Why a MES System Is Critical for Food and Beverage Manufacturers
Why a MES System Is Critical for Food and Beverage Manufacturers
Why a MES System Is Critical for Food and Beverage Manufacturers
2 Oct 2019
James Wood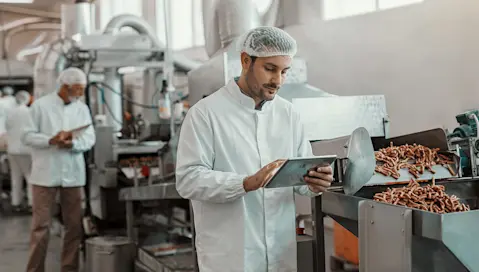
For many food and beverage manufacturers, keeping up-to-date with the newest technology isn’t high on the priority list, especially for mid-size companies who don’t have a ton of money to invest. The thought of integrating technology into their company seems not only expensive but also daunting. Sometimes taking that big, scary step, however, makes everything easier in the long run.
For food and beverage manufacturers, a fit-for-purpose manufacturing execution system (MES) could be used to shift your company culture towards one of continuous improvement and action.
Integrating an MES solution into your company’s operations should be handled carefully. Price, compliance, and the overall learning curve that come with any technology installation of this nature are common, and the idea is that eventually, all employees should be able to assimilate and feel confident without feeling overwhelmed.
An MES solution can be a positive change for companies of all sizes.
How Can MES Software Optimize a Shop Floor?
The shop floor is one of the most critical components of a manufacturing company. It’s where the magic happens. However, machines break, and human error is not uncommon. Without a well-oiled shop floor, the company cannot continue to perform at a rate that’s needed to turn a profit.
To stay ahead of the curve, manufacturers need a solution that will help their employees work smarter and more efficiently. That’s where MES software comes into play.
The right MES solution will help any manufacturing team run the shop floor more smoothly and strategically. The ability to make quick, confident decisions in real-time is the key to staying competitive. This is impossible with the pen-and-paper method as it requires pulling data and an after-the-fact approach, both of which take time.
MES software can do more for food and beverage manufacturing companies than traditional management. It has the ability to:
Optimize your shop floor on-the-go.
Identify issues or potential problems before they happen.
Integrate easily with existing systems.
Empower employees with the data and insights to make manufacturing smarter.
Remove non-value adding actions and anecdotal evidence of losses.
Build a reputation of trust and quality with the supplier base using auditable, quality data.
There are problems that companies face industry-wide, many of which can be remedied with an MES solution. Let’s take a look at a few of the most common issues food and beverage manufacturers face to determine how MES software can help.
Problem 1: Production Overheads Are Rising
Food manufacturers are facing undeniable global economic uncertainty. The cost of raw materials is rising, and there’s been a devastating global labor shortage. Energy and distribution costs are also on an upward trend and further squeeze manufacturers’ margins.
Every cost increase unequivocally impacts manufacturers’ bottom line. So, what can be done?
When it comes to raw materials, the best thing manufacturers can do is to make sure their shop floor and overall operations are both consistent and efficient. In terms of labor, companies can reduce overtime shifts, which makes for a leaner environment.
An MES solution, combined with a structured implementation program, can quickly and easily analyze performance and trends based on shifts, crews, individuals, materials, equipment, production lines, products, and packaging.
The right MES software can identify opportunities for improvement when it comes to performance, product innovation, and food safety, as well as bottlenecks in the factory supply chain. With this technology, manufacturers are able to analyze product costs relative to targets to better gauge overall cost and profit analysis.
With MES software, end-to-end yield tracking is more accessible. Companies can identify causes of yield loss from batching to packaging in order to reduce manufacturing costs. This helps to improve the overall plan attainment.
Problem 2: Compliance Requires Greater Diligence
Food safety is a significant issue for food manufacturers. One compliance mishap could mean a world of trouble for companies large and small.
