Building a Business Case for Process Manufacturing OEE
Building a Business Case for Process Manufacturing OEE
Building a Business Case for Process Manufacturing OEE
Sep 5, 2023
Aptean Staff Writer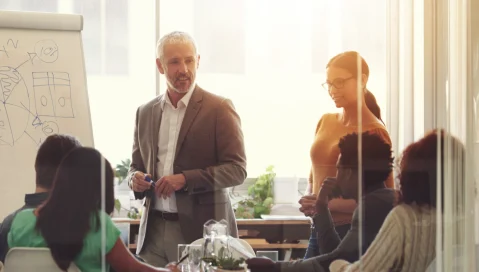
If your business is in the process manufacturing industry, you need to have full visibility of your operations at all times. After all, productivity and profitability must be tracked and analyzed for potential improvement in a market as competitive as yours.
Do you have visibility into the causes behind delays and increases in scrap or wastage? Do you have data-driven information to spot profitability constraints and preventable revenue losses?
Overall equipment effectiveness (OEE) is the most frequently used production metric to comprehend, assess and enhance manufacturing performance. A good OEE platform provides you with the real-time insight and reporting you need to boost equipment availability, performance and output quality by automatically collecting data to inform improvement plans.
This article discusses the reasons you need to have an OEE solution for your process manufacturing operations, helping you build a strong business case for your OEE software deployment.
How To Calculate Your OEE Score
To put it simply, an OEE score measures the effectiveness and efficiency of your manufacturing processes.
The OEE score is calculated by multiplying the variables of: availability, performance and quality. An OEE score of 100% is the perfect scenario in a production run.
Here's an example calculation:
OEE = Availability x Performance x Quality
Availability (50%) x Performance (68%) x Quality (98%)
OEE Score = 33%
Reflecting a poorly optimized process, this scoring metric would be a useful gauge by which to judge and re-evaluate longstanding methods of manufacturing to identify opportunities for better results and greater efficiency. In this example, asset availability and performance are quite low, indicating that the machines are continually taken offline; and during their optimal production time, they’re running slowly. Hence, it’s highly suggested to get more reliable equipment or schedule repairs to maximize your assets’ performance.
Availability
x Performance
x Quality
Foundations of a Solid OEE Approach
Solid OEE software can provide you with total visibility of your overall operational performance. It doesn't only target increasing your productivity; a well-integrated OEE solution can streamline every process in your production run.
Organizations in the process manufacturing industry often need to get to the root cause behind slow production runs and poor asset performance. By keeping close tabs on what's going well and what's not, your organization can foster better outcomes in the future.
Here are the notable benefits of tracking and improving your OEE:
1. Consistent Production Volume to Meet Market Demands
A good OEE platform can help inform enhancements of your manufacturing operations to increase efficiency and maximize production volume. Consistently delivering all orders on time and in full will improve your bottom line and promote a better customer experience.
2. Manufacturing Optimization to Reduce Wastage and Scrap
OEE software can help you identify issues on your production lines by providing complete real-time visibility of your operations. Hence, using such a solution can make a positive impact on continuous improvement and the reduction of waste. The more you can optimize a process and dig into the root causes of scrap, the more you can save on material costs and maximize quality yield.
3. Improved Shop Floor Accountability
Aside from your capital equipment, your workforce is essential to your manufacturing operations. OEE solutions can track performance individually or as a team. It's best to track how your staff fulfill their responsibilities by creating regular skill enhancement training and set them up for success on their career paths. It also encourages collaboration across departments with a single, unified dashboard that serves as the single source of truth for everyone.
Continuous Improvement With Current State Analysis and Lean Manufacturing
Manufacturers often look for more efficient ways to produce their products. Popular techniques for continuous improvement are current state analysis and lean manufacturing.
Current state analysis can help you to optimize procedures to promote cost savings and profitability. You may deploy solutions like OEE to help you perform this analysis and streamline production. You may also include lean manufacturing or the Define, Measure, Analyze, Improve and Control (DMAIC) approach for continuous improvement.
After you've measured your current state of efficiency, you can now move forward in selecting the right software to solidify your future state strategy. Furthermore, current state analysis can help prepare your company to implement additional solutions that support your OEE and overall manufacturing optimizations, including enterprise resource planning (ERP), enterprise asset management (EAM) and product lifecycle management (PLM) software.
Why Aptean Process Manufacturing OEE?
Now that you better understand the foundations of a solid OEE system, you may research various options available in the market. However, most OEE software that claims to have a "one-solution-fits-all" approach may fall short in meeting specific needs for your operations.
Aptean Process Manufacturing OEE uses real-time, shop-floor data for complete production and yield quality monitoring. It can immediately identify losses and OEE scores, allowing you to make data-driven business decisions in real-time.
We understand that you have unique manufacturing challenges, allowing you to tailor fit Aptean’s OEE platform to your business needs. It's been serving various manufacturing companies in food and beverage products, personal care and cosmetics, chemicals and nutraceuticals.
