Four Critical Ways to Advance Your EAM Maintenance Strategy
Four Critical Ways to Advance Your EAM Maintenance Strategy
Four Critical Ways to Advance Your EAM Maintenance Strategy
30 Sep 2020
Aptean Staff Writer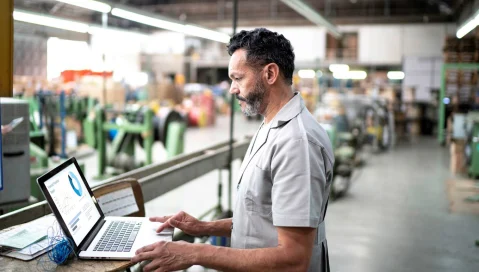
We wrote about preventative maintenance a couple of months ago and wanted to further explore how preventative maintenance positions your business for future success. By proactively maintaining your equipment, you’re monitoring your assets to identify and correct failures within the factory before they occur. And you can best prepare for the future by utilizing the data you collect today.
The objective of maintenance in the industrial manufacturing sector is to make equipment more reliable and predictable for production. Gaining visibility on how your machines are working, when they may have reached their limits, and when to budget for new equipment is critical to planning your maintenance strategy.
To create accurate forecasts about your equipment, you need to capture, review, identify, and evaluate the data within an enterprise asset management (EAM) solution. It enables you to make decisions today that directly impact future performance.
Getting to a place where you can predict breakdowns before they occur doesn’t happen overnight. It’s a steady progression of collecting the data right in front of you and studying it over time for insights that lead to more focused data collection and smarter decision-making.
There are four critical steps to developing a proactive approach for your maintenance program:
1. Data Capture
We want to emphasize it’s never too late to begin. If you’re not measuring your machines or collecting any data, that’s OK. Start now. Don’t worry about what to do with the data; just start gathering. Start simple and then build up from there. For example, schedule bearing temperature and/or pump pressure checks at regular intervals through your PM program. Record those measurements and stick to the schedule you create.
If you can employ more automated data collection approaches through IoT or an existing operations data network, then you begin to utilize those resources to capture more real-time data progressively. Real-time data capture is an advanced component to approach true predictive maintenance. It allows for more accurate, nearly-real-time predictions, and it directly monitors all of your asset conditions.
2. Review the Evidence
Next, take the data you just collected and study it. At this step, we’d analyze the data from those regular PM interval temperature and pressure checks and see if there are any patterns visible that indicate potential issues or align with issues encountered during operations.
The longer you do those regular PM checks, the longer your machine history is going to be. You’re going to notice patterns or inconsistencies more quickly and determine what the data means. If you have issues, you’re going to see what the data before those issues looked like and whether or not there was any indication that a problem might arise.
The more you capture data, the more compelling picture of each asset’s operational tendencies you can paint. From there, you can make inferences about the historical set of data you captured and compare it to the failure history that you’re storing in your EAM.
3. Identify Areas for Improvement
By reviewing the data you’ve captured for the various assets that you had measured, you’re able to produce an accurate prediction about potential future failures within your manufacturing plant. Based on your review of the evidence, you can make smart decisions—in real-time—to avoid downtime and machine failure. You can prioritize the equipment critical to your operations and more specific operating conditions that lead to failure. These early indications also allow you time to plan for downtime, rather than a failure interrupting your output capability.
4. Evaluate
Your data is only as good as your ability to use it. To use it, though, you need to be able to visualize and understand it. We’ve already discussed taking small steps to start measuring data and understanding it in terms of the bigger picture of your enterprise.
Along this journey, you have defined how you’re going to monitor and create alerts when there are issues with the equipment. By collecting data and identifying patterns in monitoring your machinery, you can use analysis tools to generate a hypothesis as to what is going to cause these problems. This type of analysis may highlight adjustments in actions and activities, which may include expanding the data you collect to gain more insight.
Over time, regular data capture and analysis builds a predictive maintenance strategy that delivers benefits to not just maintenance, but to the production operation as a whole. It’s not just about putting sensors on equipment and hoping you recover something; you need to intentionally configure and progressively study your factory in a way that makes sense to you. This strategic approach leads mostly to small, incremental changes in data capture, evaluation and problem-solving. Eventually, you have a robust, active maintenance program across the plant that can deliver better equipment reliability and fewer operational disruptions.
Creating the smart factory of tomorrow is more than just having a business that reacts to incoming data. You need to spot those signs and symptoms ahead of time. It’s about prevention to keep your machines running effectively and efficiently so that your enterprise can remain profitable.
Aptean EAMs provide full support for registering the unexpected issues with assets. The mobile applications allow users to record not only the details of the specific problem but also additional preventive actions.
Using real-time metrics and event data coming from instrumented assets, Aptean EAMs automate the delivery of information to maintenance managers to adjust preventive maintenance (PM) schedules, creating tickets to address issues or respond to failure warnings.
The application covers all areas, starting from work order generation, resource allocation and advanced planning features to easy tracking and analysis of financial information. Using the Analytics Module, the application extracts valuable information about how users are interacting with maintenance activities and provides insights on how to improve performance and efficiency continuously.
If you’d like to talk more about how to advance your EAM maintenance program with an Aptean EAM solution, reach out to our team of EAM experts. We’d love to talk.
Related Content
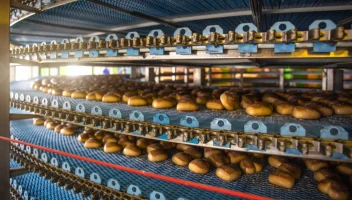
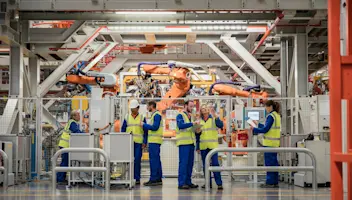
Ready to start transforming your business?
We’ve got the specialized EAM solutions you need to conquer your industry challenges.
