How Molding Businesses Can Optimise Their Production Time for Large Batch Fulfilment
How Molding Businesses Can Optimise Their Production Time for Large Batch Fulfilment
How Molding Businesses Can Optimise Their Production Time for Large Batch Fulfilment
20 Oct 2022
Toni Guillen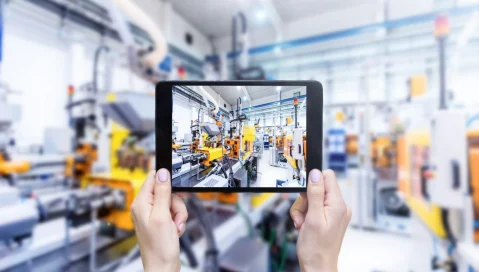
How can you streamline your operations?
In the molding industry, where bulk production of cheap items is the norm, every second counts and any stoppage in production can cost you a lot of money. Delays are expensive. So how can you minimise them?
The answer lies in using MES software for injection molding to streamline production processes.
Manufacturing Execution Systems (MES) track the production of goods from raw material to finished goods. MES systems are integrated into your ERP, SCADA, PLCs, machinery and smart sensors to help you gain visibility and control of your production processes.
Innovation in MES for molding companies is helping them to work harder and smarter, while saving money and giving them time to develop their business.
The Big Challenges for Molding Companies
You know how it is. The bulk goods you’re producing may be low-price, but the production is anything but cheap.
Expensive molds, the high cost of materials and the stringent demands of customers mean every second matters, and every scrap of efficiency you can squeeze out of your business counts.
As a manufacturer, you must be able to track your transactions to ensure money is not falling through the cracks. You also want to be able to trace the materials you’re using from gate to gate for maximum efficiency; keeping track of your consumption of raw materials is one of the biggest headaches for molding industry producers.
Your customers are also making demands on you—they want data on quality assurance, delivery times, traceability, liability and production hygiene.
The Modern Ways to Build More Efficiency into Your Business
For molding suppliers, one of the key trends now is incremental innovation.
As injection molding is a mature technology with a high-level of automation across factory floors, opportunities for improvement come in the form of greater efficiencies.
Higher speeds, lower changeover times, more flexibility, and lower energy and raw material consumption are where you can improve your business. Software that will help you do it.
Big data management is also a hot topic. The "fourth industrial revolution", aka Industry 4.0, is penetrating production within the molding industry.
As production processes become increasingly automated and more data is generated, using MES software—integrated with your machines and smart sensors to ensure product quality during the process—can help you increase quality and utilisation rates.
MES can also be used to generate useful reports and KPIs. You can track how much raw material you're using and where your processes are lacking optimal efficiency.
Are You Still Keeping Paper Records?
We still meet manufacturers in the molding industry who are using pen and paper, or basic software like Excel, to plan their production schedules. Their operations often involve multiple machines—sometimes dozens of machines—all which need different materials in different feeds, at different times, for optimum efficiency.
When something goes wrong with production, or a product must be recalled, these suppliers have to search through dozens of files, which can take many hours or even days.
Keeping manual records also means greater risk in terms of damage, as well as the environmental cost—plus it is much harder to spot patterns and get useful statistics from your data. If you can ditch the old-fashioned comfort of doing things on paper and embrace the security and ease-of-use of modern software, you will very quickly notice the benefits.
Molding companies that use MES reap the benefits in efficiency, in many ways, from maximised production schedules to near-instant report generation. In addition, they alleviate the aforementioned headache of tracking raw material consumption by monitoring that and machine performance all in real-time.
Using MES also leaves less room for human error, so you can take some of the responsibility off your team's shoulders, and free up their time for bigger jobs—such as designing your processes for further efficiencies.
How to Optimise and Streamline Your Production Time
As an example of the software you can use, Aptean MES Objective Edition and Aptean WMS Objective Edition use a WIP-IN tool to optimise production time between different machines for large batch order fulfilment.
Our WIP-IN tool allows you to configure your MES and WMS to deliver the correct raw materials to the right inputs of your machines for continuous production.
Depending on the situation, tasks will be released to the operators using our WMS system to bring these goods to the specified WIP-IN. This specification can be done per input. Each WIP-IN can have multiple properties—and be incredibly specific.
For example, you can configure locations so that a queue of pallets is waiting while one is being consumed. This queue can be programmed as FIFO (first in, first out), LIFO (last in, first out) or bulk (pick any you want), while the size of the queue can also be decided in advance. The possibilities are numerous.
It ensures continuous delivery of raw materials to your machines, and the system will notify you in time if resources are running out, so you can send more before production grinds to a halt.
How Our Customer Used WIP-IN for More Efficiency
A customer of ours, a producer of plastic boxes and crates, has 40 machines producing 24 hours a day, seven days a week. They use Aptean MES and Aptean WMS together to make sure there is always enough raw material on the WIP-IN to produce for at least four hours.
A one-tonne bag of raw material lasts for two-three hours, so the need for constant replenishment is high. The rate of consumption for each machine is different, so it's very difficult and time-consuming to manually calculate where materials are needed.
The WIP-IN tool calculates it for them. If a bag of material on the WIP-IN is starting to run low, the software automatically assigns a task so that the operators can fetch another bag to place on the WIP-IN, ensuring the machine doesn’t stop producing.
Our customers using WIP-IN within Aptean MES and Aptean WMS reported huge differences in the level of downtime, as well as a reduced number of errors. Being able to track raw material levels in real-time helped them make better use of their machines.
It's this kind of innovation from Aptean that is driving efficiency for molding companies.
Learn more about Aptean MES Objective Edition and Aptean WMS Objective Edition, and how we can help you streamline and optimise your production time. Contact us today or schedule a personalised demo.
Ready to start transforming your business?
We’ve got the specialised MES solution you need to conquer your industry challenges.
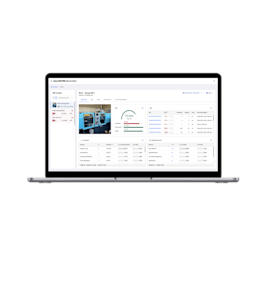