4 Ways Pandemic Pressures Have Changed Process Manufacturing
4 Ways Pandemic Pressures Have Changed Process Manufacturing
4 Ways Pandemic Pressures Have Changed Process Manufacturing
4 May 2021
Daniel Erickson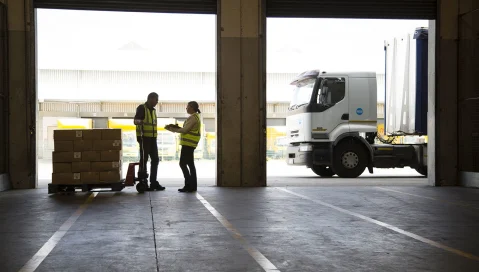
After a year like no other, the process manufacturing industry is ready to forge a stronger, more resilient future. But you need more than a calmer economy to build your organization back. You need to understand how the landscape has changed post-COVID and modify your approach to protect against future disruption.
In order to help process manufacturers recover and grow, we’ve identified four ways that pandemic pressures have changed our industry—and what changes are needed to future-proof your business model.
1. Rapid Innovation Is Now a Necessity
COVID-19 had a seismic impact on consumer behavior. And many of the industries that use process manufacturers were hard hit; the US prestige beauty market’s year-on-year dollar performance dropped by 25% in the first half of 2020, for example.
On the flip side, changing consciousnesses also led to an increase in demand for some process manufactured products. Discussions around whether vitamin D and zinc can protect people from coronavirus have increased supplement sales in some territories. In fact, the wellness industry as a whole has seen a surge; the nutraceuticals industry is forecast to grow at 9% CAGR between now and 2024.
Some process manufacturers were even part of the effort to pivot business models during the pandemic. One powerful example of this is hand sanitizer: from cosmetics brand Garb2ART to cannabis company Desert Hot Springs, businesses in a broad range of industries moved into a booming market to keep cash flow moving while promoting consumer hygiene.
Good, bad or new fortunes, the pandemic highlighted the need for manufacturing organizations to understand where demand is coming from, and to help your clients react to market demand. Rapid innovation is now a necessity.
Manufacturers that weathered the COVID-19 storm best were able to pivot production based on changing behaviors. And continuing to use this agile approach will enable you to make the most of any situation the future economy throws your way.
2. Supply Chain Alternatives Are No Longer Optional
On the subject of agility, it’s not just consumer demand that has shaped process manufacturing fortunes over the past year. While client relationships are critical to finding the opportunity, the onus is on manufacturers to get those products to market quickly.
Coronavirus showed manufacturers the impact of putting all your eggs in one supply basket (on an extreme scale). When COVID-19 hit China, the resulting business shutdown caused global supply chain shockwaves; long-term, trusted suppliers were no longer available.
Pandemic pressures have underlined the critical need for process manufacturers to have backup suppliers in place, to keep your production flowing even when things don’t go to plan. Quickly identifying potential supply problems and finding alternative resources builds long-term resilience into your business operation.
But it’s not just enough to expand your black book; you need to vet these suppliers, to know you can trust the quality of raw materials. And you need full traceability throughout your supply chain to ensure complete accountability.
The explosion of the hand sanitizer industry in 2020 is a powerful example of why supply chain transparency is pivotal. In addition to sourcing raw materials quickly, process manufacturers needed to ensure quality control and product labelling processes were watertight and compliant, to create products that consumers could trust.
Yet a survey conducted in the UK by Which? last year found that 18 widely available hand sanitizers didn’t contain the advertised 60% alcohol content needed to kill COVID-19 virus particles. While in the US, the FDA has been forced to create a do not use list, namechecking sanitizer brands that are either substandard or dangerous to consumers. These examples show the huge financial and reputational cost of prioritizing speed over quality.
3. Managing Lead Times Has Become a Package Deal
Supply chain resilience will go a long way to helping you future-proof your process manufacturing business, but it’s not just the actual products that need to be factored-in. The global pandemic also taught our industry a valuable lesson about packaging and logistics.
During the peak coronavirus crisis, one of the biggest hold-ups for manufacturing businesses wasn’t only the availability of raw ingredients; it was the packaging materials needed to complete customer orders. McKinsey highlighted the marked increase in packaging demand for essential industries like pharmaceuticals during 2020.
Anecdotally, many of the process manufacturing organizations Aptean works with saw packaging lead times increase from 2-3 weeks to 30+ weeks in some cases. Frustratingly, the products themselves were ready to go, but there was no way of getting them out.
Even manufacturers that could get products packaged and ready to ship weren’t completely out of the water. Regional shutdowns and border restrictions had a massive impact on shipping and logistics during the pandemic. As the International Finance Corporation reports, we saw scenarios where cargo was backlogged at ports, trucks were lined up at the side of the road and air freight was compromised by the sudden end to international consumer travel.
As with raw material supply, the availability of packaging and freedom of logistical movement is beyond manufacturers’ control. However, process manufacturing organizations can invest more in understanding what the reality of these constraints are, to factor them into lead times and keep customers up-to-date.
4. The Four Walls of the Factory Have Been Torn Down
Transforming the workplace model is not a new concept, but COVID-19 accelerated its trajectory beyond what most organizations had planned for. Process manufacturers were pushed into distributed working models that have permanently torn down the four walls of the traditional factory set-up.
In our recent blog post on connecting your business in a virtual world, we talked about the importance of enabling manufacturing professionals to work from any location. However, it’s also worth considering how the pandemic has reshaped operations inside the factory, on the production floor.
Social distancing mandates have restricted how many people can work together at any one time this past year, and how closely colleagues can collaborate while still protecting their health. This has prompted process manufacturers to look at how their people and machinery can work symbiotically to increase workforce efficiency.
In light of this, it’s not surprising that more than half of US companies are planning to increase automation investments due to COVID-19. The smarter you can work inside and outside the factory’s four walls, the better prepared you’ll be for the future.
Using ERP To Analyze, Integrate and Improve
Every process manufacturer’s priority list has been reshaped by the global pandemic, and yours will be different to your competitors.
But whatever is top of your list – from faster innovation, supply chain flexibility and increased traceability and transparency, to real-time demand management, cloud connectivity and further automation – all process manufacturing organizations have one thing in common: digital transformation is now a business imperative.
Process manufacturers have an opportunity to learn from the pandemic, and to make future-proofing improvements. And at the heart of these improvements lies industry-specific enterprise resource planning (ERP) technology, which allows you to analyze what is happening in your business and integrate operations, in order to make rapid, smart changes.
If ERP investment is a no-brainer post-COVID, there’s only one question that process manufacturers need to ask: what would’ve helped me perform better during the pandemic? This will give you your start point for change.
Our purpose-built process manufacturing ERP, Aptean Process Manufacturing ERP, is developed for the process manufacturing industry. Our fully integrated system streamlines workflow and provides scalable, flexible functionality. And we offer a cloud deployment option to support unlimited growth.
To future-proof your manufacturing business, talk to us about how Aptean’s cloud ERP technology can support your needs, post-pandemic.
Request a free demo of our process manufacturing software.
¿Todo listo para transformar tu negocio?
Tenemos las soluciones ERP especializadas que necesitas para superar los desafíos de tu sector.
