Quick links
What Is MES (Manufacturing Execution System)?
What Is MES (Manufacturing Execution System)?
22 Jun 2020
Aptean Staff WriterHeadline
- Manufacturing Execution Systems, Explained
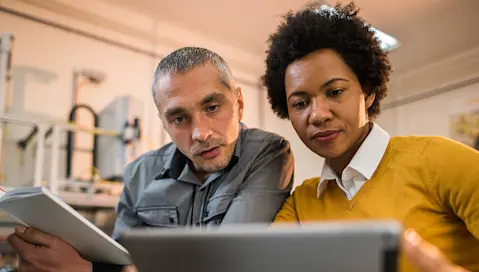
A Manufacturing Execution System (MES), is an information system which monitors and tracks the process of producing manufactured goods on the factory floor. The overall goal of manufacturing execution systems is to make certain that manufacturing operations are effectively executed to improve production output. That goal is achieved by tracking and gathering real-time and accurate data about a complete production lifecycle.
MES is the comprehensive system that controls all the activities occurring on the shop floor. It begins with all the various orders from customers, the MRP system, the master schedule, and other planning sources; and then builds the products in the most effective, low cost, expedient, and high- quality way possible. A comparative example occurs in the construction business where the construction team (MES) builds a tower from the architectural plans (inputs from MRP, Master schedule, etc.).
History of Manufacturing Execution Systems (MES)
Manufacturing execution systems have had quite the evolution. In the 1970s manufacturing organizations used software applications to automate their accounts. Over time, those applications were improved in order to provide the standard inventory management features. In the late 1970s/early 1980s came the MRP (Material Requirements Planning) systems, capable of material planning, material control and production definition.
AMR Research, who defined MES as a “dynamic information system that drives effective execution of manufacturing operations”, first coined the term in 1992. Early manufacturing execution system models were on-site applications, coded in a way that would represent the current manufacturing process of the organizations as-is.
Manufacturing execution systems have evolved from the simple data collection application that it was in the late 1980s into a more modern software in today’s age and time.
Core Functions of Manufacturing Execution Systems
In 1995, the ISA-95 standard was developed by the American National Standards Institute (ANSI) with the mission to provide abstract models and standard terminologies for the exchange of information between enterprise business systems and manufacturing operations systems in an enterprise.
The MES 11 model published in 1997 features the core functions of a manufacturing execution system. This model showed functions including scheduling and sequencing, maintenance and quality.
In its most current form, manufacturing execution systems core functions include:
Data collection and acquisition
Scheduling
Staff and resource management
Process management
Performance analysis
Document management
Benefits of a Manufacturing Execution System
A Manufacturing Execution System can deliver significant improvements in bottom line profitability, on time delivery, and better quality products. Additional key benefits of using this solution include:
Reduces manufacturing cycle time
Reduces or eliminates data entry time
Reduces work-in-process
Reduces or eliminates paperwork between shifts
Reduces lead times
Improves product quality
Eliminates lost paperwork
Empowers plant operations people
Improves the planning process
Improves customer service
Reduces setup costs, wait times
More reliable and precise sequence planning
How do MES and ERP Work Together?
Both MES and ERP (enterprise resource planning software) have the ability to work together. Since both software bring different capabilities to the forefront, using them together can help bring your business about more well-rounded results. Both software can be integrated, which can increase operational clarity and equip organizations with the ability to monitor and adjust performance against business plans. ERP knows why decisions need to be made, while MES know how to make those decisions. Both systems have their own purpose which can make them complimentary components.
Why Can’t I Just Build To The Order Schedules from ERP?
Today’s shop floor is a complex, continually varying environment. The scheduling needs to account for a level of variation that is typically beyond the scope of the planning systems- MRP, Master Scheduling and the like. MES automation considers and controls the highly critical details of a typical plant shop floor.
