Featured in this post
Your Top Manufacturing Challenges and the Software Solutions That Can Solve Them
Your Top Manufacturing Challenges and the Software Solutions That Can Solve Them
26 Feb 2024
April Matthews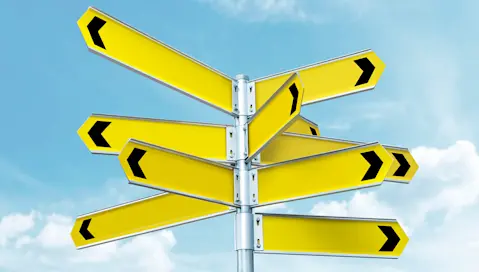
It may sound cliché, but that makes it no less true: the manufacturing industry is challenging. Whether you’re producing food items, car parts, dental equipment, clothing or another kind of product, you’re likely juggling a range of complex strategic problems, as well as day-to-day headaches and inefficiencies.
As you’ve probably heard from every industry body and vendor by now, the solution for many of your problems is advanced software and digital technology. It's likely a great relief to have an answer, but what does it actually mean? Which of your challenges are going to be solved and how?
In this first half of a two-part blog series, we’re going to answer those questions and more. Below we’ve listed six of the biggest manufacturing challenges—those everyday operational issues that impede efficiency and business growth—and explained how advanced manufacturing software can help your business address those pain points.
And in the upcoming installment, we’ll discuss how technology can help you tackle the problems caused by the latest trends shaping the manufacturing industry, including supply chain disruptions and talent shortages.
Challenge 1 - Lack of Visibility and Reliable Data
There’s no shortage of data in manufacturing businesses. Whether it’s coming from your finance department, warehouse, shop floor, suppliers or customers, information is plentiful, but can often use different measurement criteria, lack reliable accuracy or be unavailable at critical moments.
In addition, data may be stored in disparate systems with poor integration, collected in cumbersome spreadsheets, recorded with manual processes and paperwork or even just stored as tribal knowledge in the minds of your employees. But no matter the underlying issue, a lack of reliable, standardized data—accessible in real time—can cause a host of problems across your organization.
As a result, this is the first manufacturing challenge you should look to resolve, as doing so can help alleviate various other problems and form the foundation of your digital ecosystem.
The Solution
By implementing a fully integrated manufacturing software suite—usually with enterprise resource planning (ERP) system at the core—your business can gain end-to-end, real-time visibility into your operations. You can also be sure that the data is as accurate and standardized as possible so that everyone is working from the same “single source of truth” and alleviate the risk of losing critical knowledge with staff turnover. All of this breaks down silos, improving communication and collaboration between your teams, streamlining daily processes and helping you make smarter, data-driven decisions.
In addition, most advanced manufacturing software systems will provide metrics and reports to help improve data analysis in many key areas such as production scheduling, output, product lifecycle management (PLM), overall equipment efficiency (OEE) and delivery execution. So not only can you boost daily performance, but you can also perform better strategic planning based on your own data.
Challenge 2 - Poor Inventory Management
With today’s supply chain complexities and frequent disruptions, inventory control is fast becoming one of the toughest manufacturing industry challenges. Whether it’s raw materials or finished goods, you need real-time visibility into exactly what inventory you have and where it is. Without granularity and accuracy of inventory data, you can end up with surpluses or shortages, pauses in production and delays in order fulfillment.
Poor inventory management practices can not only directly impact your bottom line by delaying existing orders and damaging customer relationships, but also limit your ability to quickly capitalize on in-demand goods, new trends or seasonal shifts. And you can be sure that while you’re scrambling to find that missing inventory, your competition will be ready to fill the gap.
The Solution
By replacing manual methods, spreadsheets and basic systems with the purpose-built inventory management tools of manufacturing software, you can track all your materials and goods through each stage of the supply chain. Again, a robust ERP is the foundational platform of this digital ecosystem tech stack, giving you all that visibility and unlocking item categorization; stock level management; sales and purchase order tracking; shelf-life management; and automatic reordering.
So, what does this mean for your manufacturing business?
Quick access to digital data, integration with barcode scanners and automation of processes not only increases the accuracy of your inventory data, but also frees up your staff so they can focus on more critical tasks.
Alignment of procurement and production schedules helps you to reduce carrying costs, cut waste, increase sustainability and minimize losses.
