The Most Important Questions to Ask When Selecting a Chemical Manufacturing ERP
The Most Important Questions to Ask When Selecting a Chemical Manufacturing ERP
The Most Important Questions to Ask When Selecting a Chemical Manufacturing ERP
Apr 17, 2019
Jack Payne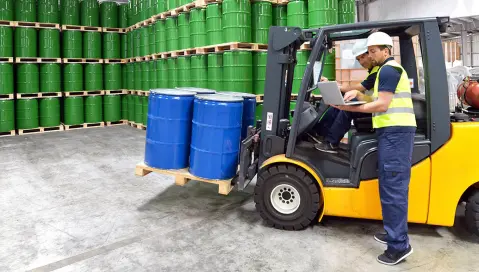
Chemical manufacturers require software that can handle precise measurements, manage multiple units of measure such as potency and multiple packaging units, maintain customer specifications for products, track actual lot characteristics and match to customer specifications and keep up with complex industry standards. However, with so many generic ERP systems on the market serving a wide range of industries, it can be overwhelming trying to figure out what option is best suited for your chemical business.
A generic ERP that works for every industry may not have the specific functionality to support your chemical manufacturing operations, and therefore may require a substantial amount of customization, workarounds or external spreadsheets to fit your needs. It’s essential to ensure that your ERP system can manage your current and future processes and handle all aspects of production from automatically linking stages of production to measuring yield. Being able to measure yield and actual output versus scheduled output accurately is a must-have for chemical manufacturers.
Fortunately, solutions that are designed specifically for the chemical industry exist. ERP systems can help improve value by better managing inventory, controlling formulation, and improving integration and visibility of information between functions and across the enterprise.
The first step in the ERP selection process is understanding your company’s specific requirements. Determining your key success needs for your operational environment is critical and will help make the decision-making process much easier.
To help, we’ve outlined the critical functionality required and subsequent questions you need to ask your ERP vendors to make sure you choose the best system for your chemical manufacturing business.
Managing Multiple Units of Measure, Potency and Multiple Package Units
An ERP system for your chemical company should handle multiple units of measure, such as weight and volume, for receiving, creating, storing and selling the same item. In many situations, a static conversion factor between weight and volume will be inaccurate when there are possible variations in the density between lots or batches. When you value or sell a liquid chemical based upon the dry weight percentage contained, that percentage may vary from one lot to the next.
You may be able to measure by weight with scales and load cells, but value and sell by volume, so an accurate conversion is critical to your success. In order to accurately manage and track these types of lots in a chemical company requires a formula-based conversion instead of a static conversion factor. With a formula-based conversion, you may measure the volume via a flow meter with a sample to measure specific gravity, and thus the actual weight can be calculated accurately. As you load tankers for shipments to customers, measuring the weight along with specific gravity results in the volume. Similar methods would be used for accurately measuring, valuing and selling products based upon a contained dry weight or potency value. An ERP system designed for chemical companies can easily calculate the percent dry weight and percent potency along with physical measurements such as weight.
Many chemical companies produce a bulk intermediate product that is packaged in multiple container types and sizes such as quarts, gallons, pails, drums and totes. This can vary from a handful of packages to many package types if you include either private label or country-specific packaging options. The generic ERP system typically requires a different part number to be created, managed and inventory tracked for each combination of bulk intermediate and package types. For a company making 100 different bulk intermediates that could be packaged in 50 different package types, there are results in 5,000 unique product masters that must be created and managed. Using a packaging unit of measure feature in this chemical company would result in only having to create and manage 100 product masters, record the package unite of measure and quantity during the packaging process.
Questions You Should Ask About Measurement:
Does the ERP system provide the capability to track and display inventory quantities in multiple units of measure simultaneously?
Does the ERP system provide the capability to buy/receive and sell/ship in any unit of measure with accurate conversions?
Are formula-based unit of measure conversions supported?
Are multiple packaging units of measure for each product/part code supported?
