Leverage CMMS to Enhance Your Maintenance Management Strategy
Leverage CMMS to Enhance Your Maintenance Management Strategy
Leverage CMMS to Enhance Your Maintenance Management Strategy
22 Aug 2023
Aptean Staff Writer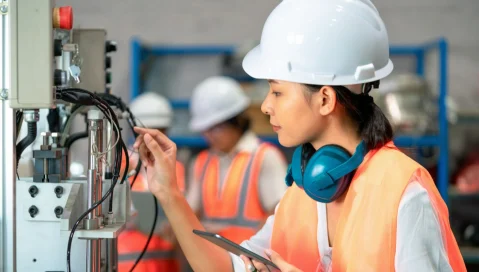
Capital equipment is at the heart of every asset-intensive industry. Today, businesses operating in the various sectors of the larger manufacturing industry—including food and beverage; computers and electronics; electrical equipment; fabricated metals; and transportation equipment—are increasingly turning to technology to improve their maintenance processes and keep machinery in tip-top shape.
That’s because businesses want to extend their physical assets' lifespan and improve both availability and reliability. This practice, which involves monitoring critical assets to make sure your operations can continue to run smoothly, is known as maintenance management strategy.
A recent survey discovered 88% of organizations outsource some or all of their maintenance operations—with the average facility utilizing a third-party contractor for roughly 23% of their maintenance tasks—stressing the importance of visibility across your business operations when planning your strategy for equipment maintenance.
This article discusses how deploying a computerized maintenance management system (CMMS) can help your organization elevate its maintenance management strategy to achieve optimal equipment performance by automating scheduled maintenance and tracking work orders as you manage your capital assets.
Why Is Prioritizing Maintenance Important?
Most maintenance teams are overwhelmed with a never-ending stream of work orders. As a result, they're primarily operating reactively and employing run-to-fail maintenance strategies—meaning they only engage in maintenance when capital equipment breaks down. That’s a problem, because those unplanned interruptions lead to extended production downtime and loss of potential profit.
Moreover, when critical equipment stops working as expected, you may also struggle with:
Wasted production resources
Overspending on emergency repairs
A lack of real-time visibility
Paper-based records dependence
Inaccurate performance metrics
Misinformed decisions
Poor equipment reliability
Extensive work order backlogs
Thankfully, there are maintenance management systems with proactive and preventive methodologies that can be employed in place of run-to-fail plans, and they’re proven to help increase your asset’s reliability and uptime.
Enter CMMS.
Indeed, machine breakdown is inevitable, but the main objective of prioritizing maintenance isn’t to prevent equipment failures entirely—it's to determine potential downtime and breakdowns over a certain period in production. With an asset management system—be it a CMMS or other software—you can make maintenance plans and strategic equipment decisions based on accurate data while tracking assets, improving equipment life expectancy and reviewing repair histories from one central database.
Understanding Value of CMMS
While CMMS software supports the maintenance of physical assets as it streamlines and automates work orders, repair schedule creation and other maintenance activities, the asset management system software can also generate data-driven reports on your equipment’s performance.
With those detailed analyses, you can then strategically plan for preventive maintenance work. Plus, the fully digital nature of the system eliminates tedious paperwork, allowing your team to focus on more important matters critical for business growth.
With CMMS, you can establish well-managed processes to improve asset performance, availability, reliability and lifespan—promoting higher productivity, cost savings and profitability.
Benefits of CMMS for Maintenance Management
Indeed, there is mission-critical importance with your approach to maintenance management and CMMS can help you with your maintenance management strategy. Here are some notable benefits of CMMS for your operations:
Streamlined Maintenance Schedules and Work Order Requests
CMMS can help you automate the creation of the aforementioned maintenance schedules for all your machinery, from small physical assets to massive equipment on the shop floor. Moreover, CMMS will allow you to strategically plan how to align technicians' shift schedules for preventive maintenance tasks. Deploying CMMS is a proactive approach to minimizing downtime and avoiding work order backlogs.
Accurate Asset Information
Full visibility of your entire operation gives you an edge in making data-driven decisions. CMMS lets you view all data on asset performance and overall health on one fully digital platform. With that information at your fingertips, you’re empowered to make smarter decisions that extend your equipment's lifespan with preventive maintenance measures, promoting potential maintenance cost savings.
Improved Asset Reliability and Uptime
With asset performance being the heartbeat and lifeblood of manufacturing companies, CMMS helps you maximize machine uptime while keeping precise maintenance records and equipment performance history. It also gives you the tools to deploy a preventive maintenance plan that improves asset reliability.
Centralized Database for Maintenance Technicians
CMMS’s centralized digital storage of manuals, photos, repair histories and reports can help technicians—on staff or third-party—retrieve the information they need to complete their tasks efficiently. CMMS software also categorizes work orders based on urgency and complexity. Furthermore, it allows the team to submit requests on a platform where managers can track them, and they can then be assigned to specific departments or technicians for completion.
of manufacturing organizations outsource some or all of their maintenance operations.
