Featured in this post
Save Costs on Ingredients with Recipe Management
Save Costs on Ingredients with Recipe Management
3 Mar 2020
Aptean Staff Writer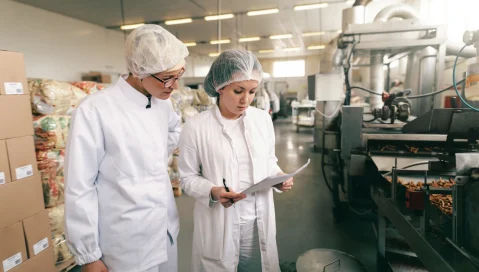
Every production process, no matter how simple or complex, is bound to have a number of necessary elements. It consists of one or several basic ingredients, certain equipment, tools and of course also people. Even in a fully automated process these essential components are always present.
Another important element of the production process is the ‘recipe’ for the production or the operation of the equipment or the entire process. A recipe determines how a production order is made. In a recipe you can define what different ingredients must be used, what must be produced, how it must be produced and what treatments and operations are required. You can compare it to a recipe for cooking, but much more advanced. Recipes are supported by instructions that guide the operator through the recipe step by step to arrive at a finished product.
Management of Recipes Through the MES Module
Having a recipe is one thing, but managing several and different recipes within your production process is a whole different story. Aptean can play a role in this. The Aptean MES Objective Edition software has ‘recipe management’ functionalities, which manage complex relationships and processes related to the production recipes of a company. It stores recipes, makes it possible to change recipes, generated data required for production registration, and even provides the option of starting tasks and processes.
Within recipe management clients can set the recipes entirely by themselves using the Aptean configurator, and the entire structure of the recipes can be created as well. But it is also possible to work from an ERP system using an interface. Aptean integrates with no less than 25+ ERP systems!
It is also possible to work with templates for recipes, as the production method is similar for some products. Instead of creating a new recipe over and over again, a template can be started that can be adjusted. One of our clients, La Lorraine, produces various types of bread, but has similar recipes. For instance, for each loaf you need dough and dough must be kneaded. All these similar steps can be laid down in a template. For a new loaf you can start from the template as it has been laid down, and it can be developed into a new recipe. This way, you need not configure treatments for each new loaf, saving much time. An additional benefit of the template is that adjustments can be carried out directly on the template, so future articles are given these adjustments simultaneously.
Don’t Let Your Ingredients Go to Waste
The picking of ingredients can also be defined in a recipe. This way, your ingredients are used optimally and the desired quality is guaranteed. A few examples:
First Expired First Out (FEFO)
This means that the products that expire first, are released first. Contrary to the first in, first out principle, this ensures that waste is avoided, and products are used optimally. This functionality is especially beneficial in the food and beverage industry. In other industries, the products that arrive first are usually processed first, and the products that are ready first are shipped first (first in, first out). In the food industry this is not so easy, as the expiry date of the products has to be taken into account.
This is true for the ingredients still to be processed and on the level of the end products that are shipped. At the first level, the ingredients that expire first will be processed first, to avoid waste. At the second level, the finished products with the shortest expiry date will be shipped first. After all, it is not self-evident that a product will expire first because it was made first. Sometimes, one product simply has a longer life than another. Aptean makes it possible to pick the stock based on expiry date; as a result, the products are used optimally and you will not be confronted with products that have expired.
Ingredients with A, B or C Quality
When you are working with ingredients of A, B or C quality to put a certain quality label on your finished products, it may be that you have run out of ingredients with e.g. C quality in your warehouse. If orders have to be shipped but you do no longer have the desired ingredients, you have a problem. In Aptean you can configure that you permit to use products of B quality when you are out of C quality, or to use A quality products when you are out of B quality.
You can also set that no product of a different quality may be used if you are out of A quality products, and production must be stopped until new A-quality products have been delivered. This way, the finished products can always meet the proper quality demands.
Manage Your Quantities
By recording and managing recipes in Aptean, you can ensure that there are as few surpluses possible. Suppose you only need three quarters of a pallet with a certain ingredient for your production order; with Aptean you can ensure that the remaining one quarter pallet will be put back into the warehouse, preventing the surplus ingredients that are brought to the line, e.g. an entire pallet instead of three quarters of a pallet, have to be thrown away. For the next order, the remaining one quarter of a pallet can be retrieved for use. Without the software the pallet with the remaining ingredients would have to be put somewhere in most cases, with a great risk of being forgotten.
Fewer Errors, More Consistency and Guaranteed Quality
First and foremost, with the use of recipe management there is much less chance of errors, as less configuration is required per order. After all, the recipes are already defined at order level. Furthermore, the option of version management also saves much time (e.g. templates, various versions of recipes, adjusting recipes). Finally, quality is guaranteed as well. In the instructions that go with the recipes, the amounts, specific treatments etc. of each separate product are exactly defined. The instructions may also come in the form of a photo or question, which the operator has to confirm. The operator must always carefully observe these, which again ensures fewer errors, but also a guaranteed quality for each finished product.
Production Optimisation with MES (Manufacturing Execution System)
Recipe management is just one component of the MES system. To take up the production challenges of today and increase efficiency, many future-oriented manufacturer have already opted for a MES (Manufacturing Execution System).
MES is an information system aimed at connecting, guarding and checking complex production processes and data flows, to improve production output and guarantee a successful implementation of all production activities. It can collect output data directly from the SCADA or PLC system and integrate them fully into the ERP system and the computer equipment, providing a full picture of the factory floor.
Aptean MES Objective Edition is a modern MES system developed to help manufacturers manage operators and machines optimally and analyse performance and quality in real time. The following things are made possible by the implementation of Aptean MES Objective Edition:
Efficient management of high complexity in production and logistics, and easy management of production with high variability and production of low volumes.
Elimination of separate data flows generated by ad hoc systems without joint support, or various systems not integrated with each other.
Ensuring transparency and traceability through easily retrievable documentation, making compliance issues a thing of the past.
Data integration with machines and systems to anticipate real-time information and updates about possible delays.
Standardising crucial processes to prevent problems with obsolete systems that are no longer maintained and with system managers absent.
Following and identifying underlying causes of quality problems in order to be able to solve these quickly, reducing costs of things not being implemented properly the first time.
Avoiding confusion by tagging production lines with unique line specifications.
By implementing the Aptean MES Objective Edition software, manufacturers can overcome the many production interruptions that hinder them, and ensure that they always supply the right product at the right moment at the right location.
Aptean is the expert in combined MES and WMS applications and services for the optimisation of production and logistics processes, with one solution being provided for a fully integrated manufacturing and warehouse management system. This gate-to-gate solution enables all Aptean clients to meet their priorities, varying from the control of the production and system transparency to the improvement of the operational efficiency and production of relevant data to improve the profitability of the company.
Related Content


Ready to start transforming your business?
We’ve got the specialized MES solution you need to conquer your industry challenges.
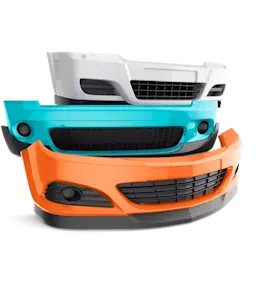