Aptean Food & Beverage ERP Case Study: Green Valley Pecan
Aptean Food & Beverage ERP Case Study: Green Valley Pecan
Aptean Food & Beverage ERP Case Study: Green Valley Pecan
15 Apr 2021
Headline
- Green Valley Pecan Tracks Millions of Pounds of Product With Aptean Food & Beverage ERP
Green Valley Pecan, based in Sahuarita, Arizona, was founded in 1946 by Keith Walden, who purchased a large area of farmland in the Santa Cruz Valley. Walden found initial success by becoming one of the country’s largest exporters of lettuce, but eventually determined that the Santa Cruz Valley was ideal for growing pecans. The company built its processing plant in 1975, and in 2000, expanded its operations and purchased two more swaths of land.
Today, Green Valley Pecan owns over 10,000 acres of pecan trees and produces tens of millions of pounds of in-shell pecans a year, making it one of the world’s largest growers and seventh-largest processor of pecans.
The Challenge
Prior to implementing Aptean Food & Beverage ERP, Green Valley Pecan was utilizing two separate systems to manage its operations. Although the old systems worked reasonably well together, the company’s team was stuck with the software’s most basic features resulting in a lack of real-time tracking and visibility. This created a number of challenges, including:
Manual production processes
Inefficient processes in the packaging department
Two day delays waiting for crucial processing data
The Green Valley Pecan team decided to look for a new enterprise resource planning (ERP) system that would provide them with the functionality needed to continue the success of the company.
“We were already using a Microsoft-based ERP, but we wanted to get more functionality from a new system—more detail, more real-time tracking of our processes—so we started looking for a new solution,” said Major Williams, Director of IT at Green Valley Pecan.
“What drew us initially to Aptean Food & Beverage ERP was that it had a lot of the base functionality we were searching for already built-in, so we didn’t have to go out and customize.”
The Solution
While searching for a new ERP solution, the team at Green Valley Pecan was referred to Aptean by a fellow process manufacturer in the Arizona area.
“We were looking for a vendor that understood food processing and process manufacturing,” said Williams. “Unlike discrete manufacturers who know exactly what is going into the production process and what is coming out, our processes are different. When we put a pecan into production, we don’t get the same result each time. It was important for us to work with a vendor that was familiar with our methods.”
Aptean Food & Beverage ERP is a purpose-built solution providing tailored features as standard to solve the unique challenges of food processors and manufacturers—from allergen management tools and bi-directional ingredient tracking to pricing features and expiration tracking.
“With these base features already in place, we knew we could build on it for our quality, traceability and production needs and be able to track our production processes in a detailed way,” Williams added.
The Implementation
While Williams and his team knew that an ERP implementation would be a huge undertaking, Aptean’s proven methodology for implementation success helped ensure the process was as smooth as possible. With collective decades of experience helping food and beverage businesses streamline their operations and accelerate growth, the in-house Aptean team was able to offer best practice advice and by-your-side support throughout the process.
“The consultants at Aptean were very knowledgeable about food processing,” commented Williams. “They came in and helped with the design of our system from the very beginning and challenged us about some of our processes. They introduced best practices, informed us about what other food manufacturers were doing, and we adapted our processes to work in those suggested changes.”
“Having access to critical information ahead of time, like how our cracking yield percentages are doing, allows us to make real-time decisions and adjustments to production as needed throughout the week.”
The Results
After going live in May 2017, the visibility into production data that Aptean’s food ERP delivers has been a game-changer for Green Valley Pecan. As a result, the company has been able to:
Increase the number of quality checks at each stage of production
Implement automated packaging processes
Track millions of pounds of inventory
Quality
Green Valley Pecan harvests hundreds of thousands of in-shell pecans a week. Each nut is put through a complex pasteurization, cracking, shelling and sorting process, which must be completed as efficiently as possible in order to keep up with production.
For Production Manager, Phillip Grajeda, the implementation of Aptean Food & Beverage ERP has helped tremendously when it comes to ensuring the quality of each of these processing steps and the final product.
“Our QC department is able to set up quality checks at each step of the process, from cracking all the way to packaging,” Grajeda said. “There’s a check in place after a pecan has been cracked, right before it’s sorted and then again at the end for final approval. Samples are taken along the way, too.”
Traceability
In terms of its traceability requirements, Green Valley Pecan relies on Aptean’s food ERP to help track its product through its vast warehouse.
“The system has really helped us with the overall traceability of our product,” said Grajeda. “We have a huge warehouse and if we want to find a certain product, even a certain pallet, and it’s being housed amongst millions of pounds of product, we’re able to easily find it by using license plates created by the system and tickets that the packaging operators generate.”
This traceability functionality also helps the Green Valley Pecan team fulfill custom orders for product blends.
“We sort our pecans into eight or nine different sizes, and sometimes customers ask for a custom blend that includes various-sized nuts,” said Grajeda. “The license plating of individual pallets helps us quickly locate the product to use in these blends, which is extremely helpful.”
Packaging
Both Williams and Grajeda agree that one of the biggest improvements they’ve seen at Green Valley Pecan since implementing Aptean Food & Beverage ERP is in the packaging department.
“Previously we were using production orders to track our packaging materials,” explains Grajeda. “There were lots of ledgers being manually updated and it was very labor intensive.”
Now, the process is automated, and as soon as the packaging operator generates a ticket, the associated packaging is consumed in the system.
“We were able to reduce the packaging consumption process down to almost a one-click function in the system,” he said. “What used to take someone two hours a day to do, now takes us about five to 10 minutes.”
“Every time we come across a process or issue that seems to be taking our users a little longer than we’d like it to, or we find something that has too many steps, we find a way to automate it, and that’s one of the things Aptean has helped us with. They’ve worked alongside us and have helped us improve the entire time.”
Ready to Swap Your Generic System for a Specialized Food Solution?
At Aptean we know the food industry inside-out. With that expert knowledge we’ve developed a tailored solution to help food and beverage processors and manufacturers gain end-to-end visibility, enhance efficiency, control quality and maximize profitability.
With features for food traceability, allergen management, catch weight tracking, supply chain management and more, Aptean Food & Beverage ERP is ready to accelerate the growth businesses across all food and beverage sectors.
What’s more, we offer a range of complementary solutions—including product lifecycle management and overall equipment effectiveness solutions—to supercharge your digital transformation and streamline your entire operation.
So, if you want to find out more, schedule a personalized demo or get pricing information contact our expert team today.
You can also read more food and beverage success stories.
Related Content
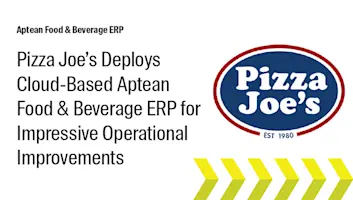
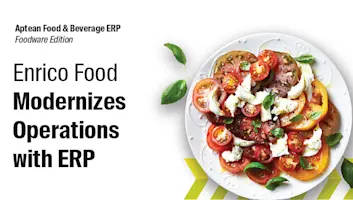
Start transforming your snack business today
If you’re ready to take your operation to the next level, we’d love to help.
