In diesem Beitrag vorgestellt
Garment Manufacturing: Tracing the Journey From Seed To Store
Garment Manufacturing: Tracing the Journey From Seed To Store
4 Juni 2024
Bethany Sanders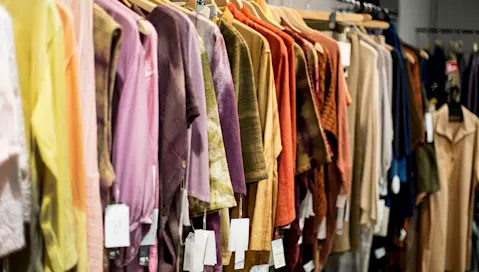
Have you ever wondered how your clothes are made? The fashion supply chain is a constantly moving process and involves the ongoing cooperation and coordination of lots of businesses and employees. It requires many steps and people, from farmers and factory workers to designers and store owners.
Take the simple cotton t-shirt—from its origins in the fields to its final destination in your closet, hundreds of people across thousands of miles have a hand in its production.
This blog will explore the journey of how a t-shirt transforms from a cotton seed to a finished garment in your wardrobe.
Five Steps of the Fashion Supply Chain
The supply chain for fashion brands and retailers can be broken down into five stages:
Design and Materials Management: Designing clothes based on trends, selecting the right materials and managing product lifecycles.
Procurement and Manufacturing: Procuring materials like textiles, thread, embellishments and closures, taking quality of materials and reliability of vendors into account here. These products will then move into manufacturing.
Warehouse and Fulfillment: Finished products are transported to warehouses where they are identified and placed in inventory.
Distribution: Orders are fulfilled and shipped to retailers.
Repairs and Returns: In the final stage, the conditions of products are identified, returns are authorized and refunds are issued.
While it may look simple written out like that, in truth, fashion businesses face a range of challenges at every stage—read our full blog for a more in-depth view of how to tame the complexities of the fashion supply chain.
With this clear picture of the fashion supply chain, let's break down the steps which lead to you getting the raw materials you need in garment manufacturing; far long before your product even hits the design stage or shop floor production, your materials have passed through numerous hands and machines along the way.
Step 1: Planting and Harvesting the Raw Materials
So, what are the main raw materials that go into making clothes? Going back to our cotton t-shirt example, the very beginning of the garment supply chain starts its journey as a tiny seed in a field. Let's dive into the nitty-gritty of how cotton is grown.
Most Popular Fabric in the World
Cotton is the most commonly used raw material for fabric in the world. Around 70% of our clothing contains cotton. Today, about 110 million bales of cotton are produced each year—that’s over 20 billion pairs of jeans.
But cotton is a fickle crop. It needs frost-free conditions, moderate rain and near-constant sunshine to survive. It’s also the perfect feast for pests and requires heavy pesticide use. For some farmers that’s where Bt cotton comes in.
Bt cotton is genetically engineered to produce a microbe that is deadly to certain cotton pests. Here are some pros and cons of Bt cotton use:
Increased cotton yields when it was first introduced
No adverse effects on soil, microflora or animal health
Effective at repelling pests; however, some pests have become resistant
Consumers may be reluctant to purchase from companies that use Bt cotton
On the other hand, rather than using genetic engineering, organic farmers use non-genetically modified crops and abstain from synthetic pesticides and fertilizers.
Planting and Cultivation
Cotton seeds are planted by huge mechanical planters that cover 10-24 trenches of soil at a time. These machines open the soil, drop in the seeds and cover it back up. Machines called ‘cultivators’ go back over the ground, pulling up any grass or weeds that might compete with the cotton. In about three months the cotton will have flowered like cotton candy and be ready for harvest.
Harvesting and Ginning
Most modern cotton operations use machines rather than hand-picking but, in many places, the backbreaking labor of hand-picking cotton is the only option. Still, there are a variety of machines that harvest cotton, including pickers and strippers.
Once the cotton has been picked and packed, it travels to the cotton gin—which has been around in its stone form since ancient times. Cotton gins clean, purify and remove the seeds from cotton fiber, extracting the raw materials needed to spin the world’s most popular textile.
Step 2: Weaving Cotton Into Cloth
For raw cotton fiber to become cotton as we know it, it is cleansed and purified in a carding machine then spun into yarn in a spinning frame.
Next up is the loom, which weaves the cotton yarn into sheets of cloth. The art of weaving goes back millennia—in ancient India, sheer cotton muslin was woven so fine that 73 yards of it weighed just one pound. These hand-powered looms required an incredible amount of labor to operate.
Thankfully, less labor-intensive modern processes mean weaving fits into the garment supply chain with much greater speed and efficiency. The finished sheets are then shipped to clothing manufacturing facilities to be bleached, dyed or otherwise finished.
Step 3: Shipping to Distributors and Cloth Purification
Now that the cotton has been expertly woven into cloth, it’s transported to a textile finishing facility. At this stage in the journey, the garment begins its transformation into the recognizable t-shirt shape that we all know and love. Here, the fabric undergoes a series of finishing techniques, each designed to enhance its quality and prepare it for its final form.
