Featured in this post
The Power Trifecta of Process Manufacturing: ERP, EAM and OEE Software Solutions
The Power Trifecta of Process Manufacturing: ERP, EAM and OEE Software Solutions
14 Dec 2023
Aptean Staff Writer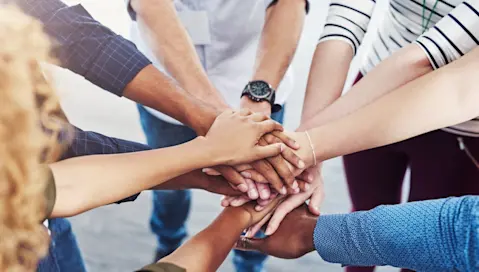
For organizations in the chemical, nutraceutical, cosmetics and personal care or other related process manufacturing industries—rising production costs, supply chain disruption and reduced consumer demand are the top three factors that are hindering growth, including surging inflation and material availability.
The Manufacturing Institute foresees that around 2.1 million manufacturing jobs could be unfilled by 2030. To alleviate the effects of this skill and labor shortage—63% of manufacturers leverage digital transformation to automate more tasks, based on the 2024 Manufacturing Trends and Outlook report for North America.
In this blog, we’ll talk about industry-specific software solutions: enterprise resource planning (ERP), enterprise asset management (EAM) and overall equipment effectiveness (OEE). This manufacturing trifecta helps process manufacturers like you to bring operations forward despite the growing challenges and future hurdles.
The Power of Industry-Specific Software Integration
ERP, EAM and OEE offer substantial benefits to process manufacturers. However, the true magic happens when these systems are integrated seamlessly, forming a cohesive ecosystem that propels manufacturing operations to its full potential. This synergy empowers you to operate with greater efficiency, precision and profitability.
Integrated software solutions offer process manufacturers like you these advantages:
Real-time data exchange: Information from EAM and OEE seamlessly integrates into the ERP system, providing a holistic view of operations.
Optimal efficiency:These solutions help ensure precision in production and market the most with the resources you have.
Streamlined workflows: Automate processes and workflows across your manufacturing operations, reducing manual data entry and human errors.
Regulatory compliance: Many industries face strict regulatory requirements. These solutions can help companies maintain compliance with ease through built-in features. Track raw materials, ingredients and finished goods at every production stage, ensuring compliance with industry regulations—providing comprehensive reporting and analytics.
Now, let's delve into the advantages offered by each manufacturing software solution.
Unified Manufacturing Operations With ERP Software
Enterprise resource planning software serves as a centralized database and offers a suite of applications, enabling companies to streamline operations, boost efficiency, make data-driven decisions and enhance overall business performance by facilitating real-time data access and smooth information flow across different departments.
You can harness these benefits by implementing ERP software in your operations.
Enhanced efficiency: ERP systems automate routine tasks, reducing manual data entry and the risk of errors. This results in faster decision making and increased productivity—enabling better tracking of customer interactions and order processing, enhancing customer satisfaction.
Optimized inventory: Avoid overstocking or understocking with real-time visibility into inventory levels, helping to reduce waste and costs.
Rigorous quality control: Implement strict quality control measures, identifying and rectifying issues before they become costly problems. Maintain precise control over recipes and formulas, making real-time adjustments to meet quality standards.
Real-time reporting: The platform offers robust reporting tools, making it easier to analyze data and generate valuable insights for better decision making. Centralized data ensures that all departments work with accurate and up-to-date information, which reduces data discrepancies and enhances collaboration.
While ERP systems offer numerous benefits, using a generic solution may require expensive customizations. However, by deploying an industry-specific ERP purpose-built for process manufacturers, you will get more out-of-the-box features and capabilities. You should carefully plan and manage the ERP selection and implementation process to align with your unique business needs.
Selecting the right ERP system is crucial. Companies should consider factors such as the size of their organization, industry-specific needs, scalability and the ability to integrate with existing software.
"Make sure you understand your business processes before you attempt to slap software on top of them. You've got to know what your business processes are so that you can define them correctly and not accidentally chose a path you think is right."
Maximizing Asset Performance and Reliability With EAM Software
Enterprise asset management systems enable businesses to extend the lifespan of their assets, minimize downtime, cut operational expenses and enhance asset performance and reliability. Features like asset tracking, maintenance scheduling, work order management, spare parts inventory and purchasing can help you achieve your target.
Through preventive maintenance, EAM anticipates machine downtime before affecting your operations – an effective and proactive approach to asset management.
