Organize Your Repair Shop with Planning Boards
Organize Your Repair Shop with Planning Boards
Organize Your Repair Shop with Planning Boards
Jun 16, 2020
Aptean Staff Writer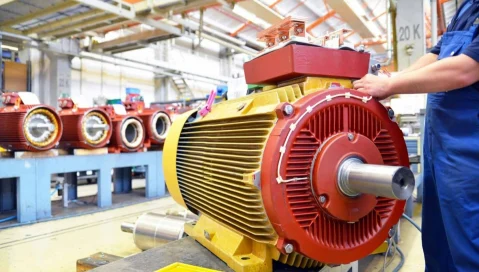
A common challenge for many repair shops is keeping organized within a dynamic environment in constant flux - juggling incoming jobs, consuming inventory and modifying priorities. Shop managers who handle the workflow of customer repairs on the fly or use manual methods expose themselves to missing important deadlines or losing track of jobs altogether due to the busy nature of the shop environment.
In this blog, we discuss Planning Boards, one of the features of motor repair shop software, that help shop managers organize repair jobs to ensure that a customer’s needs are met – improving efficiency and profitability.
Planning boards help document the details and standardize processes for each repair job to ensure customer satisfaction. As jobs are brought into the shop, some take priority and are designated as such – including rush jobs or repairs for special customers. With an ERP for service repair shops, the centralized database of the software maintains real-time parts inventory, accounts for work center availability and technician capabilities to schedule each job. The solution can help deploy just-in-time (JIT) inventory practices when ordering to remain cost-effective and ensure parts availability when needed in the repair process.
Two common Planning Boards that bring organization, visibility and profitability to repair shops, regardless of size:
1. Job Board Status
As the traditional method for tracking work in repair shops, a job board is a particular type of planning board that involves several phases or statuses including:
New – Job is set up and is placed in a holding area.
Active – Technicians begin the process and assess what repairs are needed.
Ready to Estimate – A quote is built for the customer based on their repair needs.
Waiting for Approval – Customer has been contacted and the shop is waiting for approval.
In Process – Repairs are in progress.
Waiting for Parts – Parts have been ordered and the job cannot be completed.
Job Complete – Repairs have been completed and the customer has been contacted.
Invoiced/Closed – Customer has been invoiced and has paid for the repair.
This board provides the ability to view all open jobs by status, dig into the specifics of job status to review job constraints, review daily movements and allow the shop manager to make on-the-fly schedule adjustments to accommodate priority jobs. With automation at each work center, the shop manager can be notified of delays and floor backlogs before ship dates are missed.
2. Job Purchases
This type of planning board details job purchases, focusing on the parts or inventory necessary to complete a repair job – a purchasing manager’s best friend! This level of monitoring centers on parts availability, parts constraints, lead times and ship dates. This oversight is an absolute necessity since if parts are unavailable, or delayed the repair job is at risk of not being started or completed on time.
In more advanced functionality of an ERP system, parts availability can be tied to a particular job phase, allowing a repair to be scheduled and started even if all of the necessary parts are not available in-house when repairs begin. If a part is not required until one of the later phases of a job, the schedule accounts for the lag time and allows a technician to get started on repairs without having to wait until all parts arrive.
As a repair shop manager and purchasing manager, access to Planning Boards within repair software provides the necessary information and visibility in one centralized location to ensure that repairs are moving along on time to meet customer promise dates. By regularly checking the status of jobs in each phase, it is easy to pinpoint problems and take care of them quickly before becoming an issue – adjusting schedules accordingly. Additionally, job purchase boards provide oversight of necessary parts to ensure availability for repairs.
Planning Boards organize repair shops to improve customer service and save time – providing necessary information before you ask for it. Aptean offers these invaluable tools and others for your for service repair shop. Contact us today for a demonstration of the features available in our motor repair shop software.
Discover industry-tailored software built by the experts
With deep technical know-how and a commitment to innovation, we deliver tailored software to businesses like yours. Reach out today for your free, no-obligation consultation with an industry expert.
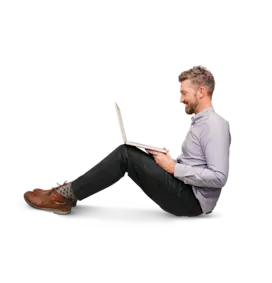