Optimizing Every Day: Why Your Manufacturing Strategy Must Be Always-On
Optimizing Every Day: Why Your Manufacturing Strategy Must Be Always-On
Optimizing Every Day: Why Your Manufacturing Strategy Must Be Always-On
12 Avr 2021
Jim Tuttle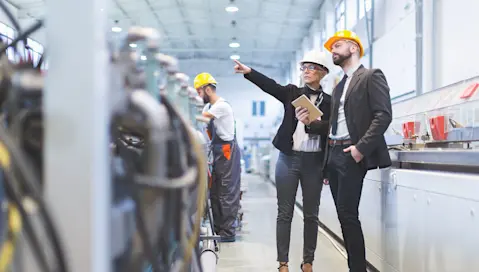
In a manufacturing organization, every person’s role matters, whether they realize it or not. A task that takes somebody a few minutes to perform can create process efficiencies that save the entire company several hours.
There’s a ripple effect to people doing their job well day-in, day-out. But manufacturers are often too focused on the biggest waves to see the massive impact that minor changes can make.
To continually maximize your performance, it’s important that everyone within your manufacturing business understands the value of their role. And looks for ways to improve and enhance everyday tasks.
In an ever evolving industry, your optimization strategy needs to be always-on. If you can help people to see how small changes add up, and give them the insights and technology to fine tune what they’re doing, you’ll soon see significant changes in your operational capabilities and overall profitability. Here are a few examples…
What Manufacturing Processes Do You Need to Optimize?
Achieving an always-on approach to manufacturing involves two core elements: understanding where you can make improvements to your operations and processes, and putting these improvements into action.
Machinery is a good example of how an always-on strategy can deliver significant benefits. Your organization creates schedules that allocate time for each asset to complete a particular job, but do you know how long it actually takes?
There are so many influences that can impact machine runtime. Delayed components; asset under performance; maintenance issues; lengthy tooling changeovers. They might only push the schedule back by a few minutes, but if it’s happening with job after job, day after day, your overall productivity starts to suffer.
How can you stop this from happening? It’s simple: your organization needs the data intelligence capabilities to analyze what’s happening on your shop floor, to see the gap between scheduling and reality. And this insight can be delivered through manufacturing ERP technology.
Improving Machine Runtime to Drive Smarter Planning
Real-time data insight, delivered through manufacturing ERP software, will empower your business to drive both immediate and ongoing success. In the short-term, it enables you to identify where performance or operational issues are slowing you down, so you can schedule-in maintenance work or make changes to your manufacturing processes, to optimize workflow.
But more importantly, in the long-term, data intelligence gives you an accurate picture of how long things really take. Using this information, you can become more strategic in your scheduling—using every minute of machine runtime to optimize productivity.
In addition to smarter planning, using manufacturing ERP to understand which jobs are most time consuming will help you to analyze profitability. Some of your current projects may take longer or be more complex than you realize, quietly eroding your bottom line.
Understanding which customers and projects are most profitable will enhance your business development strategy, as you can move your production schedule in the direction of tasks that play to your strengths, and support your growth goals.
Optimizing Design and Pre-Production
Machinery is just one example of where an always-on approach to optimization delivers big returns. Another area of your business that will benefit from ERP investment is design and pre-production.
Many discrete manufacturers produce a high mix of custom, made-to-order jobs, but the set-up required to get these jobs off the ground can be lengthy. In a disconnected approach, it takes several weeks to manage design, quotation, approval and ordering of materials.
The right manufacturing ERP technology will enable your business to integrate pre-production processes, in order to save time and people power. For example, using an ERP with CAD integrations means you can instantly convert concepts into component requirements once the design has been signed off.
Running your business holistically through one ERP platform allows you to turn concepts into production-ready designs within minutes, automatically generating a bill of materials. And you can use insights into how long similar jobs have taken to include custom projects at an appropriate point in the schedule, allowing sufficient time to get the job done.
Commit to Continuous Change
The two examples we’ve shared underline how empowering ERP technology can be to manufacturers. Ultimately, optimization is just better decision making, so your business needs software that will enable you to make the best decisions all day, every day.
Modern manufacturing is a complex infrastructure of continual micro-decisions and actions, all of which add up to massive time and profit saving efficiencies. By investing in the right manufacturing ERP software, your essential data and processes are continuously being logged, monitored and enhanced, so you’re driving perpetual improvement.
It’s this commitment to continuous, iterative change that will ensure your organization is always switched on. And the best part is that every improvement will make people’s jobs easier, quicker and more satisfying—building staff loyalty, and ensuring that everyone in your organization is contributing towards a profitably run business.
Ready to optimize every day? Aptean Industrial Manufacturing ERP is an industry-specific solution that enables manufacturers to understand your business in granular detail, to drive future growth.
Our manufacturing ERP software delivers relevant, real-time data through an easy-to-use dashboard, matching real-time inventory levels with scheduling for effective resource planning.
Get in touch to book your free Aptean ERP demo.
Related Content
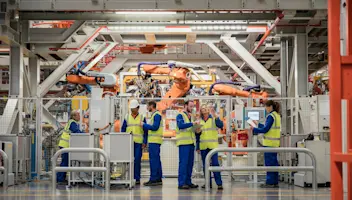

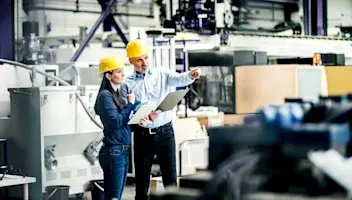

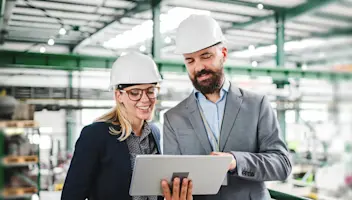
Commencez à transformer votre entreprise dès aujourd'hui
Prêt à faire passer votre entreprise à la vitesse supérieure ? Nous sommes là pour vous.
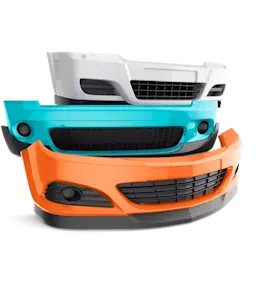