The process kicks off with the purification and cleaning of the cloth, including steps such as bleaching, desizing and singeing. Next, the fabric is colored, rinsed and dried. To combat fashion sustainability concerns in this stage, some producers have developed methods that eliminate the use of water altogether. At this point, cotton cloth can also be screen or block printed. To achieve desired texture and properties, a variety of mechanical and chemical techniques are then applied, giving the cloth its unique feel and characteristics.
Once finished to specifications, it’s ready to embark on the next step down the supply chain—the garment factory. This is where the magic happens. Here, it will be cut, sewn and turned into your new favorite t-shirt complete with hems, sleeves and pockets.
Step 4: Garment Production
While some companies have embraced vertical integration, spinning their cloth and crafting garments within the same facility, most clothiers operate across a global network of factories.
Factory workers cut the finished cloth into the required shapes and designs, passing these pieces along to the next set of workers: the sewers. These workers assemble the pieces, transforming them into an almost-finished state before they undergo a final round of finishing, cleaning and pressing—presenting your brand new seeded and sewn t-shirt.
But, garment factories can be challenging environments. Such conditions have drawn the attention of labor activists, sparking a global pushback against unsafe labor practices. This outcry has inspired some companies to completely overhaul their production processes and supply chains, using these reforms as a selling point for socially conscious consumers.
Step 5: Shipping Finished Products to the Warehouse
Your t-shirt is now running the home stretch to your closet. After leaving the garment factory, it will typically head to a distribution warehouse unless it's sent directly to a retail store. Given that most apparel manufacturers sell their products through various channels, let's follow this t-shirt through the busy world of distribution.
Brands, retailers and many other companies rely on massive distribution warehouses to efficiently organize and transport their products. Most of these warehouses are outfitted with cutting-edge radio frequency (RF) tracking technology, allowing management to track every single item in the warehouse in real time, providing precise data on the movements of each product. Applied globally, this technology enables companies to monitor their entire fashion supply chains, from raw textiles to finished garments.
When the shipment arrives at the distribution warehouse, a meticulous scanning process begins. Each item is logged and stowed, awaiting dispatch to either a brick-and-mortar or online retailer. Warehouse managers strategically place items based on their popularity. High-demand items are kept near exits for quick retrieval, while less popular items are stored further back. This careful planning significantly enhances the efficiency of a warehouse.
Step 6: Distribution From Warehouse to Storefront—or Customer
As soon as a store is ready for a shipment, they call the warehouse and your shirt embarks on the final leg of its journey where garments are loaded onto trucks and sent to postal services and retail stores.
In a store, employees receive the shipment and scan each garment as they unpack it, deciding where the garments should be displayed. Item placement can have a major influence on how quickly retail products sell. Popular items like t-shirts are typically placed near the front of the store at eye level to grab the attention of shoppers.
Of course when fulfilling your online orders, your fashion and apparel items are shipped directly from your warehouse to the consumer—skipping over the brick-and-mortar retailor—often referred to as direct-to-consumer (D2C) shipping. This increasingly popular model is efficient and flexible, even allowing a hybrid model for your retail partners to ship your orders for you; allowing you to shift your strategy and focus to the new way that consumers shop.
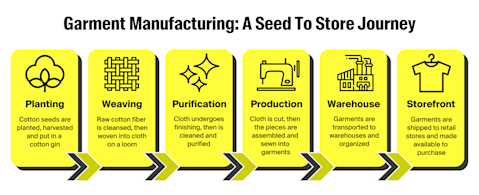
Simplify Supply Chain Management With Garment Manufacturing Software
There’s a lot that goes into our example of making a simple cotton t-shirt. On its embarkment from seed to storefront, your garment encounters more people and places than many of us ever do—your clothing has lived a full life before you even try it on. This intricate and global process ensures that the cotton cloth, starting from a simple seed to textile fiber, is transformed into the stylish and comfortable clothes we wear every day.
If you run an apparel business, you’re already familiar with how complex the fashion supply chain can be. But, sometimes it can be a struggle to stay on top of all the moving parts, especially if you don’t have the right apparel industry tools and technology to help you. If you find yourself constantly seeking greater insights and ways to optimize your operations, Aptean can help.
Our expert garment manufacturing enterprise resource planning (ERP) software is purpose-built to help apparel companies monitor and track every aspect of your fashion supply chain, from managing your products lifecycle to improving supplier relationships, managing your warehouse and controlling costs.
Our garment manufacturing software can help you use that data to streamline your processes, reduce inefficiencies and enhance overall productivity so that you will always have visibility, efficiency and control over that t-shirt, or any other apparel product you manufacture.
Contact us today or request a personalized demo for more information on Aptean Apparel ERP and our other apparel software solutions.
Sind Sie bereit, Ihr Unternehmen grundlegend zu verändern?
Wir bieten Ihnen die spezialisierten ERP-Lösungen, die Sie für die Herausforderungen Ihrer Branche benötigen.
