The Benefits of CMMS: Improved Reliability, Cost Savings and More
The Benefits of CMMS: Improved Reliability, Cost Savings and More
The Benefits of CMMS: Improved Reliability, Cost Savings and More
27 Oct 2023
Aptean Staff Writer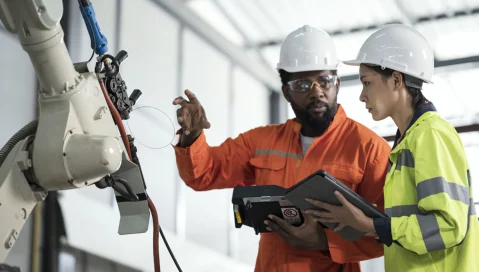
Many organizations seek to empower their workforce by optimizing work processes through software implementation. In fact, over 50% of manufacturing industry leaders and engineers currently utilize computerized maintenance management systems (CMMS) for their production lines and maintenance schedules. The CMMS software market was valued at $960.88 million at the end of 2022 and is projected to grow at a compound annual growth rate (CAGR) of 10.55% through 2028, reaching $1.75 billion by that point.
On-prem or cloud-based CMMS can improve your operations with increased asset reliability and limited breakdowns. The software system helps your business in all aspects of modern maintenance management by improving efficiency, reducing maintenance costs and enhancing productivity—all of which contribute to improved profitability.
Before diving into the benefits of CMMS, let's define what makes for a solid maintenance management strategy for your manufacturing business, especially for those starting their digital transformation journey for manufacturing operations.
The Role of CMMS in Your Maintenance Management Strategy
CMMS is a software platform designed to improve your maintenance operations and centralize related information in one digital platform—helping your business boost its production efficiency while optimizing the use and availability of capital equipment, like vehicles, manufacturing machinery, essential infrastructure and other assets.
A study by the Asset Management Council found that up to 75% of equipment failures can be attributed to poor maintenance practice. Moreover, the average downtime incident costs about $17,000 and manufacturers experience over 800 hours of downtime a year.
Indeed, most manufacturers want to extend the lifespan of their equipment, while increasing the availability of their assets and ensuring that they are more reliable. These goals require close monitoring of manufacturing performance with a solid maintenance management solution.
Over 50% of manufacturing industry leaders and engineers currently utilize CMMS
The Benefits of CMMS in Your Maintenance Management Strategy
CMMS can assist companies of all sizes grow their operations as the software can help manufacturing businesses effectively manage their equipment maintenance tasks, save costs and so much more.
Other software implementation benefits include:
1. Maximize your asset lifecycles and boost operations for manufacturing success.
A report by the Aberdeen Strategy & Research found that CMMS can improve efficiency in maintenance operations by as much as 20%. Routine plant inspections are excellent for getting insight into your asset performance and preventive maintenance schedules are key for preserving asset reliability. A maintenance management solution can help you manage both with specialized, purpose-built features.
2. Precision-engineered preventive maintenance planning for better performance.
Create a strategic and proactive maintenance plan for your capital equipment and facilities. Implementing maintenance management software can help your organization minimize paper-based maintenance processes for planning and scheduling from a central database.
3. Efficient work order and task management for streamlined operations.
Thanks to the real-time framework, work order requests are routed to specific technicians right away, allowing an approval flow across your entire organizational chart. Additionally, your staff members can include attachments – such as images, manuals, checklists and videos – to inform preventative maintenance activities.
4. Cutting downtime and operational costs for unparalleled productivity.
Facilitate efficient capital equipment operations, reduce unplanned downtime and avoid slow production runs—calculating each asset’s “mean time between failures” (MTBF)—which can help you predict, prevent and prepare for the next breakdown cycle.
5. In-depth financial insights and advanced reporting for strategic decision-making.
Easily track the cost of your maintenance activities. As you monitor these expenses, you can generate accurate reports to share with leadership to inform your budgeting process. Aside from tracking maintenance costs, track your employees' work hours, giving you a way to gauge team performance while identifying areas for improvement.
6. Real-time data and accessible history log for empowered visibility.
Document real-time facility and maintenance activities; store detailed records of your repair history per asset. That includes completed work orders, maintenance costs, maintenance schedules, total work hours, spare parts replacement and repair history for complete visibility.