Imagine a regulator walks into a potato chip manufacturing plant and picks up a bag of chips. He/she examines the bag and then requests to see every quality record from when that bag of chips was produced. The task would be nearly insurmountable if every part of the process was recorded on paper.
Traditional methods, because of their lack of control and consistency compared to more advanced technology, leave room for reputational risks. Human error is a risk in itself when it comes to compliance and quality control.
How can MES software help with compliance and quality control?
This technology eliminates room for error by:
Tracking checks in real-time.
Alerting the right team or person if something needs attention.
Flagging check items to ensure quality, which removes the need for human “checkers.”
Eliminating falsification, pencil-whipping, and data manipulation.
Launching checks into the operator workflow each hour to remove the reliance on watch and check.
Best of all, MES software can provide a complete audit trail at the click of a button, which saves the manufacturer the time and human resources that traditional methods would typically require.
MES software is built to optimize the shop floor by providing accurate data, real-time alerts, and more transparent communication between employees and teams. Food and beverage manufacturers can’t afford to slip up on quality control and compliance, and MES software minimizes the effort without compromising the diligence.
Problem 3: Integrating Technology Comes With a Steep Learning Curve
The tried-and-true pen-and-paper method is still around for a reason—it’s reliable. Having a paper trail of the daily intricate manufacturing details is reassuring. Not to mention, adopting a tech solution can be a challenge for many companies-- not everyone is tech-savvy, nor does he/she necessarily have a willingness to change.
However, the benefits of embracing a culture of technology shouldn’t be overlooked. The state of the industry isn’t predicting a shift toward a technology-first mindset; it has already shifted.
How are food and beverage manufacturers supposed to keep up with the sweeping change?
Selecting a technology solution that is both easy to learn, and that does everything the pen-and-paper method can do but better is a surefire path to successful integration. Food and beverage manufacturers need an MES solution that can not only fit into their current processes but improve them.
The Aptean Factory MES is equipped with features that help manufacturers work smarter, not harder.
The Aptean Factory MES allows companies to do the following easily:
React to problems and implement solutions faster.
Drive continuous improvement company-wide.
Measure factors like downtime, labor, plan attainment, and changeovers in real-time.
Remove band-aid solutions for a more efficient shop floor.
Gain transparency across the company.
This MES solution is complete with role-specific views and offers 12 different languages for its users, which makes onboarding easy and efficient. Also, there’s no coding or programming required; it’s a complete out-of-the-box solution.
This new wave of technology can be intimidating, so selecting MES software that reduces the friction among employees and provides visibility across your company is essential.
Embracing Technology Will Ensure Survival
For most food and beverage organizations, there’s an existing mentality that integrating technology into business is complicated and invasive, but avoiding technology will only make it harder to compete in the future.
The goal of adding software to your shop floor is to increase margin by producing more sellable products and by reducing costs. Though this initially comes at an additional cost, the return on this investment is going to benefit the business in the long-term and add value to the bottom line. Being able to measure a tangible return is what sets up a company up for lasting success.
Adding technology to the shop floor is only as complicated as the company makes it. Start by rolling out simple things, like tablets, so employees can become familiar with the software. Once that becomes a natural part of your operation, more can be added and customized to increase your efficiency.
There’s a technological solution for every company—you just have to choose the right software.
Want to learn more about how MES software can help optimize your company? Contact us today, and let’s get started.
Food Insights
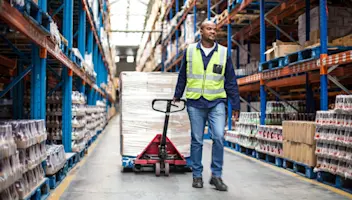
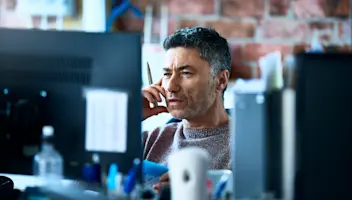
Get in touch today to speak with an expert in your industry
To grow your business, you need a food ERP built specifically for your industry challenges. We're ready to help—reach out today and we'll help you find the right solution.
