Featured in this post
Key Considerations for Inventory and Demand Planning in the Food Industry
Key Considerations for Inventory and Demand Planning in the Food Industry
5 Jul 2023
Aptean Staff Writer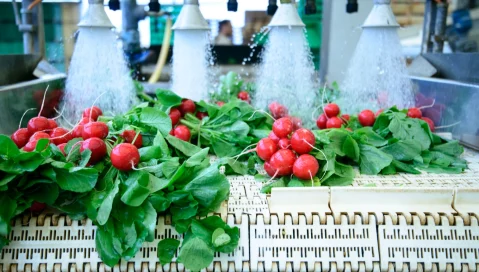
For food and beverage businesses, not having complete visibility and control over the supply chain can lead to disruption of operations, lower customer satisfaction and a host of other headaches. As a professional in the industry, you’ve likely faced these issues in the past and would prefer to never deal with them again.
What does that take? Good supply chain management involves precise food and beverage demand planning, inventory management, a complete understanding of plant capacity and intelligent scheduling. You need to dive deep into your data and prepare yourself for both the immediate future as well as long term.
A significant hurdle for many food and beverage manufacturers that are aiming to improve their supply chain management is that they simply lack knowledge of sound forecasting and planning techniques. They might rely on outdated practices or in-house procedures that are less based on science and more on convenience.
If you really want to achieve results on this front, you’ll have to familiarise yourself with the most up-to-date forecasting methods. One key will be realising that projections at the item or location levels will be far less reliable than those at the aggregate level. Thus, it’s a better idea to focus on the high-level estimates and then use proration to dial in on the item and location forecasts.
The figures derived will inform practically all of your processes, including scheduling and shipping. With time and the right technology—namely, an industry-specific enterprise resource planning (ERP) solution—your forecasts will become more accurate and have a positive impact on operations.
A Deeper Understanding of Inventory Policy
Safety stock, reorder point, batch size and customer service levels—these are just some of the variables that make up your inventory policy. Such a nuanced, complicated topic can be a bit intimidating, but it’s vital to prioritise this part of your business to meet demand.
First, you need to know the real value of your “days of supply” and “cover period” metrics. You likely already use these in your planning efforts, but be wary of oversimplification. If your approach in the past has been to take annual demand and divide it by the number of forecast periods to calculate your needs, you’re missing out on key factors like seasonality, trends and carrying and production costs.
You also need to know how to vary your approach based on the volume of your products. Low-volume products should be produced less frequently and with a longer cover period to minimise changeover costs. High-volume products, on the other hand, should be produced more frequently and have a shorter cover period. And for all of your products, expiration dates will also be vital to consider to minimise waste.
Then, there’s the matter of safety stock. With lower safety stock, service levels are higher, and vice versa. The correlations between all these numbers are important to understand, as once you have a firm grasp on these principles, your business can achieve greater satisfaction and not suffer the burden of keeping larger-than necessary inventory on-hand.
There are critical questions that your employees should be asking when conducting demand planning in the food industry, but they don’t necessarily need to be able to provide the answers themselves—again, this is where technology comes in. An effective ERP system with robust forecasting tools can take into account all of the many factors necessary for accurate projections and provide dependable results.
Long-Term Planning Horizons
Clearly, the timeframe for which you are forecasting will determine your flexibility in acting on the numbers and what measures need to be undertaken. If you’re looking at the long term and using the typical 12-months-out paradigm, the precision of your estimates will be critical, because they’ll have long-lasting, business-wide implications.
Just what will be impacted by these projections? Budgeting, distribution and production planning are just a few of the processes that will hinge on long-range forecasts. A systematic approach will be necessary for your supply chain to remain reliable over a longer period.
If you’re successful in finding the right platform that can factor in the vast quantities of data that good demand forecasting requires, you’ll see benefits of greater stability, less reactive decision-making, adequate but not excessive inventory levels, higher customer service levels, increased throughput in manufacturing, greater confidence and reduced freight costs.
Medium-Term Planning Horizons
With solid forecasting techniques and accurate estimates, medium-range planning for distribution, inventory levels and demand allocation based on plant capacity can be made. Before attempting to create a master production schedule (MPS), however, it will be necessary to establish inventory levels for finished products on a location-by-location basis.
