Going Beyond OEE: 5 Metrics Your Competitors Are Tracking
Going Beyond OEE: 5 Metrics Your Competitors Are Tracking
Going Beyond OEE: 5 Metrics Your Competitors Are Tracking
13 Feb 2020
Aptean Staff Writer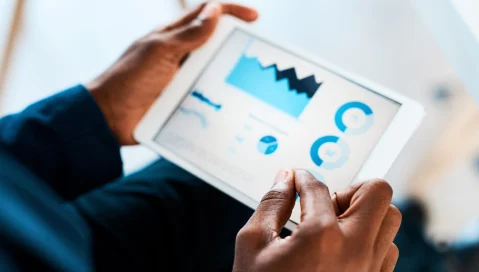
Don’t be fooled by the title of this piece. Overall equipment effectiveness (OEE) is extremely valuable to the success of your manufacturing business. Simply, OEE is a way to benchmark production and measure manufacturing productivity. A really good OEE score lies generally between 80 and 85; a perfect OEE score means you’re operating at 100%, that you’re manufacturing all parts perfectly as quickly as possible without any stop time.
Having a good OEE score is a given, though. Of course you should pay attention to that. We want to explore other metrics that you should be tracking to gain a leg up on your competitors. By monitoring bottleneck analysis, labor, material variances, non-productive time and quality, you’re ensuring that your factory is in fact running effectively and efficiently. Let’s take a closer look at these five metrics.
1. Bottleneck Analysis
Everyone knows that downtime in a factory is a bad thing. Downtime is time where product could be manufactured, where money could be made – but it isn’t. Downtime certainly hurts your OEE. A manufacturing execution system (MES) can pinpoint exactly when a piece of machinery goes down and the bottleneck effect it has on the rest of production.
A bottling line, for example, can run a half a mile long—between the depalletizing to the rinsing of bottles to the labeling to putting it back on a pallet, it can be difficult to determine where the inefficiencies are. As indicated in the image below, a robust MES solution, such as Factory MES, can pinpoint exactly where the bottleneck is occurring. If there’s an incident with the unloader, that would explain why the case packer is jammed. Not only does this make correcting the issue easier, but it keeps everybody in the loop and helps to avoid the cascading effect where everything thereafter is slowed down.
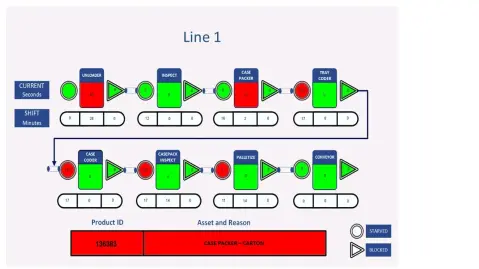
2. Labor Tracking
The factory floor is where you can either make or break your bank. If you have too many people on a line, you end up paying for labor you don’t need, and with too few people, you risk bottlenecking and running behind on a job. You need just the right amount. By having your employees scan onto or off of the line, either with a card or fingerprint scanner, to indicate they’ve joined (or left) a specific line task, provides you with a good labor metric. Labor tracking is tighter and cleaner simply because you know exactly how long each of the team members are on the line, how many members are on the line and how long it took to complete the job. This kind of tracking ensures you have as many people as you need and that everyone is doing the work they’re expected to do.
3. Material Variances
Let’s say you have a job where you’re making soup, and you need to measure out, among other ingredients, flour and milk. You need to somehow make sure that your recipes remain consistent between batches. So, if a recipe requires five pounds of flour, you need to add the exact amount without being over or under. Aptean Factory MES allows the operator in the mixing area to use a screen, which provides them with the necessary measurements, and connected to the screen is a scale on which they can make those precise measurements. The system records all the materials that are weighed from batch to batch to eliminate those material variances.
Not only does this process help to eliminate paper and consequently mitigate the risk of human error, there’s a quality aspect to it as well. It helps you track stock, ensuring that you won’t have any more material shortages; you’ll know exactly how much of each ingredient you’re using. This solution also enforces sequence, as there’s a setting that won’t allow the screen to progress until you’ve measured and indicated that you’ve added a certain ingredient. This is useful if you need to, say, add dry ingredients before liquid ones. There’s no way to cut corners when you’re tracking your data this precisely, which inevitably leads to fewer material variances and inconsistent batches of product.
4. Non-Productive Time
Non-productive time refers to the time that something isn’t being produced. OEE doesn’t track this time as it doesn’t actually begin until production starts. In order to ensure that you’re producing as much as possible, it would be valuable for you to track everything you’re doing during non-productive time. Likely, you’re changing over labor, prepping the machines, performing quality checks, sanitizing, and/or cleaning. Are you utilizing the data garnered from each of these tasks to drive efficiency? Are you wasting too much time changing over labor or prepping the machines? Tracking these non-productive metrics is essential to reducing this time that can now be used for production. Knowing how your productivity on non-productive tasks is just as important as knowing your productivity on production.
5. Quality Assurance
An MES solution that can use the data you draw from your quality checks to make adjustments within your ERP system is invaluable. Let’s say you’re in a factory, and you’re tasked with producing 1,000 8oz bottles of orange juice. If, on the line, the amount of juice being made is inconsistent—bottle number four overflows while bottle number thirty seven is only half-full—then clearly there’s a problem somewhere in the production process.
Employees on the line recognize the problem as they’re doing one of their periodic, manual quality checks, which are part of standard operating procedures and for regulatory compliance. After that check, they can input that data into the MES system, so that, if necessary, adjustments can quickly be made to the recipe, to the type of ingredient, to the process or container.
Your customers want every product produced to be a quality product. With all of the data from your quality checks in the system, your customer can ensure that they’re not being cheated.
Tracking these five metrics means you’re going above and beyond what your competitors are doing. Sure, it’s a bit more work, but the payoff is exponential. Factory MES can track all of these five things right out of the box. Our powerful MES solution can help you with your production activity by attending to all the details that have a bad habit of falling through the cracks.
If you’d like to talk more about Factory MES, reach to our team of MES experts today. We’d love to talk.
Get in touch today to speak to a software industry expert
To grow your business, you need a purpose-built ERP for process manufacturing. We're ready to help—reach out today for your free no-obligation consultation.
