How Much Is Inefficient Delivery Route Planning Really Costing You?
How Much Is Inefficient Delivery Route Planning Really Costing You?
How Much Is Inefficient Delivery Route Planning Really Costing You?
2 Sep 2020
Aptean Staff Writer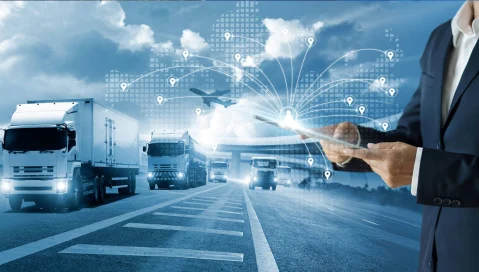
One of the challenges of managing a fleet of delivery vehicles is that you’re traditionally seen as a cost center and only a cost center. Your success or failure, at least in the eyes of the person in the corner office, will typically hinge on your ability to control or reduce costs.
There’s not much you can do about the price of gas, vehicles, maintenance or drivers’ wages — those are set by the market. But here’s one set of costs you really can drive down: those associated with inefficient delivery route planning.
Many companies continue to plan routes manually or using rudimentary tools, despite the existence of specialized routing software that automates the planning process and optimizes routes. We’ve found old-school route planning methods could mean your overall transportation operational costs are 10-30% higher than they should be. These avoidable costs spread beyond transportation, and the corner office is monitoring those costs, too.
Let’s look at where the money is leaking out:
Inefficiently planned routes use more miles and time than needed. Sophisticated delivery route planning software uses smart algorithms to assess dozens of factors and millions of route permutations to create the routes that take the least amount of time and travel the shortest distance. With manual planning methods, you’re never going to arrive at the most efficient plan. More miles mean more trucks, drivers and fuel than you really need. The American Transportation Research Institute (ATRI) calculates the average cost of a truck mile at $1.82. If you can reduce your total annual fleet miles by 10, 15, or even 20%, simple arithmetic will show you how much money you’ve been throwing down the drain just on wasted time and miles.
Replacing an unhappy driver costs thousands. The estimated average cost of hiring a new driver is $8,200, according to TheTruckersReport.com. that includes recruitment advertising, entry and exit administration, new driver orientation costs and other expenses. Ensuring route allocation is fair, achievable and unbiased is key to making drivers feel valued, and this is where the use of tailored route planning software can help. Generating accurate and feasible schedules that take into account each individual driver’s availability and needs makes for happier drivers who are more likely to stay.
You’re paying too much for route planners. When it takes hours to create what may only be an adequate route plan, you’re paying people to do the work that the right technology can do better — and in minutes. One large home improvement retailer was dispatching trucks from 80 stores and had part-time route planning resources in each of these sites. After the company automated and centralized planning, all route planning work across the network was done by two people without the assistance of any local planners.
Warehouse costs include unnecessary overtime. Businesses that need to send delivery trucks out by, say 8 a.m., have to work backwards to take into account the time it takes to plan delivery routes, then pick and pack orders for each load. When you are adding unnecessary hours to the process of planning, it can delay the pick-and-pack operations in the warehouse, often moving them into the expensive third shift that incurs overtime costs. Shortening planning time gives you the option of either moving pick-and-pack into a less expensive shift, or moving back your order cut-off time — increasingly a competitive benefit as demand for next-day delivery grows.
You’re handling more incoming customer service queries than you need to. Inefficiently planned delivery routes tend to produce spotty results when it comes to on-time delivery. That triggers more “where’s-my-stuff?” calls to customer service at a cost of $7–$13 per interaction. Businesses with good on-time delivery performance, as well as those using other route optimization technology capabilities — such as automated, proactive customer messages sent via email or SMS — can see customer service queries drop by 50% or more. This business saw customer satisfaction levels rise to close to 100% after implementing route planning and route execution software.
Cost-to-serve inaccuracies are expensive. One of the benefits of advanced delivery route planning software is that it provides huge amounts of data that allows you to assess the exact cost to serve each customer or to accurately predict the cost of serving a new customer (along with a host of other critical KPIs). New sales are typically a good thing, but when an overzealous salesperson promises deliveries twice a week to a remote location, the added fleet costs could make it impossible to turn a profit on this customer relationship. Customer demands are changing rapidly, and the general trend is towards tighter delivery time windows and other requirements that put pressure on your delivery operations. It’s absolutely essential to be able to break down the exact cost to serve each customer.
Operations that manually plan delivery routes are often dependent upon tribal knowledge, such as unique customer demands, driver preferences, and other nuances that aren’t well documented and may not even be contractually required. Routes can be biased towards driver or customer preferences, rather than based strictly on business requirements. If the manual planner is absent or separates from the company, the entire planning process is jeopardized until a new employee is trained or figures out a new manual process suitable for them. By deploying route planning software, all that tribal knowledge can be incorporated into the solution and evaluated to ensure that unnecessary constraints are not creating inefficiencies in the schedule, as well as simplifying cross training of other employees.
Efficient route plans equal cost savings, plain and simple
Delivery operations that are planned, executed and analyzed using anything less than sophisticated delivery route planning systems are substantially less efficient than they should be. That leads to many different kinds of avoidable costs, some of them hard to quantify or identify, many of them all too obvious once they become plain to see.
With the right type of delivery route planning technology, you can be sure you’re making the absolute best use of all your assets — not just drivers and vehicles, but planners, customer service representatives, warehouse workers and more.
Contact Aptean today to find out more about how you can trim 10-30% in avoidable costs from your overall transportation operations.
Related Content
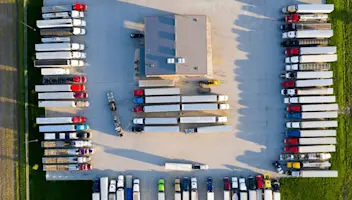
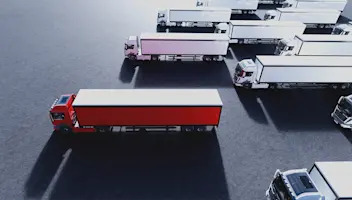
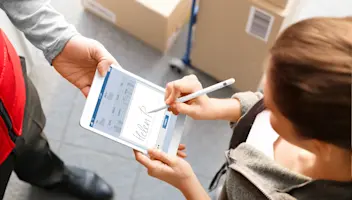


Ready to start transforming your business?
We've got the specialized TMS solutions you need to conquer your industry challenges.
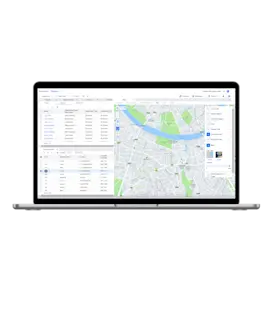