Aptean Process Manufacturing OEE has the following features and benefits:
Production equipment integration - automate data-gathering for accurate information through equipment integration.
Real-time OEE score calculation - obtain complete visibility of the equipment OEE score to help you adjust fast in certain situations.
Production performance, output and asset downtime tracking - measure production performance, output quality and track asset downtime throughout your manufacturing runs.
Advance analytics and dashboards - gain insight into production and quality with pre-built dashboards and PowerBI integration.
Quality management - streamline quality processes with a comprehensive set of tools.
Continuous improvement and collaboration - manage improvement initiatives with built-in frameworks and collaboration tools.
Beyond OEE - changeover, sanitation and clean-in-place (CIP) tracking and Total Effective Equipment Performance (TEEP)—track processes outside typical OEE measurements to maximize production output.
For example, imagine a bottling soda manufacturer that makes 10,000 bottles per batch of different flavors. After the first batch, they need to clean the equipment and change the parts of some assets. A traditional OEE solution wouldn't measure the cleaning time; but with Aptean OEE, you can measure OEE and TEEP across timeframes, including interruptions in your manufacturing operations.
Real Results From Deploying Aptean Process Manufacturing OEE
The success of Aptean customers serves as our inspiration and fulfillment.
After 12 months of Aptean OEE implementation, these companies saw OEE improvement from 6% to 23%. When you consider that a 1% increase in OEE can translate to tens of thousands or even hundreds of thousands in profits, depending on the size of your operations, that’s a tremendously positive effect.
Here are some actual results from customers deploying Aptean Process Manufacturing OEE:
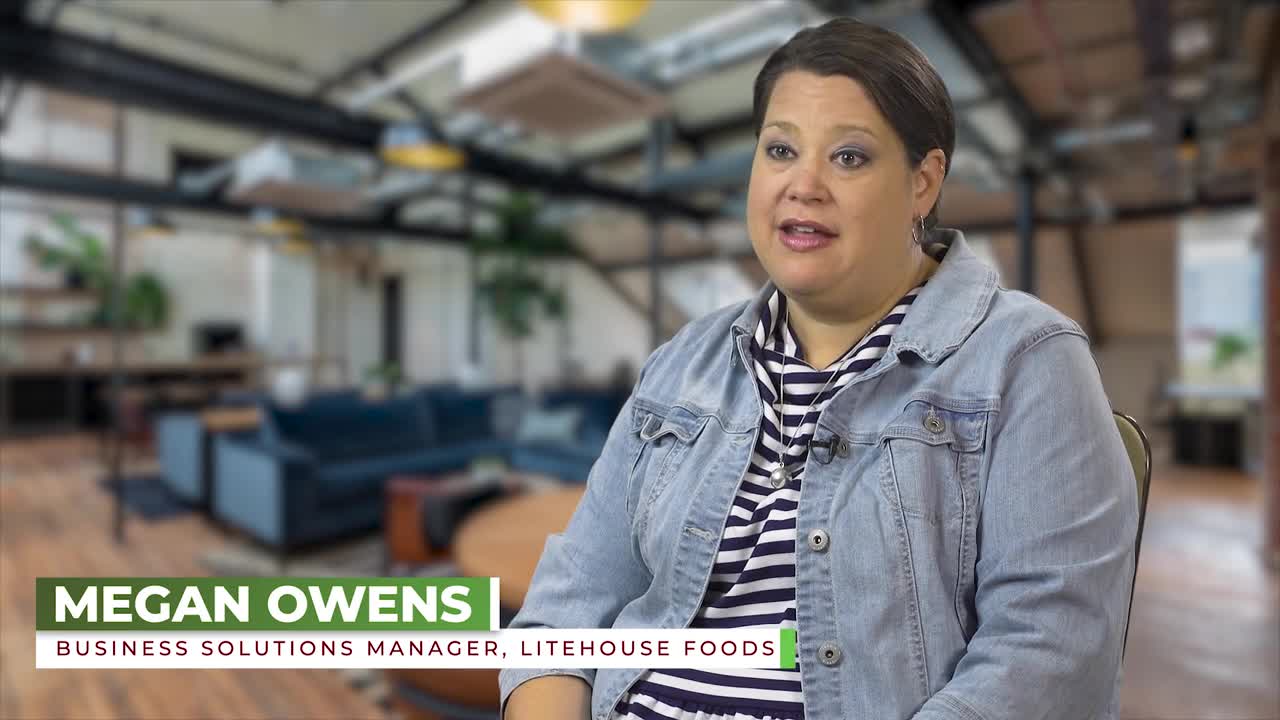
Litehouse Foods Experiences Unexpected Returns
Litehouse Foods is a leading manufacturer of refrigerated salad dressings, cheeses, dips, sauces, cider and freeze-dried herbs. The business’s efficiency was limited due to the piles of paperwork and the need for greater visibility in the actual performance of their manufacturing operations.
