How Advanced Planning and Scheduling Helps Industrial Manufacturers Boost Efficiency
How Advanced Planning and Scheduling Helps Industrial Manufacturers Boost Efficiency
How Advanced Planning and Scheduling Helps Industrial Manufacturers Boost Efficiency
17 Nov 2020
Jim Tuttle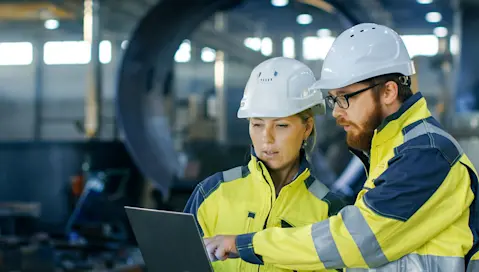
How often do you wish that there were more hours in the day? You could finish a big work project or schedule your shop floor for upcoming seasonal demand periods or wrap up a report that's already a few days late if you only had more time.
There never seems to be enough time.
We haven't figured out how to add more hours to your day, but we do have a solution that optimizes time and efficiency within your manufacturing business.
The planning and scheduling module of an industrial manufacturing enterprise resource planning (ERP) solution is one of the last components that many enterprises implement, oddly enough. The foundational processes and data necessary for accurate planning and scheduling often overwhelm manufacturers.
Think about all you do in terms of production planning and scheduling within your factory operations. You make hundreds of assessments about quantity, timing, sequence, equipment and resources each day on your shop floor.
Planning and scheduling are two distinct manufacturing phases that work hand-in-hand. Planning – ensuring that production materials match job requirements – is more long term. Scheduling – establishing the order of production and allowing enough time to produce by the given deadline – is usually near term. You must be an effective planner and scheduler to manage your shop floor successfully.
Many manufacturers still rely on manual workflows for planning and scheduling. Employees use whiteboards with magnets and post-it notes; others manage their schedules and plans in Excel, printing out datasheets whenever necessary.
These processes may get the job done, but it's worth asking if it's the most effective way to do so. Handwritten notes need to be deciphered, and printed-out paper schedules can't accommodate last-minute changes. The most significant risk posed by manual processes is the potential for inaccuracy, which impacts the entire business. These manual data tracking methods, scheduling and planning result in lower productivity and costly overtime.
Many manufacturing companies want to move away from inefficient, time-consuming processes. Essential scheduling tools integrated into an industry-specific ERP automatically schedule jobs while also allowing the scheduler to drag and drop jobs within the system; in addition to the parent job, any necessary components or sublevels also adjust simultaneously. Administrators can quickly review the data to ensure accuracy. This allows you to review and document data inputs that might be "tribal knowledge." You're able to improve communications and break down information silos because data is now being recorded in the ERP and can be shared with other departments.
An ERP that supports advanced planning and scheduling functionality can take your business to the next level. Scheduling algorithms allow managers to see how different jobs in various production stages are consuming resources. It allows for what-if scheduling, which helps companies respond fast to unexpected situations. An ERP provides you with the ability to update the current schedule with real-time information, giving you insight into the availability of materials and resources and calculating accurate delivery dates.
You must be flexible to adapt quickly and easily if orders change or new priority orders arise. An industry-specific ERP supports this kind of flexibility. It considers how your planning and scheduling demands can help you increase accuracy, lower your costs, minimize late jobs and increase profits.
It's also worth considering a solution that's easy for your employees to use. You want your workers to quickly view job orders and peg individual job tasks to related sales orders or other top-level demands.
Our industry-specific industrial manufacturing ERPs are smart solutions to control your business's demands if you're a make-to-order, make-to-stock or mixed-mode manufacturer that wants to automate your planning and scheduling processes. They present up-to-the-minute information. In turn, order entry, purchasing, manufacturing and shipping have real-time visibility over the shop floor schedules and can be adjusted accordingly. Let your ERP do all the hard work so that you can focus your attention and time on what's really important.
Aptean Industrial Manufacturing ERPs offer you an opportunity to move away from cumbersome, manual processes towards more advanced planning and scheduling. More efficient planning and scheduling increases productivity and optimizes resources, allowing you and your shop floor to accelerate performance.
If you'd like to talk more about how Aptean ERPs can support your planning and scheduling needs, reach out to our team of industrial manufacturing experts. We'd love to talk.
Also, don't miss my upcoming articles: The Post-COVID Manufacturing Revolution, Part 1: Your Working Structure and The Post-COVID Manufacturing Revolution, Part 2: Your Pace of Change.
Related Content
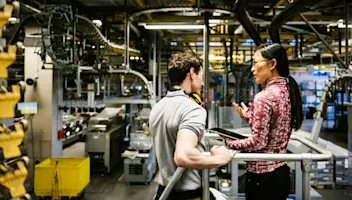
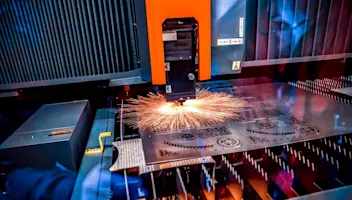
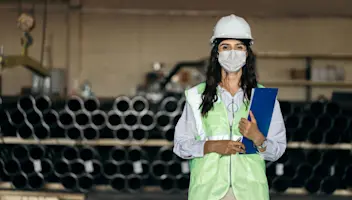
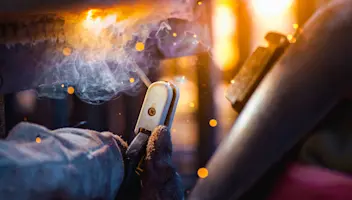
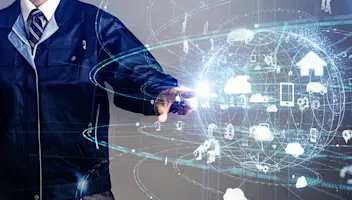
Start transforming your business today
If you’re ready to take your discrete and industrial manufacturing business to the next level, we’d love to help.
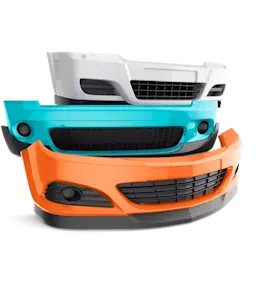