Preparing Your Factory to Take Advantage of Advanced Artificial Intelligence
Preparing Your Factory to Take Advantage of Advanced Artificial Intelligence
Preparing Your Factory to Take Advantage of Advanced Artificial Intelligence
Jun 13, 2018
Roy Thomas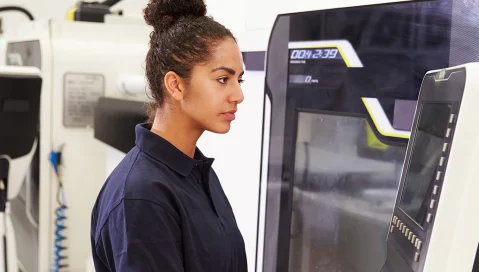
Ask any factory manager his or her thoughts on the most important tech advancement of the last two decades, and you’re likely to get a similar answer: data capture. Moving processes away from error-prone pencil-and-paper recordkeeping immediately increases shop floor visibility and efficiency. Managers no longer need to manually track machine and labor productivity; they can interpret the information and adjust processes based on their findings.
While basic data capture had a major impact on factory processes when it was introduced, it still suffered from a significant flaw: it couldn’t keep up with the speed at which managers must interpret, absorb, and then make decisions. If an important asset is days away from malfunctioning, that information must be readily available to the manager, rather than buried in data. Industry 4.0, driven by machine learning and artificial intelligence (AI), has made strides in minimizing this delay in decision-making.
To demonstrate the impact of Industry 4.0 on shop floor processes, think of AI in the factory as a chess match. You’re the player, inefficiencies are your opponent, and productivity is checkmate. With traditional data capture software, you’re only empowered to think about your next move. You have information about the factory floor’s current status and nothing more.
Today’s machine learning has already enabled factory managers to think one move ahead. Tomorrow’s developments, and ultimately the endgame for AI in the factory, could help us think two or even three moves ahead.
Strategies for Checkmate: Aiming for Maximum Productivity
Advanced AI is no longer science fiction. Although it may not be ready to solve all of your company’s challenges, innovators get closer every day. That’s why it’s critical to consider how you might prepare your factory for rapidly evolving technology. But if you’re still relying on manual data tracking to manage your factory, the thought of switching to automated processes can be daunting. So, where to begin? Consider these three steps:
Determine the key variables that affect your operations.
Before you invest in a new solution, ensure that you understand which variables most affect factory productivity. Spend a day on the shop floor watching employees move through daily activities, and start an open dialogue concerning which tasks prevent them from working efficiently. Then consider how you might overlay those variables with IoT-enabled technology. Different solutions address different pain points, and you’ll want to make sure you understand what issues need to be addressed before you invest.
Identify areas of potential rapid implementation.
The longer you wait to address inefficiency, the more it hurts your bottom line. Determine which issues you can fix quickly, and prioritize new technology within those areas. Because IoT sensors are inexpensive and relatively easy to install, implementing new data collection software is generally a good first investment. However, make sure it aligns with your specific pain points.
Integrate your technology into algorithms.
AI requires an understanding of your processes before it can actively improve your factory. Determine how best your IoT-enabled technology can be programmed into algorithms to address common problems as they arise—and plan for slight variations on your pain points. Your solution must be able to recognize that two different vibrations could mean the same issue with your machinery.
One final piece of advice concerning implementation: avoid installing a solution on servers in-house. The equipment is costly, and you won’t have the power to quickly analyze sensor data. Instead, consider investing in a cloud-based AI solution. They’re much more powerful, able to turn around data analysis rapidly, and don’t require substantial upfront investments or lengthy implementations.
It’s Your Move
Addressing problems as they arise is no longer a sustainable business model. There are too many demands on the factory to allow for downtime. If you’d like to stay one step ahead of your pain points, or if you’d like to lay the foundation for an AI overhaul down the road, you’ll need to invest in today’s technology and empower your employees to work at maximum productivity. Only then will you be able to declare checkmate on inefficiency.
To take a deeper dive into the current state of factory AI and the developments we’re likely to see in the next 1-2 years, read Roy’s recent article, “The Digital Chess Match: AI’s Effects on Factory Floor Decision Making,” published by Supply & Demand Chain Executive.
Start transforming your business today
If you’re ready to take your discrete and industrial manufacturing business to the next level, we’d love to help.
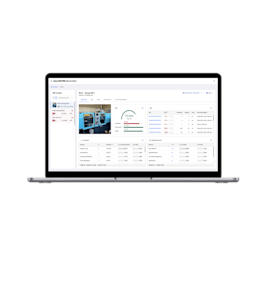