Applying Traceability Beyond Recalls
Applying Traceability Beyond Recalls
Applying Traceability Beyond Recalls
23 Nov 2016
Jack Payne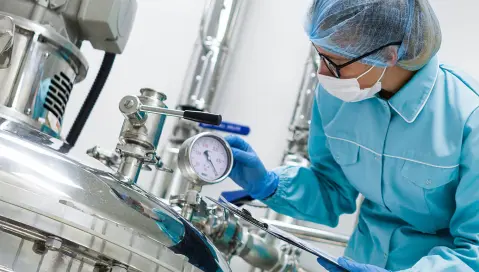
Human beings have been keeping on eye on their food supply since the dawn of time. Livestock has been identified in some form and monitored for centuries, particularly during outbreaks of disease. Ancient Romans had provisions to protect citizens from adulterated food. Early colonial America implemented inspection laws for the export of food to Europe. Only in the last 50 years or so have food companies more routinely relied on product identification codes and electronic systems. Regulations such as the 2001 Bioterrorism Act and the 2011 Food Safety Modernization Act have made traceability a critical factor for food companies to consider.
For most manufacturers, the number one reason to implement track and trace technology is to manage recalls. This capability can be also be used to improve other aspects of an organization, such as inventory management and quality assurance. This wider application can lead to improved efficiencies, reduced costs, and increased customer satisfaction.
Tracking the Source
Globalization has created gaps in safety in the food supply chain. The US imports approximately 19% of its food supply - 80% of seafood, 50% of fruits, and 20% of vegetables. The top three countries are Canada, Mexico, and China. Safety regulations vary by country, as do agricultural practices. Quality should be at the forefront of all supply chain initiatives for risk management and business continuity planning.
Solutions can include built-in controls to provide manufacturers with visibility into qualified suppliers and the ability to specify incoming inspection requirements. If a tolerance issue or contaminant is identified, track and trace technology can notify the manufacturer in real-time to begin addressing the problem and avert the deficient product from leaving the production floor. If the same product is returned multiple times, a root cause analysis of track and trace data might reveal a quality issue with a specific ingredient or supplier.
Tracking In House
Food manufacturers yield an average of 84% of raw material. Even a small increase in yield improves profitability. Managing growth and keeping costs under control are high priorities for any organization, and visibility into manufacturing operations is crucial.
Track and trace technology can be used to improve inventory management. Knowing when an ingredient arrived, and what its shelf life is, allows a manufacturer to optimize the use of its materials. For example, establishing protocols with a first-expired/first-out (FEFO) rotation ensures that stock is used in order, rather than being left to languish on the shelf. Lot controls can also dictate distribution order to that product with an approaching expiration date is shipped ahead of the next batch. Better use of inventory can lead to improved demand forecasting and planning, thus allowing for more strategic operational decisions.
Tracking the Distribution
Increased scrutiny and improved testing methods have led to more product recalls. In fact, contamination recalls have increased 167% from the first quarter of 2016 to the second. General Mills recalled 45 million pounds of flour after it was linked to an E. coli outbreak going back to December 2015. The flour was distributed to consumers, as well as other producers. Betty Crocker instituted a recall of its cake mixes and Krusteaz pulled its blueberry pancake mix, due to receipt of recalled flour. These secondary recalls are a direct result of traceability. By knowing the ingredients that went into the product, these manufacturers were able to take action quickly.
Regulatory bodies are not the only ones demanding that manufacturers be able to track a product forward and backward in production. Many retailers are requiring their suppliers conduct mock recalls to demonstrate their ability to track an ingredient’s path through the manufacturing process. Identification is considered the most important step in increasing the effectiveness of a recall. An industry survey found that 78% of companies can locate lot information within eight hours. An integrated ERP system with full backward and forward lot trace/recall capability has the potential to reduce that time to minutes. The sooner an issue is identified the sooner steps can be taken to resolve it.
Conclusion
According to the 2016 International Food Information Council (IFIC) Foundation Food & Health Survey, 66% of respondents were confident in the safety of the US food supply, down 12% from the previous year. Traceability can allow a manufacturer to greatly improve agility and decision-making, thus ensuring product safety, securing customer and consumer trust, and meeting industry and government regulatory requirements.
Contact Aptean today and discover the capabilities of our purpose-built food and beverage solution Aptean Food & Beverage ERP.
Food Insights
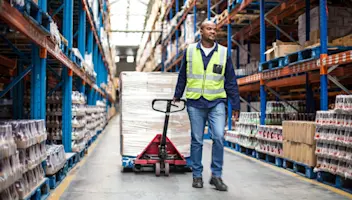
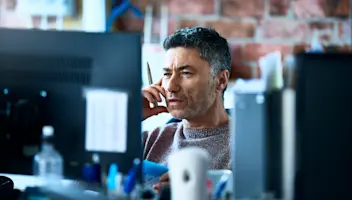
¿Todo listo para transformar tu negocio?
Tenemos las soluciones ERP especializadas que necesitas para superar los desafíos de tu sector.