7. Foster system-wide collaboration for effective communication.
Create a single source of truth across all departments in your organization. This centralized information warehouse has every detail of your maintenance program, which increases visibility into critically important facts and figures. Plus, CMMS generates data-driven reports, giving you insight into the overall performance of your manufacturing operations.
A study by the Asset Management Council found that up to 75% of equipment failures can be attributed to poor maintenance practice.
Choosing Your Maintenance Management Strategy Solution Provider
Now that you've learned about the benefits of CMMS, your next step forward is to consider what you need out of a software provider.
Here’s a brief checklist when selecting the best-fit vendor for your manufacturing business.
1. What are your goals and future plans?
This is the most critical question when selecting any software solution. You should focus your search on industry-specific and purpose-built maintenance systems that can future-proof your operations. Identify your goals for conducting preventive maintenance, tracking work orders, generating maintenance reports and implementing technical support.
2. What are your preventive maintenance needs?
A one-size-fits-all maintenance solution may not address all your preventive maintenance needs. Software that provides industry-specific features, with a user-friendly interface, is more likely to cover your requirements.
3. Have you considered scalability?
Where do you see your operations three, five or ten years from now? The ideal provider can let you start your journey with basic CMMS features. As your operations upscale, the solution can allow you to implement additional capabilities based on your needs. (see our next section on a CMMS-Integrated EAM solution)
4. Have you conducted due diligence?
You should request a demo or schedule a discovery call with your prospective maintenance management solution provider and ask them for references, case studies or testimonials. This can help you get a feel for how they work and whether they are a good fit for your organization.
CMMS-Integrated EAM for Your Maintenance Management Strategy
CMMS and enterprise asset management (EAM) solutions are both effective maintenance solutions for your manufacturing operations; however, CMMS solely focuses on asset maintenance and work order management. With EAM you will benefit from all the capabilities of CMMS plus other robust features for inventory management and procurement—monitoring and preserving the entire lifecycle of your capital equipment, from acquisition and installation to repairs and replacement.
However, you don't have to choose between CMMS and EAM software. There are solution providers out there that allow you to implement the features that you need and as your business grows, so can your solution’s feature set. For example, you can start your maintenance management program with basic capabilities for preventive maintenance, initially streamlining your work order requests and obtaining real-time reporting. After you reap the benefits of CMMS and your business continues to scale up, you can easily upgrade to add-on other features like inventory and procurement automation found in an EAM solution. Enter Aptean.
Most companies that implemented Aptean EAM found an 80% reduction in overtime and an overall reduction in man hours by $300,000.
Why Choose Aptean EAM for Your Maintenance Management Strategy?
A sound CMMS has the potential to improve your manufacturing operations. However, when you're thinking about business continuity and future opportunities, you'll see the advantages of choosing an EAM platform that has all the functionality of a CMMS and more to maximize your maintenance management strategy.
Aptean combines both CMMS and EAM features into one software package. Most companies that implemented Aptean EAM found an 80% reduction in overtime and an overall reduction in man hours by $300,000. They've also reduced redundant asset purchases by 75% and spending on spare parts by 23%. Moreover, the system integrates or complements well with other Aptean platforms you may need for manufacturing operations.
Are you ready to optimize your asset performance, maximize equipment uptime, improve asset reliability and streamline manufacturing while reducing maintenance costs?
Explore modern maintenance management solutions with this insightful datasheet covering our EAM solution. Or, have a quick chat with our CMMS and EAM experts today to learn more about Aptean EAM.
Related Articles
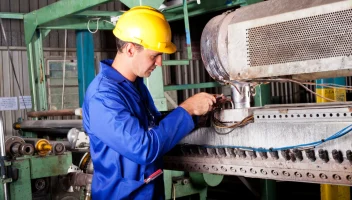
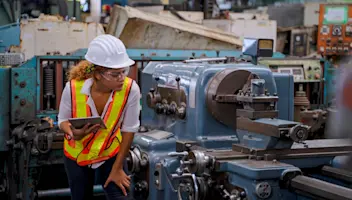
Ready to start transforming your business?
We’ve got the specialized EAM software you need to conquer your industry challenges.
