The Post-COVID Manufacturing Revolution, Part 1: Your Working Structure
The Post-COVID Manufacturing Revolution, Part 1: Your Working Structure
The Post-COVID Manufacturing Revolution, Part 1: Your Working Structure
Jan 12, 2021
Jim Tuttle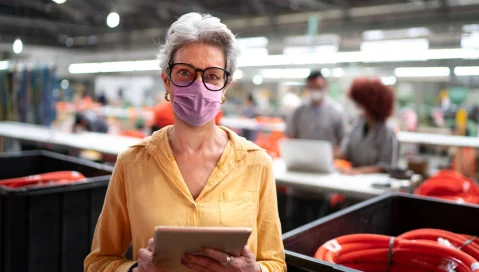
There are years of evolution, and there are years of revolution. 2020 absolutely falls into the second category.
COVID-19 has brought into question everything we know about industrial manufacturing. Supply chain strength; shop floor processes; people power; demand prediction. Pandemic pressures have touched the set-up of every business.
But while trading has been challenging, this isn't a time for self-pity. The manufacturing industry has been through rapid, uncomfortable change, and now it's time to take stock. What have we learned? How can we future-proof?
To thrive in 2021 and beyond, manufacturers need to take positive lessons forward. With this in mind, Aptean has looked at the most disruptive aspects of 2020 and how our sector can respond.
There are too many vital points to fit into one article, so this is the first of two parts: how to evolve your working structure for post-COVID manufacturing.
Remote Working Is Not a Quick Fix
2020 is the year we went home and stayed home. Overnight, manufacturers had to reformat their entire business to enable as many people as possible to work remotely.
Some were well prepared for this sudden change. Others less so. Either way, things aren't going to return to their old ways for a while – if ever. Recent McKinsey research revealed that 3-4 times more people now plan to work from home compared to pre-pandemic levels. And these people need to stay connected with colleagues on the shop floor.
Cloud strategies rocketed up the priority order in 2020, as manufacturers built virtual offices to keep their businesses running remotely. In many cases, cloud-based connections have been a matter of life or death. Aptean worked with multiple companies early-on in the pandemic, supporting their remote environments or moving customers to a hosted environment to continue producing critical front-line equipment for those worst affected by COVID-19.
Whether your business had a remote working structure in place before the pandemic, or you scrambled to put measures in place, you need to ask yourself an important question. Was your cloud strategy a quick fix – or will it work long-term?
Automation Is a Top Priority
COVID-19 hasn't just upset the status quo on where people work. It's fundamentally questioned how people work. Remote operations and social distancing have placed a premium on human capital, renewing the focus on automation.
To move forward, people and machinery need to collaborate to optimize output. In a virtual office, manufacturers can't rely on manual processes. Internal interactions, supplier updates and customer notifications must run seamlessly. Digital workflows are needed to deliver remote efficiencies, with automated notifications speeding up response times.
Significant change is already afoot. PwC's latest global CEO survey revealed that almost half (43%) of industrial manufacturing leaders plan to improve operations by modernizing their ERP system in 2021. Others have even more ambitious plans – 3 in 10 want to prioritize Artificial Intelligence (AI), while 37% are looking at predictive maintenance to minimize downtime.
Combining People, Power and Processes
Technology investment alone won't be enough, however. Two other key elements must be in place to meet the revolutionary challenges that COVID-19 has created.
The first is free data flow – which is reliant on complete system integration. However, this topic merits more in-depth discussion, so we're going to tackle it separately in part two.
The second key element is talent. We're already in the fourth industrial revolution, but COVID-19 has changed the game again. Manufacturers need to match people's power with process performance. Deloitte data reveals that upskilling will be a crucial focus for our industry in 2021. 3 in 10 senior executives want to develop new skill sets to ensure their teams are primed for post-pandemic production demands.
Manufacturers already know that blending human capability and technical ingenuity will future-proof your business. Automating technology should bring people, data and processes together for value-driven operations that play to everyone's strengths to deliver the most significant ROI.
Time To Make a Fresh Start
The world can change in the blink of an eye – this year has taught us that. And while quick fixes and interim ideas, delivered through gritted teeth, have got us through the eye of the storm, manufacturers can't rely on short-term solutions forever.
A new year is an opportune time to make a fresh start. For the manufacturing industry, this means looking at how your current operational structure is functioning and investing in the strategic and technical improvements you need to prepare for unpredictable action.
Your business may not have a future-proof working structure in place right now – that's OK. There are many other manufacturers in the same boat.
The important thing is to acknowledge where change is most needed and work with an industrial manufacturing expert who you can trust to build solid (yet adaptable) foundations for your business.
Enjoy this read? Look out for part two of our revolutionary change series on data-driven flexibility.
If you'd like to talk with us in the meantime, contact us here.
Related Content
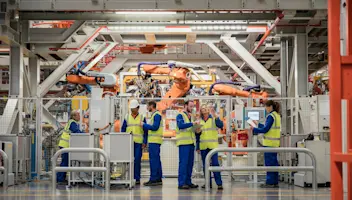

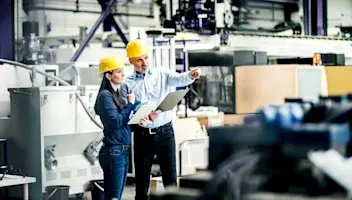

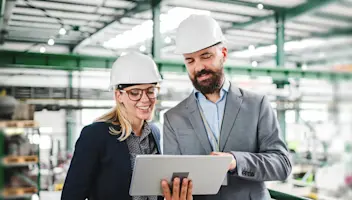
Start transforming your business today
If you’re ready to take your discrete and industrial manufacturing business to the next level, we’d love to help.
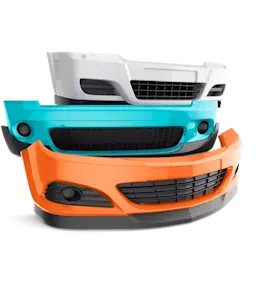