Featured in this post
The Future of Process Manufacturing: Achieving Operational Excellence through OEE Software
The Future of Process Manufacturing: Achieving Operational Excellence through OEE Software
6 Mar 2024
Aptean Staff Writer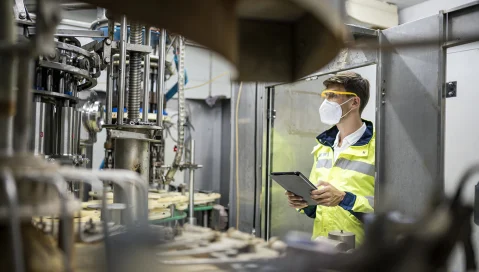
In the process manufacturing sector, overall equipment effectiveness (OEE) is a metric to gauge your operational performance and can be calculated by understanding your plants, availability, performance and quality. While this can be calculated manually, OEE becomes much more powerful when you implement a solution that calculates performance measurements in real time.
Organizations that implemented OEE software in recent years achieved 8.6% higher revenue than those that didn't utilize an OEE system. In recent research conducted by B2B International and Aptean, OEE is among the top five software solutions that companies plan to implement this year.
Are you thinking of deploying a software solution to optimize production and strategically utilize your capital assets? This blog will help uncover the untapped potential within your production processes and elevate shop floor staff productivity with process manufacturing OEE software.
Maximizing Operational Efficiency With OEE Software
OEE software delivers immediate insights into the performance, quality and availability of manufacturing equipment and processes through real-time monitoring.
Leveraging OEE software enables process manufacturers to identify and eliminate inefficiencies, reduce downtime, and enhancing productivity and cost-effectiveness across your operations.
Identifying and Eliminating Inefficiencies
Being an effective tool to optimize your production processes, OEE software provides comprehensive insights into production effectiveness by systematically analyzing equipment; then pinpointing downtime occurrences, whether due to equipment breakdowns, changeovers or planned maintenance. The platform allows proactive measures to minimize disruptions, highlight performance bottlenecks and inefficiencies, and identify factors hindering optimal equipment output.
Here's how OEE software could improve your process manufacturing operations:
Provide holistic performance assessment
Measure downtime duration and impact
Maximize resource utilization
Benchmarking and goal setting for production
Provide opportunities for continuous improvement
OEE solutions identify areas of improvement to enhance efficiency in production processes, ultimately leading to streamlined operations. Moreover, OEE software can help you:
Pinpoint underperforming equipment
Prioritize improvement efforts
Simplify root cause analysis
Align operations with your business goals
Boost accountability and performance
Impact on Productivity and Cost-Effectiveness
Deploying OEE software impacts your production runs' overall productivity and cost-effectiveness. Here are some of the benefits that OEE technology can provide to help improve productivity:
Reduced waste
Faster throughput
Minimized downtime
Improved quality
Better resource allocation
Enhanced competitiveness
For cost-effectiveness, OEE solutions directly contribute to your bottom line by reducing costs through optimization of operational efficiency—maximizing production output and minimizing downtime.
Improved resource utilization through OEE also helps ensure that your investments are optimized, further enhancing profitability. Additionally, enhanced customer satisfaction resulting from consistent quality and timely delivery by leveraging OEE solutions directly impacts your bottom line by fostering loyalty and repeat business.
Customer Spotlight:
Gehl’s Achieves Growth and Continuous Improvement with Aptean Process Manufacturing OEE
Customer Spotlight: Gehl’s Achieves Growth and Continuous Improvement with Aptean Process Manufacturing OEE
Gehl's, originally a creamery founded in 1896, shifted its focus in the 1960s to produce sterile, non-refrigerated dairy products, notably their renowned cheese sauces. Today, Gehl's supplies its flagship products, including nacho cheese, to various establishments nationwide, from restaurants and convenience stores to movie theaters and cafeterias.
Implementing Aptean Process Manufacturing OEE has proven instrumental for Gehl's, facilitating a significant increase in productivity. By enabling real-time monitoring of process performance and assisting in the analysis of root causes for delays and scrap, Aptean OEE has empowered the company to enhance its output effectively. This heightened efficiency has enabled Gehl’s to meet rising order volumes and has also ensured the organization's financial stability and growth.
Empowering Your Workforce With a Purpose-Built OEE Solution
Empowering your workforce with an OEE solution involves several key steps to ensure that employees understand and leverage the benefits of the tool effectively. In your process manufacturing facility, OEE technology positively shifts your workforce dynamics where your business can now understand how you are performing against your targets at any given moment.