Now, let's explore the advantages of EAM software deployment in process manufacturing operations.
Benefits of EAM in Process Manufacturing
Preventive maintenance: Maximize the lifespan of expensive machinery, reducing the need for unexpected capital expenditures. EAM software allows organizations to schedule and automate preventive maintenance tasks, reducing the risk of unexpected breakdowns and costly downtime.
Reliable asset tracking: Collect equipment performance data, identifying issues before they impact production. EAM software provides real-time tracking of assets, offering detailed information on their location, condition and performance. This data helps organizations make informed decisions about asset allocation and maintenance schedules. Hence, you’re able to determine the type and frequency of maintenance issues on an asset.
Cost control: EAM software enables cost tracking for each asset, helping organizations identify cost-saving opportunities and make informed financial decisions. With EAM, organizations can efficiently manage spare parts and inventory, ensuring they have the right materials on hand when needed, reducing excess inventory costs.
Metrics That Matter To Elevate Your Performance With OEE Software
Overall equipment effectiveness software is a tool used in manufacturing to measure and analyze the efficiency and performance of production lines—monitoring the availability, performance and quality of production processes, giving a full picture of your operations.
The system is a holistic metric that measures these factors:
Availability: The amount of time that equipment is available for production.
Performance: The speed at which equipment operates as a percentage of its maximum capability.
Quality: The ratio of defect-free products to total products produced.
OEE promotes continuous improvement—identifying bottlenecks, inefficiencies and directs your focus to areas where enhancements yield tangible results. The software has a constant cycle of assessment and optimization, a commitment to squeezing out every drop of potential from your manufacturing assets.
In process manufacturing, OEE translates operational data into actionable insights, ensuring that every production run is efficient to achieve your target.
Here are a few notable benefits that OEE systems bring to your manufacturing process.
Systematic high-volume production: Identify and eliminate bottlenecks and inefficiencies to improve production capacity.
Optimal equipment uptime: Reduce unplanned downtime through proactive maintenance and improved equipment availability.
Top-notch product quality: Enhance product quality by pinpointing and addressing production issues promptly.
Sustainable continuous improvement: Use OEE data to drive continuous improvement efforts, resulting in better overall performance.
Unlock the Value of a Process Manufacturing Software Ecosystem
The significance of ERP, EAM and OEE in process manufacturing extends beyond the realms of operational efficiency. It's about resilience, adaptability and a steadfast commitment to thrive in an ever-evolving landscape. In the relentless pursuit of continuous improvement and excellence, this manufacturing software “trifecta” can future-proof your business.
Leverage ERP as your strategic foundation while harnessing the power of OEE and EAM for operational performance and asset reliability. These systems, when combined and tailored to specific industry needs, have the power to revolutionize your operations.
Are you ready to elevate your manufacturing game? The future belongs to those who seize it. Embrace change and let's chart a course to unparalleled efficiency, reliability and prosperity.
For more insights and guidance on unleashing the full potential of your process manufacturing operations, don't hesitate to reach out to our experts at Aptean today.
Related Articles
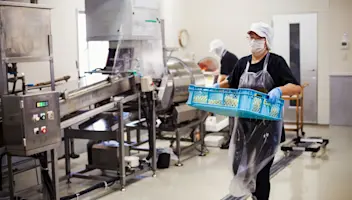
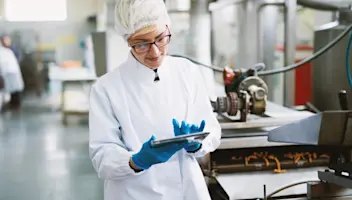
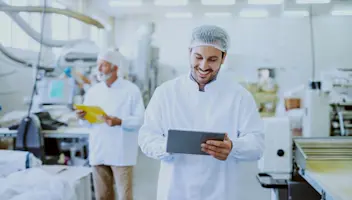
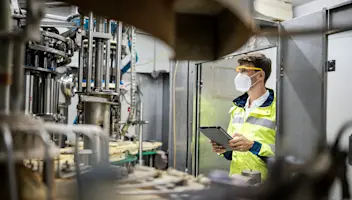
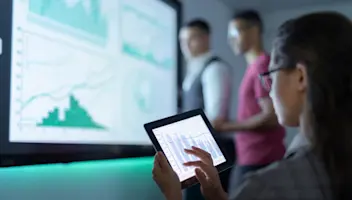
Get in touch today to speak to a software industry expert
To grow your business, you need a purpose-built ERP for process manufacturing. We're ready to help—reach out today for your free no-obligation consultation.
