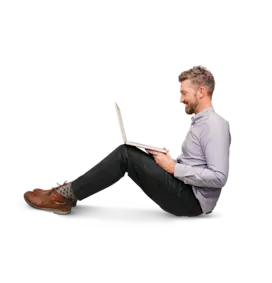