OEE is like a scoreboard for your shop floor. Imagine that you have real-time monitoring of production lines and detailed insights into equipment performance. Operators and technicians alike are equipped to swiftly detect and rectify inefficiencies, including bottlenecks and quality deviations. Frontline employees can troubleshoot issues, optimizing processes to minimize downtime and maximize throughput immediately.
Here's how an OEE solution can help empower your workforce and provide valuable insights:
Specialized process training optimizes specific production procedures for enhanced efficiency
Ownership and accountability drive personal responsibility and reliability
Real-time data accessibility enables continuous process monitoring
Resource allocation optimizes process efficiency
Continuous learning initiatives drive ongoing development efforts
Cross-functional collaboration enhances the problem-solving capabilities of your workforce
Complete visibility into performance to align with organizational goals
Fostering Collaboration Culture
OEE promotes teamwork by offering a unified framework and metrics that streamline communication, problem-solving and shared accountability. It facilitates collaboration through shared goals and objectives, enhanced transparency and visibility, cross-functional cooperation, root cause analysis and knowledge sharing. The collaborative approach cultivates a continuous improvement and teamwork culture, driving organizations toward operational excellence.
Staying Ahead of the Curve
OEE harnesses real-time data from the shop floor, delivering actionable insights and a holistic view of production and quality. The platform's focus on optimizing plan attainment and overall equipment effectiveness equips you to make strategic decisions and propel operational excellence forward.
By seamlessly integrating real-time metrics and intuitive technology, our software swiftly identifies manufacturing losses, tracks product costing, measures OEE and fine-tunes plan attainment. With the capability to adjust key metrics in mere seconds, the platform ensures optimized plan execution and operational efficiency. It also has a continuous improvement module that helps manage and prioritize process improvement initiatives.
Customer Spotlight:
Monogram Foods Leverages Aptean Process Manufacturing OEE for Greater Accuracy, Visibility and Efficiency
Customer Spotlight: Monogram Foods Leverages Aptean Process Manufacturing OEE for Greater Accuracy, Visibility and Efficiency
Monogram Foods, a leading U.S. food manufacturer since 2004, has seen impressive growth, with over 3,000 employees across ten facilities in six states. However, expansion brought challenges, including outdated paper-based record-keeping, leading to data inaccuracies, reporting delays and a lack of actionable insights for informed decision-making.
The company is delighted with the significant enhancements brought about by the adoption of Aptean's Process Manufacturing OEE solution for the food and beverage industry. This system has catalyzed improvements across various fronts, notably in transparency and productivity, leading to a tangible boost in overall performance.
Looking Towards the Future of Process Manufacturing With OEE From Aptean
OEE aligns with the evolving industry trends influenced by technological advancements, shifting market demands and sustainability initiatives.
As part of your continuous improvement journey, OEE software integrates with Industry 4.0 technologies, shifting toward sustainable manufacturing processes. The platform's data analytics capabilities help in identifying and eliminating inefficiencies, empowering your workforce and increasing your operational productivity.
Now that you grasp the potential of a robust OEE system, it's time to consider your options. While many OEE software claim to be a one-size-fits-all solution, they might not meet your specific needs. Unlock your operations' potential with Aptean Process Manufacturing OEE, seamlessly integrating data management, streamlining processes and empowering your workforce.
Furthermore, Aptean Process Manufacturing OEE’s rapid implementation timeline—as short as four weeks in some cases—accelerates access to actionable insights and analysis, empowering you to make informed decisions that directly impact your bottom line.
Are you ready to elevate your manufacturing operations with OEE software? Reach out to us today. For further insights, check out this helpful article on how to build a business case for process manufacturing OEE.
Related Content

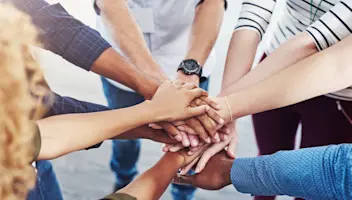
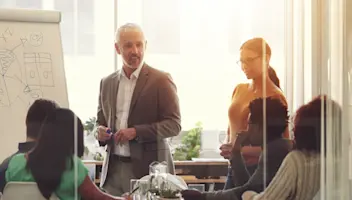

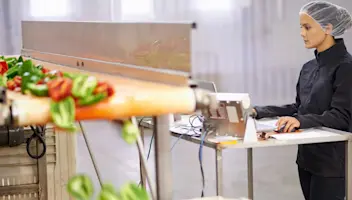
Ready to start transforming your business?
We’ve got the specialized OEE solutions you need to conquer your industry challenges.