Real-time insights and tracking provide end-to-end transparency and traceability—particularly important in highly regulated industries such as cosmetics and personal care, and for food businesses tackling shelf life and allergen management.
Challenge 3 - Inaccurate Forecasting and Planning
No matter what you sell, ensuring that your products are available and plentiful when your customers need them is the foundation for maintaining profitability and growing your business. But, as you know, aligning supply and demand is incredibly complex.
Without the tools to accurately and reliably forecast demand, your manufacturing operation will face a host of challenges. First and foremost, the resultant effects will be apparent in your production planning, with a lack of data increasing inefficiencies, slack time and waste. And with production scheduling that is not informed by solid demand forecasting, you’re at risk of leaving customers unsatisfied, missing sales opportunities and incurring higher costs.
All in all, poor demand forecasting leads to guesswork, reactive decision-making and significant operational inefficiencies—limiting your growth.
The Solution
With the right tools in your arsenal—such as ERP and business intelligence (BI) solutions—you can take the guesswork out of forecasting. By consolidating your data, analyzing historical sales figures and using current trend patterns, these systems can create reliably precise demand projections so that you can make smarter procurement and scheduling decisions. In this way not only do you help ensure you’re always ready to fulfill demand, but you can do so with optimized efficiency and minimized waste.
The best manufacturing software solutions combine these demand forecasting functionalities with production planning tools to help you further align supply and demand. Furthermore, production scheduling features help you optimize the use of all resources—including materials, personnel and equipment—and enable you to boost efficiency by better managing capacity, avoiding bottlenecks and facilitating smoother supply chain management.
Challenge 4 - Failure To Meet Schedule Attainment Goals
Even if your demand forecasting and production planning are optimized, your plan can come unraveled on the shop floor if you’re not reliably meeting your schedule attainment goals (in other words, not completing all the work planned within a specific production period). This could be for a number of reasons, from operator issues and equipment problems like the Six Big Losses to suboptimal facility layout and poor data visibility.
Whatever the cause, inefficiencies on your shop floor can lead to many challenges including underutilization of equipment, increased production costs, delayed orders and missed revenue opportunities. So, to avoid negatively impacting customer satisfaction, paying out for staff overtime and hampering your business growth, ensuring your production processes are optimized should be a top priority.
The Solution
To optimize plan attainment, you can implement programs such as lean manufacturing or Six Sigma to help maximize productivity. It’s also a good idea to conduct thorough operator training to streamline processes. And alongside those process-driven improvements, you’ll also want to invest in the right manufacturing software—namely OEE and enterprise asset maintenance (EAM) systems.
OEE software helps you calculate and improve your OEE score—actual productive time vs. available planned production time—by giving you insights into problem areas and improving processes. With an OEE system you’re able to minimize idling time, avoid short stops, reduce waste, maximize yield and increase productivity while optimizing the aforementioned plan attainment.
Meanwhile, an EAM system helps you manage the lifecycles of your equipment so you can get the most out of your resources. EAM enables you to track vital equipment data from procurement to disposal, schedule preventive maintenance, track spare parts inventory and streamline work order management. All of this helps you reduce labor and maintenance costs while increasing the performance and uptime of your assets—so there are fewer unexpected issues to harm your schedule attainment.
Challenge 5 - Inefficient Compliance Processes
Compliance is critical for manufacturers. Whether it’s facility safety rules, data protection laws, sustainability edicts, cleanliness standards or industry-specific restrictions like food traceability regulations and the MoCRA legislation in cosmetics, your business must adhere to many rules and guidelines. The consequences of failing in these duties can be both significant and wide-ranging, from reputational damage and revenue loss to hefty fines and even judicial ramifications.
As a result, every manufacturer is taking steps to be compliant every day. But are those compliance processes streamlined and efficient? Rarely. Because of the range of rules to follow and the importance of adhering to them, compliance procedures can become cumbersome and confusing quickly, burdening your staff with complex, manual or time-intensive tasks that take them away from profit-driving activities. That, in turn, will make it even harder to proactively adjust when regulations or standards evolve.
The Solution
With digital data management, strategic integrations, automatic alerts and automation of key tasks, manufacturing software systems enable you to optimize compliance processes from end to end. So not only can you reduce the time spent on related tasks, but also increase your confidence that you're always covered.
