Aptean Agility CMMS Case Study: Wavin
Aptean Agility CMMS Case Study: Wavin
Aptean Agility CMMS Case Study: Wavin
4 Nov 2024
Aptean Staff WriterBlog Post
- Revitalising our systems usage to further enhance our operations, maintenance, and estate management.
An AgilityCore CMMS has proven to be the best workflow and asset management system for Wavin
With a presence in more than 25 countries and over 5,500 employees, the energy-efficient company needed a CMMS system that would enable them to manage their assets with all planned and reactive work, schedule work to available engineers, manage tool room and form changes with production and report the performance of the team. AgilityCore has allowed Wavin to do just this as well as improve the production schedule and enhance proactive maintenance.
Wavin needed a CMMS system that would enable them to:
Manage their asset register with all planned & reactive work
Schedule work to available Engineers for minimal downtime
Manage toolroom and form changes with production
Report the performance of the Engineering team
The benefits of using an AgilityCore CMMS
An AgilityCore CMMS is used extensively, with 70 users operating over the 24/7 shift pattern. Through using mandatory fields for completion comments and fault codes Wavin are able to capture quality information that helps them identify recurring issues and causes of problems.
Paul Colley, Maintenance Planner is responsible for allocating planned and reactive work across the two teams within the Engineering department, Maintenance and Toolroom. Paul explains, “We use over 200 fault codes, which are prefiltered depending on the work type, so we really try to get to what’s causing breakdowns and problems. AgilityCore then shows us areas for improvement, better ways to spend our proactive time.”
The BARCO Plant Master Manufacturing Execution System (MES) is used by Wavin and displayed on screens to communicate the status of each production cell. The same colour coding is used within AgilityCore to connect any breakdown, repair or form change work being done by the Engineers. This enables the Production and Engineering Teams to have the same view and understanding of activity throughout the site.
Everything is in AgilityCore, so at the start of a shift we can see the priorities, colour coding enables anything urgent to be quickly identified. AgilityCore allows us all to give the priorities focus and helps the two departments work together collaboratively.
Wavin operate under the International Safety Rating Scheme (ISRS) to asses, improve and demonstrate the health of their business processes. AgilityCore CMMS is key to providing visibility of the register of approximately 1000 assets and ensuring it is well maintained with routine services and checks all set up as planned work. Health and Safety requirements, such as risk assessments and legionella checks are all scheduled in AgilityCore which is then used to store the result reports.
Over 70 contractors are also managed through AgilityCore CMMS; AgilityCore holds each contractors’ insurance and liability certificates and responses to the Wavin contractor questionnaire. Reminders are set so the System Administrator, Sam Shipley, can proactively ensure contractors documents don’t expire. “AgilityCore allows me to monitor everything and make sure everything is in the right place, all our information is reliable and visible.”
Labour utilisation is one of the Engineering Departments KPIs, Adi Clifford, Engineering Manager explains, “We accurately capture the exact time spent on each job through the log on/off functionality. We also know which assets are demanding too much reactive work, so we’re able to really identify what’s costing us as a business. By using AgilityCore we’ve been able to see where we need to improve, one result of this is that the Toolroom is now running between 80 – 85% proactive maintenance.”
Next steps
Adi expanded, “We recently moved to SSG Insight’s hosted solution for AgilityCore, we’ve seen significant performance and speed improvements in accessing the system. We’re looking into the Android application, as there are further savings in administration and time that could be made by giving everyone a mobile device.
“The inventory department is scheduled to have a new touchscreen carousel fitted which will be integrated with AgilityCore so we can accurately monitor parts movements, costs, usage rates and stock levels.”
AgilityCore is also used at the Chippenham site and was recently introduced to Wavin in Netherlands, further roll out to sites in Germany and Italy are in discussion.
Related Content

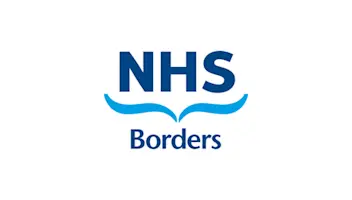
Ready to start transforming your business?
We’ve got the specialised EAM solutions you need to conquer your industry challenges.
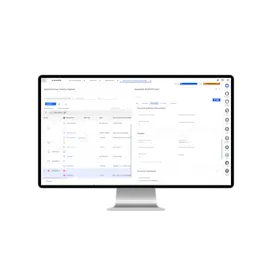