As Ecommerce Transforms Buyer Behavior, Your WMS Can Help You Manage the Perfect Return
As Ecommerce Transforms Buyer Behavior, Your WMS Can Help You Manage the Perfect Return
As Ecommerce Transforms Buyer Behavior, Your WMS Can Help You Manage the Perfect Return
6 Mar 2019
Aptean Staff Writer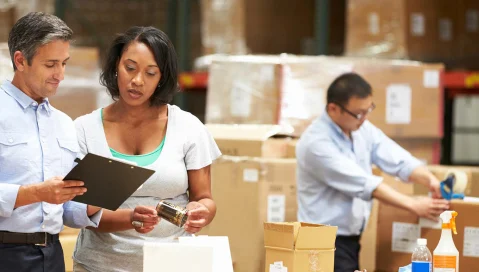
Last holiday season proved that consumer shopping behaviors have fundamentally transformed, possibly forever. Shoppers are now making purchase decisions based on a store’s returns policy. Eighty-six percent of consumers say that the returns process influences their buying decisions online.
Consumers were projected to return close to $100 million worth of gifts last holiday season. The rate of returns is surging across all products segments and is even growing in categories that traditionally have a lower rate of return like expensive products.
This enhanced focused on returns may look seamless to the customer, but it poses a real challenge for the supply chain industry. Forty-four percent of distribution center managers currently consider returned items to be a pain point in their operations. Attracting and retaining customers is now dependent on an organization’s ability to manage a highly efficient reverse logistics process.
The Most Efficient Way to Manage Returns
The challenge in managing an efficient returns process is limiting the amount of manual activity required for each return. Best-in-class organizations manage this process with just a single scan.
A single-scan receipt is when a returned product is received back into the warehouse through a single bar code scan. With that scan, a wealth of information about the item is available with the help of a warehouse management system, including customer details and order information. The scan can also prompt warehouse staff to capture reason or disposition codes to record the condition of the returned item.
There are two basic was ways to process a return in a warehouse – planned or unplanned:
With a planned return, the warehouse receives the item against a returns authorization and the system immediately initiates financial and inventory actions.
With an unplanned return, the item must be identified by the tracking ID, a return label ID, a license plate, the carton ID or an order ID.
Tracking the Financial Impact
The most important factor in an efficient returns process is managing the financial details of a return. Speed and accuracy are crucial to keeping customers happy by providing a quick refund and properly tracking the financial transaction.
The key is having tight integration between a WMS and ERP or financial system. This allows the organization to initiate the return in the WMS and immediately start processing the inventory and the financial components.
Enterprise-Wide Visibility
An inefficient returns process leads to wasted time, resources, space and money. One of the greatest benefits of a WMS system managing your returns process is the enterprise-wide visibility gained into your operations. The system allows you to view things occurring in a warehouse that you simply cannot detect otherwise, potentially saving a significant amount of time and money.
For example, if a pattern emerges where an item is returned consistently due to damage, there may be an underlying process issue. Using the data from the WMS you may detect an error in the packing process or the packaging type that was causing damage to the item in transit. Identifying the error as quickly as possible is essential to minimize the damages incurred.
This enhanced visibility is also useful for preventing fraud. Fraud often occurs with organizations that have generous return policies because the cost of processing the return is greater than the cost of simply shipping out a new product. The WMS can help detect a pattern of abuse by recording the customer’s history of returns, potentially raising a red flag and preventing payment.
Managing Complex Returns
A WMS is essential for accommodating more complex returns, like those involving serial and lot numbers. Serial and lot number validation is used to verify that the product returned is the actual product that was shipped.
For the healthcare industry, the returns process must include a review of details including expiration date, shelf life, and tolerance before the product can be processed back into the warehouse. In the case of pharmaceutical items, organizations may also require a verification of the lot number to maintain an accurate audit trail.
For consumer goods, serial number tracking can help in preventing scams from occurring. For example, a consumer may order a cell phone from your company but then try to return a different, broken cell phone in an attempt to get another new phone. Warehouse staff can stop this scam by validating that the serial number of the returned product was the same as the item shipped to the customer.
Building a Fast, Accurate Returns Process
Building the most efficient returns process is all about accuracy and speed. A WMS does this by minimizes the potential for human error. Not only does automation remove the need for manual entry, but it also provides the intelligence needed to identify the best course of action in every return situation, all with a single scan.
As consumer behavior continues to shift towards a higher volume of returns, improving your returns processes today is essential to keep pace. A robust WMS will give you the accuracy and speed necessary to meet expectations and maximize your capabilities. Read the WMS buyer’s guide to learn more.
Related Content

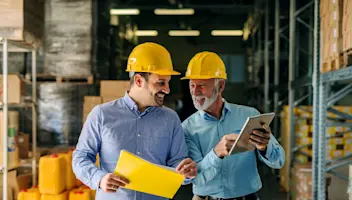
¿Todo listo para transformar tu negocio?
Tenemos las soluciones ERP especializadas que necesitas para superar los desafíos de tu sector.
