Aptean Apparel Shop Floor Control Case Study: Carhartt
Aptean Apparel Shop Floor Control Case Study: Carhartt
Aptean Apparel Shop Floor Control Case Study: Carhartt
13 Sep 2021
Headline
- Carhartt Increases Efficiency and Growth With Aptean Apparel Shop Floor Control Software
Carhartt is one of the most recognized brands in North America. It’s known for its signature outerwear, including jackets and overalls, and in recent years, has also expanded its workwear products to serve and protect hardworking men and women both on and off the job in all weather conditions.
Founded in 1889, Carhartt has almost 4,000 associates across its seven manufacturing and distribution facilities in the U.S. and Mexico. The company services many channels, selling direct to consumers and small businesses as well as maintaining a large wholesale retail presence and even operating Carhartt-owned retail stores.
The Challenge
As Carhartt entered a period of rapid growth, the company lacked the strategic technology base needed to scale up and fully support its apparel manufacturing operations. The old system the organization was using didn’t provide real-time production visibility and couldn’t offer enough flexibility in variable operator pay calculations.
Inability to support customizations and scale created a burden for management and IT
Legacy, batch-based systems lacked real-time visibility into production and operator performance, resulting in bottlenecks
Calculating variable incentive pay required manual, time-intensive payroll processes, including gum sheets on the shop floor
Carhartt’s Chief Information Officer, Katrina Agusti recalled the previous solution was all batch processes. “We would print coupons which the operators applied to gum sheets, and then a day later, we would scan all those gum sheets in order to be able to update operator pay and see movement of production through the sewing lines,” she said.
“We were always reacting a day behind, and we didn’t have any insight into what was happening on the shop floor in real time,” Agusti also noted.
“To continue to scale, we needed to get to the root cause of some of the production bottlenecks and really address those permanently.”
The Solution
After an evaluation period, the Carhartt management team selected Aptean Apparel Shop Floor Control (SFC) because they wanted an easy-to-learn system that would create a good associate experience while also provide the depth and breadth of industry-specific functionality the operation needed.
Aptean Shop Floor Control provides Carhartt a real-time manufacturing execution system (MES) that leverages an innovative Android™ app, management dashboard and off-the-shelf tablets running on Wi-Fi networking to collect production data.
This enables real-time manufacturing data collection in order to provide complete visibility into production and operator performance as well as the flexibility to support labor tracking and incentive pay with customizable pay types—solving Carhartt’s biggest challenges with its previous system.
“Our implementation of Aptean Apparel Shop Floor Control went very smoothly. They were very patient, very accommodating and I know that the team feels really good about continuing to invest in the platform.”
The Results
Aptean’s apparel manufacturing software has streamlined Carhartt’s shop floor processes by tracking and reporting the progress of shop floor production in real time. In this way, supervisors, plant managers and supply chain managers all share an understanding of the timing and trends in production, helping them manage costs and quality.
Increased average production line efficiency by 13% overall, across seven manufacturing plants providing the ability to quickly adapt to changing demands
Delivered real-time visibility into production and performance across organization eliminating bottlenecks
Saved 320 person hours per payroll and approximately $60,000 USD annually by eliminating manual payroll work
Real-time data also helped plant and supply chain managers enjoy a macro view of their entire facility, with data to understand whether their lines are running properly, at the right level of efficiency and at target output levels. If they see something coming out of alignment with production goals, they can talk to the production supervisors about their individual areas.
Aside from improving production, Carhartt was able to lower the cost of payroll processing through automation which allows the company to re-assign staff to more important tasks.
Agusti plans to leverage Aptean Apparel Shop Floor Control to find even more ways to strengthen productivity and efficiency at Carhartt. For example, she sees a future opportunity for using real-time equipment data to reduce machine down time, improve preventative maintenance and lower overall maintenance costs on the shop floor. She’s also exploring Aptean Apparel SFC’s tracking capabilities for quality and repairs processes within the finishing center.
“We’re definitely planning to continue to invest in the platform and take on additional capabilities that the solution will offer.”
Choose a Manufacturing System That’s Cut Out for Hard Work
The best manufacturing software streamlines and automates processes, taking the hassle out of your day-to-day operations and allowing your teams to focus on what they do best, creating and selling your products. Not only does this increase efficiency and reduce costs, it also helps you drive profitability and paves the way for accelerated growth.
That’s why Aptean’s industry-specific solutions make the perfect fit for apparel manufacturers. From specialized enterprise resource planning and shop floor control software to product lifecycle management and electronic data interchange, we’ve got all the apparel manufacturing systems you need to keep your business running smoothly and efficiently.
And what’s more, our solutions are all backed by dedicated in-house teams that know the apparel industry inside out. So, you’ll always have technical expertise and best practice advice on hand to ensure you’re getting the most out of the software and driving your business forward.
If you’re ready to take the next step on your digital transformation journey, get in touch with our experts to see our software in action in a quick personalized demo.
Related Content
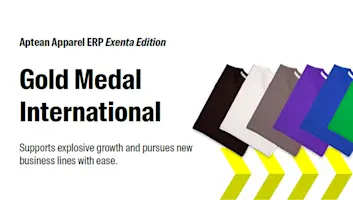
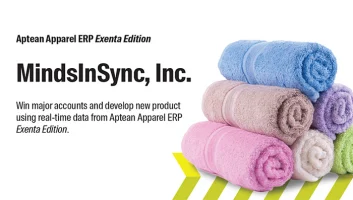
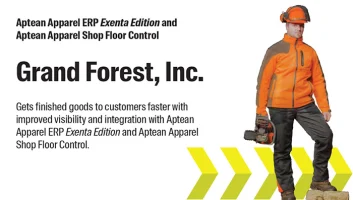
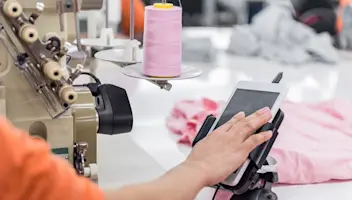
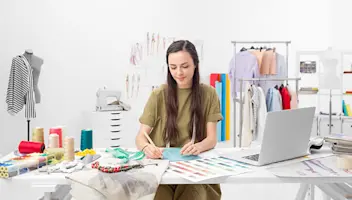
Ready to start transforming your shop floor?
We’ve got the specialized MES solutions you need to conquer your fashion industry challenges.
