5 Ways Cycle Counting Improves Warehouse Inventory Accuracy
5 Ways Cycle Counting Improves Warehouse Inventory Accuracy
5 Ways Cycle Counting Improves Warehouse Inventory Accuracy
16 Oct 2019
Aptean Staff Writer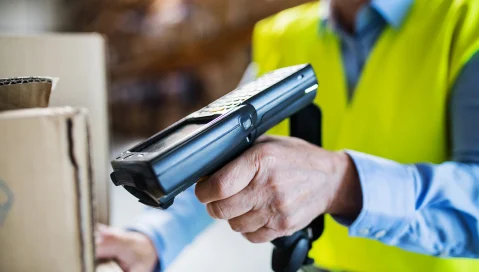
“Physicals” are a natural event for many organizations. It allows managers to gain clarity and insight into their current inventory accuracy. Natural as it might be, it is an incredibly costly exercise. Not only does it strike fear into the hearts of those who have to count every piece of inventory in the facility, but it is excruciating for warehouse executives.
Inventory inspections drive accuracy within the four walls of a facility, but they completely disrupt operations, thereby eliminating any potential revenue for the time they are down. They are dependent on labor, requiring overtime pay. They also reveal significant gaps in accuracy that were likely unknown before the inspection, and more importantly, often remain a mystery following.
No matter how sophisticated your warehouse operations are, inventory accuracy is a continual challenge. In this 24/7, omnichannel economy, warehouses are now living, breathing ecosystems that require constant attention and care. Processes to increase accuracy should interweave into daily fulfillment tasks like picking, packing, and shipping.
The answer is Cycle Counting with a cloud warehouse management system. Most facilities run anywhere from 95% – 98% accuracy within their warehouses with legacy technology and paper-based practices. Those operations now have to compete against facilities operating at 99.999+ accuracy, backed by state-of-the-art cloud technology.
What is Cycle Counting?
Cycle counting is periodic counting of inventory within a warehouse to ensure that the physical inventory at the bin location matches the count reported in the warehouse management system.
The theory behind cycle counting is that counting a smaller percentage of items on a more regular basis will lead to greater overall accuracy. These frequent inspections significantly reduce errors thereby maintaining incredibly high accuracy rates across the entire facility. The benefit is that organizations using this practice of inventory control can perform inspections at any time with little or no oversight. Cycle counting simply becomes a normal function performed during downtime, or it is assigned to specific workers.
How Does Cycle Counting Work?
That process is entirely based on what is right for each facility. Organizations control their inspections by dynamically selecting what they want to inspect.
For instance, you may prioritize the highest-value or fastest moving items for more regular inspections as those tend to be more prone to errors. You may also incorporate seasonal items or peak season items when appropriate.
After selecting the items for inspection, staff on the floor follow step-by-step instructions right on their mobile device to perform the inspection.
As cycle counting occurs, real-time updates are sent to management, who can immediately request recounts. If the final count does not match what is in the system, you can make a stock adjustment right from the floor, or create a discrepancy report and move to the next item.
5 Ways Cycle Counting Improves Accuracy
Here are 5 ways that cycle counting, along with a cloud warehouse management system, can improve accuracy in your warehouse.
Elimination of Physicals In a legacy technology or paper-based environment, physical counting requires a substantial amount of up-front planning, not to mention work stoppage. You can eliminate downtime, overtime pay, and the dedicated resources required to perform physicals with a cycle counting.
Better Utilization of Employee Time Continuous process control, verification, and validation of inventory costs lead to a much more productive fulfillment center. Overall labor productivity will increase as associates spend more time moving product and less looking for it.
Higher Fill Rates Better meet customer demand with an improved first-pass yield. With a higher fill rate, you will eliminate backorders and lost sales.
Identify the Root Cause of Issues Physicals determine accuracy issues within your warehouse, but cycle counting goes much further by helping you to determine the underlying causes of problems. You can run analytics against these checks and tie the issue back to a vendor that is pushing bad products or an employee that is stealing.
Better Purchasing With regular cycle counting, your team will benefit from a higher confidence in the accuracy of your system counts. This certainty of information enables managers to make better purchasing decisions, yielding more efficient use of warehouse capacity, improved space utilization and less capital tied up in excess inventory.
The Future of Accuracy in Warehouse Management
Facilities utilizing sophisticated cloud warehouse management systems, RFID, and cycle counting by ABC stratification, can increase inventory accuracy to 99.999% at the bin location.
Still, that is 1 error out of 1,000 orders. With organizations shipping 1,000,000+ orders a day that ratio compounds to a significant number. So even with near-perfect accuracy, there’s still the need for continuous improvement.
That means getting humans out of the process. With advances in drone technology, vision and voice scanning, and artificial intelligence, fulfillment processes will get faster and even more accurate, creating an even wider gap between technology-centric warehouses and organizations yet to embrace cloud technology. Is your warehouse management team excited about the prospect of near-perfect inventory accuracy? It's possible with cycle counting with a cloud-based WMS. Contact our team of WMS experts today to get started.
Related Blogs
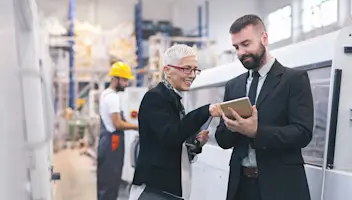
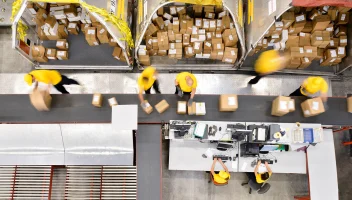
Ready to start transforming your business?
We’ve got the specialized WMS solutions you need to conquer your industry challenges.
