The ERP for the
Plastics Industry
Streamline Your Business Processes
DTR delivers tailored features to drive efficiency across all your operations—from production forecasting and scheduling to bill of materials (BOM) management, material requirements projections and production monitoring. And by integrating your core plastics production operations with other business processes, DTR also helps you manage product and project costing, quoting and variance reporting with speed and accuracy.
Accelerate Production
With increasingly short lead times, you need a reliable system to easily and accurately determine required materials for production. DTR’s scheduling tools provide production management with detailed information—driving strategic decisions about what to produce, when to produce it and what resources to use. This data eliminates repetitive calculations and paperwork and helps shorten production cycle times. It also minimizes waste and provides instant feedback in response to changing situations on the shop floor.
Strengthen Customer Relationships
DTR centralizes customer data and provides real-time order tracking to help you better manage relationships and improve customer satisfaction. The system’s customer relationship management (CRM) stores comprehensive customer and prospect information in a central database that is fully integrated with the ERP. This gives employees across every department easy access to the information they need to identify sales opportunities, nurture customer relationships and improve customer service. DTR’s real-time reporting tools enable precise tracking of customer orders and shipping schedules so you can confidently provide status updates at any time.
Specialized and User-Friendly
Generic ERPs are simply not designed to support the unique workflows of plastics manufacturers, leading to frustrating inefficiencies in your daily operations. DTR is different. Whether you’re an injection molder, extruder, film and bag processor, blow molder, thermoformer or compounder, DTR provides purpose-built functionality to support and streamline your processes—from inventory control and job costing to distribution and financial management. DTR is quick and easy to implement and provides a user-friendly experience for employees in any department.
Start transforming your business today
If you’re ready to take your industrial manufacturing business to the next level, we’d love to help.
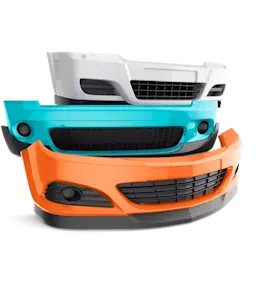