Get Recall Ready With Chemical ERP Software
Get Recall Ready With Chemical ERP Software
Get Recall Ready With Chemical ERP Software
13 May 2021
Daniel Erickson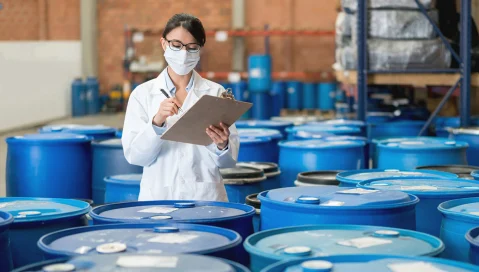
As a chemical manufacturer, there are many products in your warehouse that could have detrimental impacts on the environment—as well as volatile substances that could cause harm if handled improperly. As such, the industry is highly regulated to protect consumers from these scenarios.
But what if a product has a safety issue that is outside of your control and a recall is issued? How do you protect your company? Industry-specific chemical ERP software helps manufacturers in the preparation and mitigation of product recalls.
What Is a Recall and What Are Its Effects?
A recall is defined as the request to return a batch or entire run of product to the manufacturer that has been determined to have a safety issue. A variety of reasons can initiate product recalls. Everything from contamination, mislabeling, defective products and incorrect potency. Thousands of products are recalled each year. As you know, this can cause various issues for manufacturers, from financial and legal costs to reputational damage.
How a Chemical ERP Helps
An integrated chemical ERP software system serves as a tracking tool with end-to-end recall management functionality. This functionality incorporates industry regulations and strict forward and backward lot traceability. Detailed recordkeeping that includes purchase orders, bills of lading, batch tickets, labels, certificates of analysis (CofA’s) and shipping documents can be accessed quickly and efficiently to meet the legislated 24-hours to complete a recall.
The following features of chemical manufacturing software are particularly helpful with recall procedures:
Warehouse Management System (WMS) – As an extension of an ERP solution, WMS monitors and automates inventory transactions with barcode scanning to provide traceability and recording of inventory movements, lot numbers, storage locations and on-hand balances—maintaining detailed inventory information within the solution. In the case of a product recall, raw materials and ingredients, work-in-progress (WIP) and finished goods are quickly located within the inventory tracking system.
Mock Recalls – With a written recall plan and integrated chemical ERP software, mock recalls are handled easily. These are simulated exercises designed to improve your recall procedures by locating 100% of products within a designated time period, notifying necessary parties in the least amount of time and enabling employees to familiarize themselves with the recall procedures. When successful, all contaminated products will be identified and clients, vendors and government agencies will be notified. Each mock recall conducted should include an evaluation of the exercise to identify mistakes and deficiencies—enabling you to adjust manufacturing processes and the recall plan as needed.
Globally Harmonized System of Classification and Labeling of Chemicals (GHS)/Safety Data Sheet (SDS) Authoring – Integrated within chemical ERP software is authoring and labeling functionality to provide comprehensive and accurate information in the documentation for every shipment. These detailed records and labels aid in the tracking of recalled products once they are shipped out of a facility.
With consumers and regulators watchful eye over chemical manufacturers and their products, you need ERP software that enables efficiently handling of all your recall needs.
Be recall ready with our industry-specific process manufacturing ERP, Aptean Process Manufacturing ERP. Let us show you how, now.
Contact us for a demonstration.
Ready to start transforming your business?
We’ve got the specialized ERP solutions you need to conquer your industry challenges.
