Advantages of Paperless Documentation
Advantages of Paperless Documentation
Advantages of Paperless Documentation
Jan 9, 2018
Aptean Staff Writer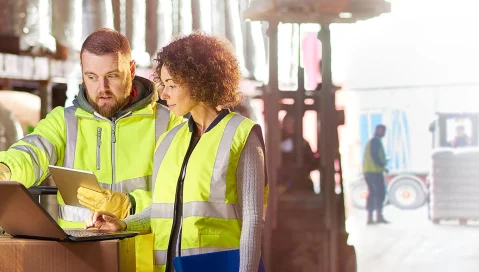
Many organizations strive to become paperless for a variety of reasons. The goals for Quality Manufacturing Services, a full service electronics manufacturing provider located in central Florida, were to increase efficiencies and accuracy on the shop floor, as well as for cost saving and a move toward sustainability.
Using a paper-based system to manage quality information leads to errors and scrap, which has a significant impact on quality and productivity. According to Gartner, workers spend about 60% of their time working with documents, and an average of 4 weeks is lost each year waiting on misfiled, mislabeled or lost documents. Moving to a paperless system not only saves time and effort, it also allows for easier, more secure access to important documents.
Working with paper is also expensive. According to the Environmental Protection Agency (EPA), the average office worker generates about two pounds of paper every day; with a case of paper averaging $40, the annual cost per employee is $80. Industry research estimates that searching for a misfiled document costs a company about $120, and re-creating every lost document costs $220 each. Equipment and maintenance, ink and toner and storage space add costs, too.
Going paperless is also beneficial to the environment. Americans use about 69 million tons of paper each year and recycle about 63% of it. Conservation experts estimate that each ton of recycled paper can save 17 trees and three cubic yards of landfill space. In addition, recycling saves 4,000 kilowatts of energy, 7,000 gallons of water and 380 gallons of oil, representing a 64% energy savings, a 58% water savings and 60 pounds less of air pollution.
QMS has accomplished a complete conversion from paper-based documentation to a 100% paperless model. The company made a significant investment in software, training and testing to accomplish this feat, but recognizes the many benefits that will come from this change in their corporate documentation workflow. Along with the cost savings, the organization will also benefit from the larger scale value of revision configuration control. While the costs associated with the paper process organization and revision control date stamping had not been objectively quantified, QMS recognizes the inherent dividends that will be gained from a paperless approach.
The engineering group at QMS creates manufacturing processes, coordinates specialized skills and constructs routers for each assembly. Prior to the paperless model, revision changes involved manufacturing engineers and supervisors to walk the entire manufacturing facility to locate paper processes, collect them, ensure that there were no uncontrolled copies, and remove them from the shop floor.
Now, if revision changes are received with notification through account managers, whoever is actively utilizing the current process revision is instantly identified. Manufacturing engineers can notify those individual active users of the impending change implementation. The obsolete PDF, along with all subsequent access, is removed from the server, internal ECO/ECN action is taken, and the revised process is uploaded at the latest revision.
Quality Manufacturing Services uses the Intuitive ERP solution to enable multiple shop floor interconnections and operations to run live through respective shop floor modules. Each shop floor workstation is equipped with either a tablet device on an articulating arm or a touchscreen PC, allowing each employee to register in and out of the system to access current active work orders. After work order entry, operators are one click away from a paper clip icon to retrieve a PDF manufacturing process. The ERP also identifies where each assembly is located along the manufacturing process, allowing WIP stream isolation until change implementation impact. With the paperless workflow, if processes are not at the most current revision, corresponding processes cannot even be accessed by the manufacturing floor.
Consistent to the core QMS philosophy of continuous improvement benefitting comprehensive quality and efficiency, the 100% paperless model also adds to the value QMS provides its customers. A complete and effective model was made possible through software technology advancements with supporting hardware, the Intuitive ERP framework from Aptean and the tireless efforts of the QMS IT administrator.
Request a callback from a manufacturing ERP expert
Discover the benefits of software designed specifically for the discrete manufacturing industry.
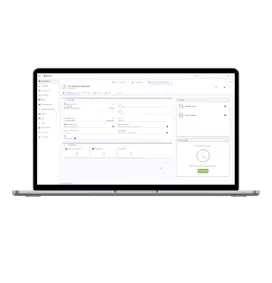