An Alphabet Cocktail for Manufacturing, Maintenance and Production
An Alphabet Cocktail for Manufacturing, Maintenance and Production
An Alphabet Cocktail for Manufacturing, Maintenance and Production
20 May 2020
Aptean Staff Writer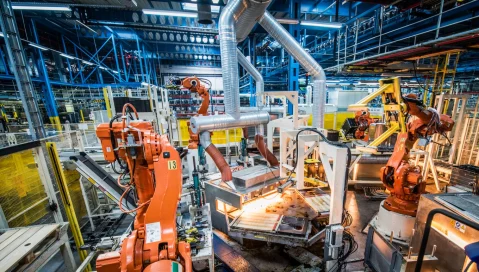
The goal of any manufacturer and production organization is fairly simple: get the most out of your equipment (assets), while producing quality goods. So how and where do each of the ingredients of the software system alphabet cocktail come into play?
CMMS (Computerized Maintenance Management System) is the absolute lifeblood of any top maintenance organization. You must be able to track who is doing what on each asset, what was done, what parts were used and so forth. You should be able to track your inventory and schedule your preventive maintenance, all completed on a mobile device. CMMS is the first key ingredient in the alphabet cocktail.
Top of the line CMMS systems have grown into incorporating EAM (Enterprise Asset Management). An EAM system takes things to the next level by tracking everything around the entire lifecycle of the asset: when was it purchased, from where, what sort of warranty is in place, tracking overhauls and depreciation. So now you are tracking everything you need to know about your equipment with a CMMS/EAM solution, or are you? The next key ingredient in the alphabet cocktail is OEE (Overall Equipment Effectiveness). It is one thing to fix your equipment when it breaks down or better yet try to prevent those breakdowns with an aggressive preventive maintenance program. Let’s remember one of the key goals of manufacturing and production is to get the most out of your equipment. This is where an OEE system comes into play.
The history of OEE can be traced back to metrics developed by Seiichi Nakajima in Japan during the 1960s, to evaluate how effectively a manufacturing operation is utilized. OEE is based on availability, performance and quality rate.
OEE measurement is becoming widely accepted as an overall measure of manufacturing effectiveness. However, when correctly applied, OEE is much more than a management benchmark. It is a powerful troubleshooting tool that identifies areas for improvement at the functional level.
It is important to remember that OEE is part of an overall improvement program and NOT just another KPI to measure. OEE is at its best when it is focused on one single asset or a synchronized line. Of course there are numerous studies of what a “World Class” OEE number is for a manufacturer or production operation. These “World Class” numbers should not be used as a benchmark. Remember OEE is about attaining improvements. A “World Class” continuous production operation might have an OEE number in the 90s, but if you take your operation from the low 40s up to the 60s you have achieved 50% improvement!
How to Improve OEE’s Three Keys
What can your maintenance program and your CMMS/EAM do to contribute to improving OEE’s three keys of availability, performance and quality? That brings us to the fourth ingredient in our alphabet cocktail, TPM (Total Productive Maintenance). TPM is a plant improvement methodology which enables continuous and rapid improvement of the manufacturing process through use of employee involvement, employee empowerment and closed-loop measurement of results (OEE).
TPM is about bringing things full circle back to your CMMS and your PM program. The key though is, now it is not just seen as a maintenance department function. The focus is how you maintain your equipment throughout its life cycle. This requires the buy in from top management as well as front line production staff and operators. Production operators for example can and should be trained on simple preventive maintenance activities such as lubrications, cleaning and how to note and track those activities within your CMMS.
People, Culture and Attitude
Remember when we talk about OEE and TPM we are not talking about a technical IT-project, sure technology will and does play a key role but more importantly we are talking about people, culture and attitude within your manufacturing operation.
OEE and TPM projects need to have clearly focused primary financial business goals such as reduce scrap, reduce short stoppages and improve lead times. OEE and TPM are about continuous improvement in your manufacturing and production environment.
Want to learn more about how EAM or OEE solutions from Aptean can help your business? Contact us today to chat with one of our experts or schedule a demo.
Related Content
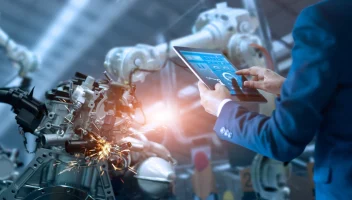
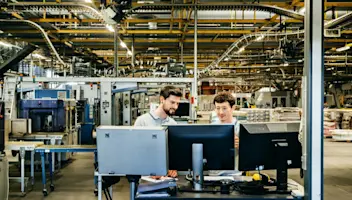
Ready to start transforming your business?
We’ve got the specialized EAM solutions you need to conquer your industry challenges.
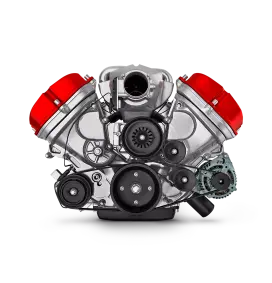