PLM software helps you prioritize regulatory compliance from the very beginning of the new product development (NPD) process, helping you better select compliant materials, design suitable products, choose suppliers, reformulate products to adhere to requirements and streamline documentation management. Next, a specialized manufacturing ERP system helps you meet your industry-specific regulatory requirements through every step of your supply chain with data visibility, streamlined processes and automations, ensuring you’ve got everything you need for compliance, audits and even recalls.
Complementary systems can solve additional compliance challenges like electronic data interchange (EDI) helping you master retailer compliance requirements, and payment processing software ensuring watertight payment card industry (PCI) compliance. And finally, transportation management tools can help you with distribution compliance by optimizing productivity with driver hours of service restrictions and forcing compliance with on-the-road procedures such as daily vehicle inspections and product temperature checks.
Challenge 6 - Customer Satisfaction Inconsistencies
When you provide consistently excellent products and services to your customers you not only stand to increase their loyalty—you also bolster your brand reputation and gather enthusiastic brand advocates along the way. All of this helps to drive profitability and growth.
On the other hand, string together a few negative experiences and you’ll be losing customers in an increasingly competitive market.
That means that one of the biggest manufacturing challenges you’re facing today is how to foster a customer-focused culture to deliver great experiences at every step while juggling all of the operational issues we’ve already mentioned. That’s a tall order.
The Solution
Thankfully, a variety of manufacturing systems offer features and tools to directly improve customer satisfaction. In addition, by optimizing many of your manufacturing processes and maximizing efficiency, you’re able to devote more time to taking care of your customers’ needs throughout the process.
When we boil it down, customer satisfaction relies on getting the right product of consistently satisfactory quality into the hands of your customer exactly when they want it. Here’s how manufacturing software ensures that.
Products that suit their needs - Whether you’re creating a new product or adjusting an existing one, PLM software boosts innovation and reduces time-to-market to ensure you’re capitalizing on new customer trends, technological advances and market changes. In addition, you can use BI tools to better analyze all your business data, helping you spot emerging trends and products that are waning in popularity.
With consistently satisfactory quality - Every product that comes off your production lines should meet your quality standards, that’s why the best ERP software provides auto-alerts, non-conformance management tools, consignment tracking, traceability reporting, and certification and validation tools.
Delivered when they want them - With ERP optimizing your production planning and OEE software reducing equipment downtime, you can be confident that you’ll have the necessary product available to deliver on-time, in-full (OTIF) with regularity. Moreover, route optimization software enables you to align your delivery schedules with customer requirements, all while reducing distribution costs.
Say Goodbye to Your Manufacturing Challenges To Unleash Success
As your organization grows, your manufacturing challenges will scale with you—hampering your pace of change, wasting vital resources and letting the competition get ahead. So now is the time to implement the right manufacturing software systems and iron out the wrinkles in your operation.
Why? Because not only will you streamline daily processes and remove operational headaches for your staff, but you’ll also pave the way for new ways of working that can accelerate your business growth.
For example, when your product designers are no longer chasing down data across multiple systems and departments, they can bring innovative new products to market faster—helping you capitalize on customer trends and boost revenue. Or, when your demand forecasting, production scheduling and inventory availability are all in alignment, you can confidently fulfill more orders, improving both customer satisfaction and resource utilization to safeguard your bottom line.
The key to solving these manufacturing industry challenges and unlocking big benefits for your business is choosing the right software, supported by a proven vendor. That’s where Aptean shines.
With decades of experience helping businesses like yours tackle the biggest challenges in manufacturing, we provide industry-specific software solutions backed by our expert in-house teams. So you can move confidently through your digital transformation journey with the support of a by-your-side partner that knows your industry struggles.
To help you evaluate which pieces of the puzzle your business needs, check out our rundown of the manufacturing software system landscape or dive into our industry-specific software for food and beverage, fashion and apparel, process and discrete manufacturing.
Also, watch out for the second part of this series as we discuss the current trends manufacturing software can help you tackle—from labor shortages to sustainability.
Related Content


Discover industry-tailored software built by the experts
With deep technical know-how and a commitment to innovation, we deliver tailored software to businesses like yours. Reach out today for your free, no-obligation consultation with an industry expert.
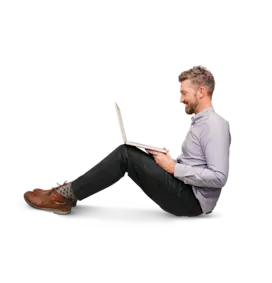