How to Drive Better OEE and Increase Productivity by 34%
How to Drive Better OEE and Increase Productivity by 34%
How to Drive Better OEE and Increase Productivity by 34%
25 Aug 2020
Aptean Staff Writer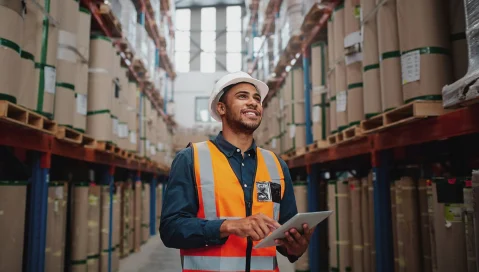
It's no secret that the world has been transforming at an alarming rate.
Global change had been accelerating socially, politically and demographically for years before the coronavirus exerted unprecedented pressure in the market this year. The pandemic has created a level of uncertainty that is shaping the buying habits of customers. Demand has been fluctuating in a way that's hard for manufacturers to anticipate, which creates a necessity for agility on the shop floor so that businesses can adapt to unpredictable changes in demand.
In addition to the pressures from the coronavirus, costs have been rising at multiple angles — from transportation to raw materials to energy costs to everything in between. This shrinks margins.
To combat the pinch in margins, improving the efficiency on the shop floor is vital. For example, the more unscheduled stops there are in production, the longer the machines will have to run to get the required product out the door. This has a substantial impact on both energy and labor costs. Having access to better, more visible and actionable data aids manufacturers to tackle these inefficient losses sooner rather than later, enabling margins to be maximized.
To stay competitive, visibility into the entire supply chain is necessary. Robust ERP solutions give access and visibility into many of the critical business functions — such as finance, sales and demand, and logistics and planning. Not having the right system in place on the manufacturing shop floor, however, can lead to a severe information gap between the ERP and the automation and control layer.
For example, as soon as the production plans get released onto the shop floor, it can be hard to view actual progress, preventing you from seeing issues as they emerge. It could be the fact that the changeover took 30 minutes longer than you had planned or that you had too much downtime or because you'd rejected too much product.
All of this can make it very hard to anticipate how this is going to affect the ability to satisfy customers. Closing the information gap and shining a light on those problems in real-time with the right system dramatically increases manufacturers' ability to stay agile to customers.
Manufacturers that do not have the right system in place often use manual or paper-based recording devices to monitor production performance on the shop floor. Many limitations can arise as a result of this. The data collected can be inaccurate, not be in real-time, be open to individual interpretation, and most importantly, it can go unaccounted for because data is often missed.
It's because of these constraints that when it's time to review the information (usually a day after it has been captured), it's filed away never to be seen again because the unreliability of it makes it almost impossible to be utilized for continuous improvement effectively.
The right manufacturing execution system (MES) can help mitigate those gaps in data collection and efficiency. Aptean Axxos OEE helps manufacturers achieve a substantial performance uplift with a focus on these four pillars:
1. Immediacy — This isn't just about making sure that operators have access to the right KPIs and the right metrics; it's about ensuring they're given closed-loop feedback so that they're empowered to make positive adjustments to improve and streamline production throughout the day.
2. Visibility — Real-time visibility into all the different types of losses you're experiencing. Whether that's time-based losses like downtime or slow running, right through to changeover variance and quantity-based losses like rejects and rework. If you don't know about it, you can't improve it.
3. Consistency — Connecting directly to automation, Axxos OEE is a standardized solution that can be scaled regardless of the types or ages of machines. This gives you a common platform that can be used to drive continuous improvement from operator to operator through to the entire plant network.
4. Accountability — Acceptable conditions can be created on the shop floor, creating an environment where everybody has a direct level of responsibility. Different role-based outputs within the solution align this to everybody within the chain of command.
Aptean Axxos OEE is your best choice when it comes to significant performance uplift. Not only is the software out-of-the-box ready, but it's built for your specific industry needs. It can align with your existing practices and provide you with visibility throughout your entire enterprise.
But don't just take our word for it. Our customers' successes speak for themselves. After implementing Axxos OEE, Epiroc, a rock drilling tools enterprise, was able to increase its availability by 45% in three years and reduce its machine downtime-type errors by 50%. Similarly, Nordiq Habo, a leading manufacturer of metal components for industrial and automotive industries, was able to increase its availability by 24% in 18 months and increase its productivity by 34%.
If you'd like to talk more about how Aptean Axxos OEE helps to overcome internal and external manufacturing challenges, please reach out. We'd love to talk.
Start transforming your business today
If you’re ready to take your discrete and industrial manufacturing business to the next level, we’d love to help.
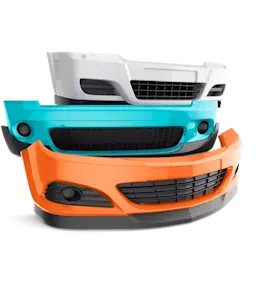