Managing Product Costs
The ability to track actual costs and compare to standard or estimated costs can have an immediate value-adding impact on your business. Visibility into sustainability, inventory valuation along with the ability to forecast profitability based on production costs allows you to have a real impact on your bottom line.
Properly managing your production costs with the help of an ERP designed for the chemical industry will give you the ability to monitor against standards, eliminate input errors, and account for non-production costs and roll them into your product costs.
There should be options to value inventory by methods other than standard cost. While standard cost is commonly used with the objective being to track and manage the cost variances, having an ERP system that can report where the variances are and why they are occurring is critical. With many raw material commodities whose costs vary often, an ERP system should allow you to calculate new standards and revalue inventory at any frequency needed, not just annually. For those companies that want to use actual costing, options for either weighted average cost or actual cost by lot should be available, and that system should continue to measure, report and identify reasons for those costs.
If you are using formula conversions for calculating and tracking inventory quantities by potency or some other variable attribute by lot such as percent solids, an ERP system designed for chemical companies should be able to cost the inventory by the potent unit of measure.
Additionally, the ability to forecast and manage future costs is key when you are dealing with commodity or market fluctuations in raw material costs. Being able to simulate future costs and perform what-if cost scenarios easily and compare prevents you from being surprised at month end and to get ahead of the market in pricing your products.
Closely tied to market price fluctuations and contract manufacturing or toll processing is the ability to base selling prices on agreed to Market Costs plus Margins without having to create complex manual spreadsheets that could easily miss increased costs.
Questions You Should Ask About Product Costs:
Can actual costs be tracked and compared to standard or estimated cost?
Do you have options for standard cost, weighted average cost or actual cost by lot?
How are costs for co-products and by-products handled?
Can the estimated cost of a process specification be compared with the actual lot cost?
Can future costs be used to provide what-if comparisons of total cost?
Can costs be date driven?
Meeting Customer Specifications
In a generic ERP system designed to support traditional discrete manufacturing, the quality tests and results are typically a Yes/No or Pass/Fail. Either the finished product works (pass) or it doesn’t (fail), resulting in either re-work or scrap.
In a chemical company, there are product specifications that typically have acceptable ranges with a minimum and maximum acceptable value. These specifications can either be industry based or set by the chemical company for their specific products.
However, a customer’s specific need for a product, or possibly the customer’s environment or actual equipment that it is used on may result in a range that works best for the customer. A generic ERP system that uses a Pass/Fail acceptable criteria cannot manage unique customer specification. You need an ERP system designed for chemical companies that can support both industry and customer specifications with the capability to manage production and set quality control test limits based on customer specifications. The ERP solution should be able to track the variable attributes of each batch or lot and then match lots in inventory to the customer’s specifications, as well as provide certificates of analysis or completion to the customer specification. This is a fairly unique, yet critical component specific to the chemical industry.
A chemical-specific ERP application should be able to employ formula specifications to manage the variations of customer processing and packaging specifications. This allows manufacturers to optimize their formulas so they can create the very best quality product while reducing scrap, waste and minimizing set-up time.
Questions You Should Ask About Meeting Customer Specifications:
Does the system provide the capability to track unlimited variable attributes by batch/lot?
Does the system provide the ability to specify quality control tests with specific minimum/maximum acceptable values instead of pass/fail test results?
Does the system provide the ability to specify either industry or customer specifications for acceptable attribute ranges?
Does the system provide the ability to source inventory lots based on customer specifications and actual lot attributes?
Putting Industry Expertise First
Looking for a system designed and developed for the chemical industry that can manage your unique measurement requirements, handle your current operational and costing processes, and help you meet regulatory standards will ultimately make the ERP decision-making process easier and more effective.
Download the ERP Checklist for the Chemical Industry
For a more in-depth look at the key functionality and questions, you should be asking your ERP vendors, download our ERP Checklist for the Chemical Industry.
Get in touch today to speak to a software industry expert
To grow your business, you need a purpose-built ERP for process manufacturing. We're ready to help—reach out today for your free no-obligation consultation.
