6 Global Events That Have Disrupted the Manufacturing Supply Chain
6 Global Events That Have Disrupted the Manufacturing Supply Chain
6 Global Events That Have Disrupted the Manufacturing Supply Chain
20 Sep 2021
Aptean Staff Writer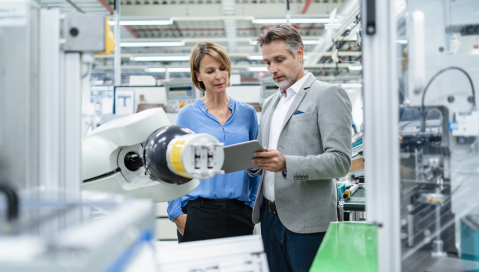
There are parts of the manufacturing process that can be controlled quite easily. There are parts that cannot. The supply chain definitely falls into the second category.
Since the start of 2020, manufacturers across the world have had to contend with new variables impacting the supply of raw materials. And for many companies, these events have put unsustainable pressure on existing supplier networks.
To understand how component availability has affected the flow of production for discrete manufacturers, let’s take a closer look at six major global events that disrupted the supply chain in 2020 and 2021:
1. The COVID-19 Pandemic
When: January 2020 to present Where: Global
It’s an obvious place to start, but we can’t ignore the phenomenal impact of the COVID-19 pandemic on global supply networks. Lockdowns and social distancing measures have influenced every aspect of the manufacturing supply chain—from vendor operations and packaging availability, to transportation logistics across land, sea and air.
For manufacturers, the trickiest aspect of managing pandemic disruption has been the ebb and flow of regional availability. An example of this is the start of the outbreak, when experts warned of a global supply chain crisis after China went into lockdown.
Supply network recovery has also been held back by subsequent strains of COVID-19, including the Delta variant, hitting countries at different times. Even now, strict Antipodean lockdowns are affecting the movement of raw materials. Construction experts are warning that New Zealand has been dropped from the global supply chain due to the severe restrictions in place, and the country’s manufacturing industry has been affected in a similar way.
2. Computer Chip Factory Fire
When: March 2021 Where: Japan
When a power surge sparked a fire at the Renasas Electronics factory in Naka, Japan, damaging 23 machines, the impact of this disaster was felt internationally. It took more than 100 days for the computer chip supplier to return to full production capacity, with Renasas needing to outsource production to vendors in other Asian regions (such as Taiwan) while the company repaired its plant. The automotive industry in particular was badly hit, as Renasas supplies almost a third of the world’s microcontroller chips. This affected the global production of vehicles by brands including Ford, Hyundai and Toyota.
3. Brexit
When: January 2020–present Where: UK
The UK’s vote to leave the European Union in 2016 marked the start of an uncertain time for goods’ movement, and these problems have intensified since the country officially left the EU in January 2020.
While North America has its own trade agreement with the UK, any manufacturers with a base in Europe or reliant on European partners certainly have felt the impact of ongoing negotiations; 43 percent of Britain’s exports are to the European Union.
Manufacturers in sectors including electronics have admitted to supply chain challenges as a result of Brexit restrictions. And legislative red tape surrounding the movement of goods is being worsened by manpower shortages affecting the transport infrastructure; Logistics UK said recently that the UK has a current shortfall of 90,000 HGV drivers, and Brexit has been a catalyst for this shortage.
4. The Ever Given Shipping Container Blockage
When: March 2021 Where: Suez Canal, Egypt
It may have been the source of hundreds of jokes and memes, but the Ever Given shipping container becoming wedged across the Suez Canal had a very serious impact on global supply networks.
Although the vessel itself was freed after six days, the subsequent backlog in traffic caused more than 60 days’ supply chain disruption. According to a Supply Chain Dive article, 62 container ships with a combined capacity of over 727,000 TEUs were held up by the Ever Given, with further vessels delayed by taking an alternative route around South Africa and the Cape of Good Hope.
Around 12 percent of all the world’s trade flows through the Suez Canal, and the Ever Given’s bottleneck led to both a shortage of containers (which pushed up their prices) and many missed handovers to freight transport—yet more setbacks for manufacturers to deal with.
5. Drought
When: 2021 Where: Taiwan
While accidents like the Ever Given can be avoided, there’s nothing people can do to influence the weather. And unfortunately, weather has not been cooperative with manufacturing over the past 18 months.
Taiwan is a powerful example of the impact that weather can have on manufacturing supply chain operations. In the first half of 2021, the country was hit by its worst drought in 56 years, with water availability at the Baoshan No. 2 Reservoir reaching 7 percent; its lowest level on record.
This shortage was highly significant for global manufacturing, as Baoshan is a primary water source for semiconductor production, an industry worth over $100 billion to Taiwan. The drought also impacted vendors’ ability to capitalize on new business opportunities generated by the Renasas Electronics factory fire previously mentioned.
6. The Big Freeze
When: February 2021 Where: USA
It’s not just Asia that has been affected by extreme weather conditions in 2021. During February, the U.S. was hit by a severe storm, which resulted in 73 percent of the country being covered in snow.
One of the worst-hit states was Texas, where a polar vortex generated freezing conditions and led to major power outages. A combination of equipment damage caused by the outages and a lack of reliable energy source forced petrochemical factories, plastic resin plants and petroleum refineries to shut down for the best part of a month.
According to Bloomberg, weather disruption caused U.S. industrial production to drop by more than two percent in February, while manufacturing output dropped by 3.1 percent.
Mitigating Supply Chain Risk in an Unmanageable Market
As these six examples show, the manufacturing supply network is faced by frequent threats, many of which can’t be predicted. But rather than fearing an uncertain future, manufacturers have an opportunity to approach your value chain differently, diversifying the suppliers you work with and mitigating major risks.
Aptean’s latest whitepaper looks at how to increase your supply chain’s strength and stretch, for a resilient model that can still flex with market conditions. So whatever the future holds, your organization is in the best position to weather the next storm, legislative change or roadblock.
Download Strength and Stretch: Increasing Resilience and Agility in your Manufacturing Supply Chain for free now.
Related Blogs

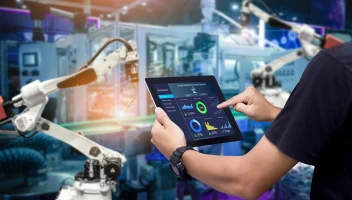
Discover industry-tailored software built by the experts
With deep technical know-how and a commitment to innovation, we deliver tailored software to businesses like yours. Reach out today for your free, no-obligation consultation with an industry expert.
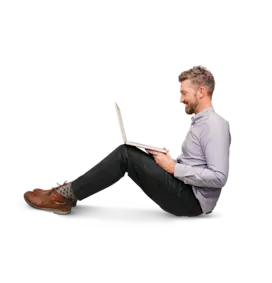