This $300 million company has leveraged the features of Aptean Process Manufacturing OEE since 2007. Following the rollout of the solution, the company has experienced an increase in uptime to 60-70%, a significant improvement from the previous level of 18-25%. Going forward, Litehouse is poised to engage in more continuous improvement while cultivating a positive production culture focused on quality.
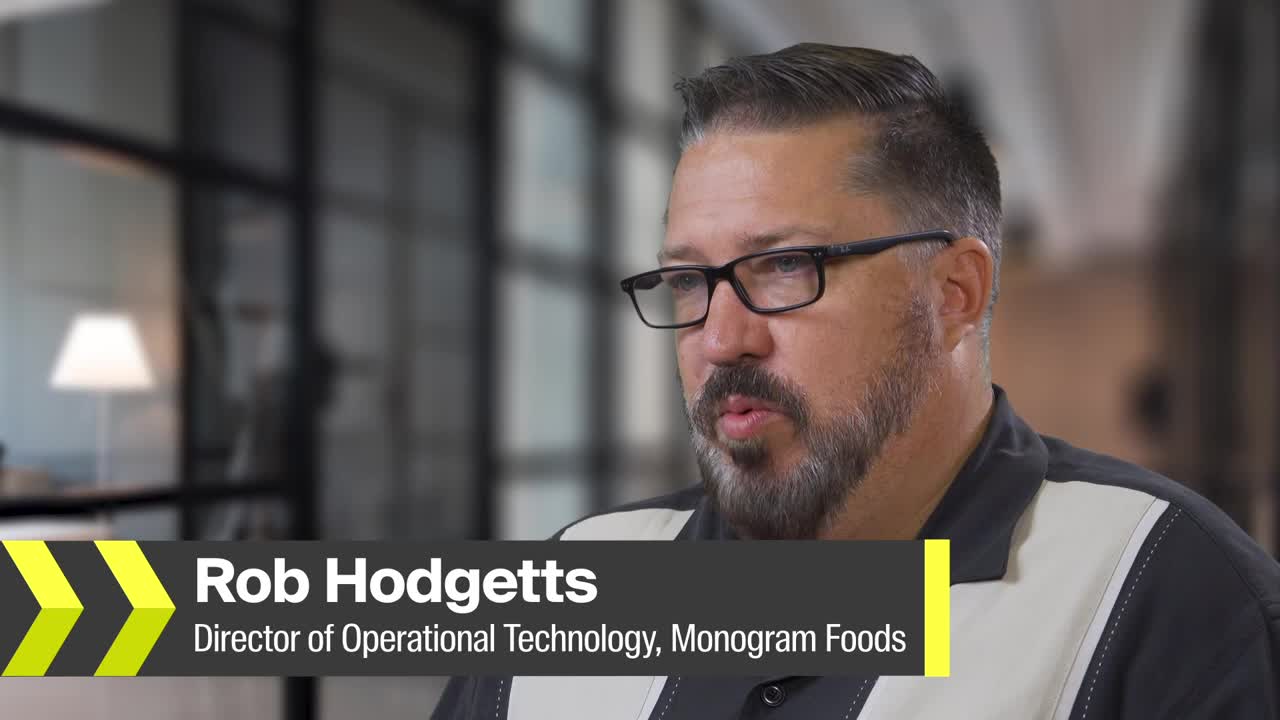
Aptean OEE Exceeded the Expectations of Monogram Foods
Monogram Foods, a company that manufactures food products for white label and convenience store customers, decided to deploy the Aptean Process Manufacturing OEE to minimize the need for paper-based recordkeeping, dig down into the causes of delays and address a lack of insights. The organization has seen a significant improvement in its OEE since deploying.
After go-live, the business’s OEE increased by 10 points while running high-volume lines. Now their team has complete visibility into their processes, including downtime, slow runs and quality control issues.
Delivering Results Across Multiple Industries
To further demonstrate the utility and potential impact of our system, here are the average OEE improvements realized by other Aptean Process Manufacturing OEE customers, broken down across numerous sub-verticals:
Get the Most Out of Your Aptean OEE With Complementary Solutions
Indeed, process manufacturing OEE can help you achieve production volume consistency and manufacturing efficiency while promoting shop floor accountability. Also, you can future-proof your manufacturing lines by integrating OEE to Aptean’s ERP solutions. This seamless integration of manufacturing and maintenance systems can promote efficient workflows and consistent production runs by maximizing your asset's performance data.
You can also complement Aptean OEE with our transportation management systems (TMS), EAM, PLM and other business platforms like Aptean Electronic Data Interchange (EDI), Aptean Pay and Aptean Business Intelligence to cover all your needs.
Discover how Aptean’s process manufacturing OEE can help improve your food and beverage and process manufacturing businesses. You can request a personalized demo to see how Aptean solutions work. Contact our team of experts today.
Ready to start transforming your business?
We’ve got the specialized OEE solutions you need to conquer your industry challenges.