Real-World Applications of CMMS
How can CMMS impact your operations today? Here are examples of how CMMS helps businesses with maintenance management and strategic data-driven decisions:
Machine Downtime Reduction
Place yourself in the shoes of a plant manager. It's a usual workday, and your equipment is operating as expected. But suddenly, there's a commotion on the production line. One of your significant assets has shut down for no reason. You've called the head office to report the disruption, but they've told you to wait for the technician they've outsourced to do the repairs.
After a couple of hours, you finally receive a call from the contracted third-party repair service provider. Still, they tell you that no technician is available for dispatch and the earliest they can address the problem is around three days. What are you going to do with this emergency?
CMMS to Reduce Downtime
This is where a CMMS can help. By leveraging a CMMS solution for your operations, there’s a good chance that major assets won’t break down unexpectedly. If a breakdown does occur, CMMS helps streamline your repair process to ensure a quick fix and minimize disruption. Your plant can keep humming along and productivity remains high.
Implementing CMMS may help you in your preventive maintenance efforts by providing accurate, real-time data on your equipment performance. The system helps you make repairs and asset inspections a proactive matter, which helps to minimize downtime. Furthermore, technicians can see the asset’s repair history, manuals and spare parts availability in a central location for quick access.
Performance Analytics and Reporting
Manually measuring the performance of your assets requires many work hours for your employees. It also requires procedures that, no matter how meticulously they’re carried out, are still prone to human error.
Let’s take the case of a food and beverage company that manually records its equipment output at the end of every shift. The staff usually takes about half an hour every day to write pages of notes. When they don’t have time to write down their equipment's performance one day, they struggle to remember the stats the next day, and that leads to inaccurate data for reporting, not to mention the potentially misinformed decisions that might result from that.
CMMS for Analytics and Reporting
When this large food and beverage manufacturer deployed CMMS to their operation, it allowed them to adjust their strategies with data-driven decision-making. They’ve also saved hundreds of work hours by eliminating tedious paperwork required for each shift.
The guessing game is over. All employees are confident about the data in their reports. The CMMS empowers them to collect data from maintenance operations and production output while using automated reporting to track trends, performance history and other KPIs. Meanwhile, quicker decisions contribute to an increase in their productivity and accountability.
Streamline Maintenance Management Strategy
Indeed, prioritizing maintenance helps to prevent unexpected downtime and resultant revenue loss. Most companies that still manually record their equipment’s data will likely experience disruptions due to inaccurate information and unavoidable human error that led to suboptimal maintenance plans.
You may streamline and automate your maintenance management processes by deploying CMMS or a robust solution with more features and capabilities—for example, an enterprise asset management (EAM) system. Let's meet EAM now.
Connected to many aspects of your manufacturing operations—inventory, supply chain, purchasing and maintenance, repair and operations management—EAM can be your key to profitability as it provides data-driven insights for inventory managers that can help them manage asset strategies, purchase orders, inventory activities, disposal of old stock and availability of spare parts. With critical asset information easily accessible, managers can set up thresholds for maximum and minimum stock levels.
What’s more, preparing for an audit with EAM is simpler and more affordable. The solution facilitates scheduling inspection rounds and enables you to easily search for maintenance records and repair histories.
Selecting Aptean EAM as Your CMMS Solution
Aptean EAM has all the capabilities of a CMMS and offers even more features that may help you maximize your assets’ uptime. Our solution is a leading maintenance management system, purpose-built for the industries we serve. For more on the differences between CMMS and EAM, you can read our blog on the topic.
What’s more, with Aptean EAM you can choose to implement just the basic features of CMMS and grow into the more robust EAM features as your business scales and grows. Our cloud-based Aptean EAM system provides broader accessibility, enhanced cybersecurity, stronger data protection and optimal flexibility.
Jumpstart your maintenance management strategy with Aptean EAM now. Feel free to reach out to our team of experts so that we can answer your questions and together determine the right strategy for your business. You can also request a personalized demo with an Aptean expert today.
Related Articles
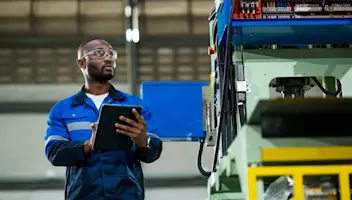
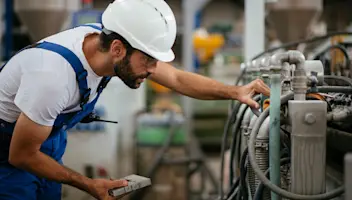
Sind Sie bereit, Ihr Unternehmen grundlegend zu verändern?
Wir haben die spezielle EAM-Software, die Sie benötigen, um Ihre Branchenherausforderungen zu meistern.