Causes of Variation on the Shop Floor
Machine breakdowns
Labor absenteeism
Changing setup times
Cleaning and maintenance times
Changing delivery dates
Quality problems
Alternative work plans
Alternative parts list
Availability of transport
Availability of quality resources
Changes to minimize process times, setups
It is therefore imperative to place the right tools and critical information in the hands of your front-line shop floor personnel, so they can produce your products in the most optimal manner possible. A good manufacturing execution system operates on a real time basis, allowing the schedulers to react to immediate variance on the shop floor. The Manufacturing Execution System also responds immediately to help make faster decisions on such things as costing over-runs, poor quality and late deliveries. It is virtually the heartbeat for all things happening on the shop floor.
Closed Loop Integration
Yet another critical characteristic of a Class A Manufacturing Execution System, is the ability to integrate with the systems surrounding it. Not only will this eliminate the mindless re-entry of mounds of data, it will also allow the adjustments necessary to bring the surrounding systems closer to reality. For example, critical information from the shop floor is needed to update other elements of the manufacturing ERP system such as Inventory, Costing, and Procurement. Setup times may be improving with new techniques used on the shop floor, and need to be fed to the ERP system for future use. This will provide better information when advising customers of projected delivery dates on new orders, or will provide improved costing information when making pricing decisions. The shop floor information provides the reality to make the adjustments necessary to continually update the other business systems.
Shop Floor Scheduling
A high-quality manufacturing execution system will also provide the best tools for controlling the scheduling needs directly on the shop floor. The shop is a complex environment with a high level of variety. Your schedulers are therefore critical in finding key opportunities to improve your production results.
MES Scheduling Methods
Finite Scheduling
Queue Compression
Visual Scheduler
Minimum Operation Priorities
Finite Slotting
Scheduling Methods
F = Forward
R = Repetitive
B = Backward
O = Overlap
M = Manual
P = Parallel
Full Functions of MES
A truly robust manufacturing execution system needs to include all the critical functions performed on the shop floor. A good Manufacturing Execution System cannot be totally responsive without the key shop floor pieces in place. The following functions should be offered at a minimum:
Resource Allocation and Status
Operation/Detail Scheduling
Dispatching Production Unit
Document Control
Data Collection
Labor Management
Quality Management
Process Management
Exception Management
Maintenance
Management
Product Tracking and Genealogy
Performance Analysis, including Work In Progress (WIP) overviews
What Modules Does a High Level MES Include?
Core Functions of MES Systems:
Planning System Interface
Visual Scheduler
eProduction/Dispatching
Shop Floor Control
Inventory Tracking and Management
Material Movement Management
Exception Management
Data Collection
Exception Management
Support Functions of MES
Maintenance Management
Time and Attendance
Payroll
Human Resources
Job Cost
Quality
Statistical Process Control
Performance Management
Document Management
Product Data Management
Genealogy / Product Traceability
Product Configurator
Bill of Material
Engineering Change Control
Supply Chain Management
Want to learn more? Consider these 6 questions when selecting a MES. Want to find out how a Aptean MES can help your business? Contact us today to chat with one of our experts or schedule a demo.
Related Content
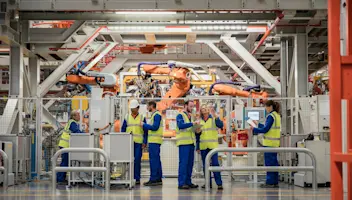

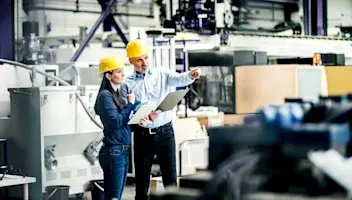

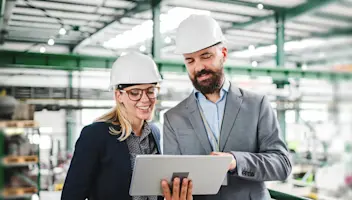
Ready to start transforming your business?
We’ve got the specialized MES solution you need to conquer your industry challenges.
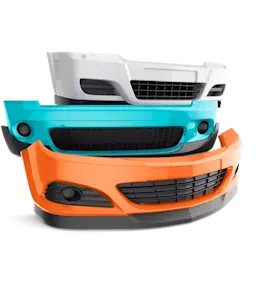