An important tool for this task is your inventory policy system—it should help the planner set safety stock levels, reorder points and reorder batch sizes based on target customer service levels. Keep in mind that location is also a consideration in these processes as well.
The inventory policy system will inform your distribution and production planning and formalise your business’s approach regarding the tradeoffs between inventory investment and service levels. Obviously, your goal will be to meet service levels while holding a minimum of inventory, and having the right system and procedures in place will be crucial to make that a reality.
Short-Term Planning Horizons
While production planning drives longer-range plans from demand forecasting, shorter-range production plans will involve resolving the replenishments of stock at distribution centres, including warehouses that ship to customer locations. If a third-party logistics provider is part of you distribution network, there may be additional challenges. The end goal is to ensure that each location has sufficient inventory to meet demand and as little excess as possible.
This is a task for your distribution requirements planning system, which will determine the appropriate frequencies and volumes of shipments from the plants to distribution centres while also taking into account plant capacities.
A good distribution requirements planning system can make your business more efficient on several fronts by reducing transport costs, improving customer service levels, reducing outages at your warehouses and facilitating communication between sales, distribution and production teams.
Unexpected short-term changes in demand are inevitable, but between better forecasting and an established process for warehouse replenishment based on real data, you can expect fewer disruptions, less contention and reduced costs.
Comprehensive Production Planning
Now, with inventory levels set at the location level, production planning can occur. Your system should cover months, weeks and days and carefully calculate the balance of capacity, labour and inventory.
The system must also operate on a model that accounts for demand requirements, line capacity and formulations required to meet the demand quantities and dates. It’s ideal if it also has the capability of simulating various hypothetical scenarios and can itself consider solutions based on the variables at play.
Your main objectives in this process are to resolve staffing, materials and capacity issues on weekly and monthly bases, as at that level your planners can leverage metrics like average run rates to balance the quality of plans with ease of maintenance of the system.
A potential key differentiator at this step are modern advanced planning and scheduling (APS) tools that can model production by factoring in batching rules, alternative routing and recipes, changeover logic, sequencing rules and more. Some APS technology can also facilitate optimisation of multi-constraint environments, shelf life considerations and allergen management.
The benefits of utilising advanced APS techniques include:
Faster planning
Increased stability of plans
Reduced overtime
Optimised labour utilisation
Fewer changes to daily schedules
Improved customer service levels
Ideal inventory levels
Better plan throughput
Decreased changeovers due to better sequencing
Own Your Demand Planning Processes With Integrated Food ERP Software
Considering that better forecasting can reduce estimation errors by 15% and implementing a solid system can help increase plant output by 10% while reducing inventory levels by 20%, the potential benefits are clear.
But, good demand planning in the food industry relies on many factors. Firstly, having accurate inventory levels at a moment’s notice is crucial, as well as complete formulation information. Forecasting requires past sales data to determine realistic figures. Distribution requirements planning also needs accurate inventory figures; and capacity planning can’t be performed without a good understanding of your plants’ potential outputs and the business’s recipe formulations.
What ties all these systems together and ensures that the data necessary for the many required calculations is available? An ERP solution purpose built for the food and beverage industry.
As a unified platform, a food and beverage ERP can provide complete information from across all your departments to the supply chain planning system, resulting in dependable forecasts.
When it comes to choosing your ERP, you need to be confident in it's ability to offer sophisticated functionalities that will continue to drive your business forward. After all, you'll be making important decisions that affect profitability based on your forecasts, so understanding the scope of your potential platform and being able to trust in its accuracy and performance is absolutely vital.
That's where Aptean comes in. Our expertise has been proven over decades of working with food and beverage manufacturers just like you and is evidenced in our specialised and award-winning industry-specific food ERP system. You can rely on our relentless commitment to delivering innovative solutions and our team's dedication to being a by-your-side-partner throughout your digital transformation journey.
Contact us to hear more about how Aptean Food & Beverage ERP can transform your food and beverage demand planning as well conquer your other industry challenges. Contact us today or schedule a demo.
Boost Efficiency in Your Production Cycle
If you’re ready to take your food or beverage business to the next level, we’d love to help.
