What Is TPM and How Do You Define TPM?
What Is TPM and How Do You Define TPM?
What Is TPM and How Do You Define TPM?
6 Apr 2020
Aptean Staff Writer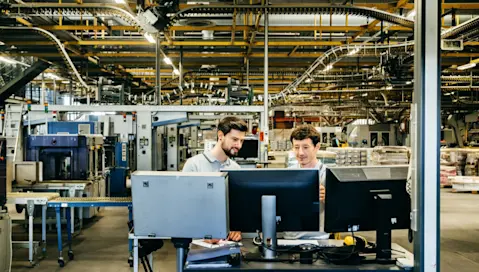
TPM stands for Total Productive Maintenance. It is a concept that creates a team-based system, which constantly aims to improve equipment effectiveness by focusing on proactive as well as preventative techniques for increasing plant and equipment reliability. It can be considered the medical science of machinery, where the goal is to maintain and increase the production by keeping emergency and unscheduled maintenance to a minimum and thereby preventing machines from breaking down.
How Does TPM Work?
TPM is a system of maintaining and improving the integrity of production along with quality systems through the machines, equipment, processes and employees. The operators, maintenance people and engineers together with equipment suppliers and others who are working on the machines can be involved in the maintenance process, where they work together to improve the overall equipment effectiveness. The TPM strategy operates with the idea that everyone in a facility should participate in the maintenance of machinery at the plant. In fact, those who are most familiar with the machines they work with, would be in charge of the maintenance of them.
What Are the Benefits of TPM?
First of all, by monitoring changes with equipment, critical problems are spotted earlier and the maintenance team can go through with earlier diagnostics on possible issues, rather than reacting to an emergency breakdown; hence the team will experience higher performance and morale with fewer breakdowns.
With regular maintenance, technicians can spot problems in advance. This means they are less likely to take dangerous risks in the high-pressured, rushed event of equipment breakdown. Furthermore, if all staff involved are keeping an eye on maintenance, small fixes will be detected faster and the issue can remain under control. TPM takes the pressure off the maintenance team, so that they can concentrate on bigger errors, which will increase the overall performance and efficiency of the business operations.
TPM and OEE – How Are They Related?
OEE is short for Overall Equipment Effectiveness and is the main performance metric continuously measuring the TPM, which seeks to improve processes and equipment through regulations. OEE identifies the percentage of manufacturing time that is truly productive, and will indicate the efficiency of the production. It will measure the quality (the good parts that are manufactured), performance (time that is spend on each part) and availability (the ‘no stop time’ on the machines). By measuring OEE as well as the underlying losses, important insights will be available to successfully improve the Total Product Maintenance (TPM).
CMMS Software in a TPM Solution
Business owners want to make sure that everything runs as planned. Unnecessary accidents, product defects and failures are unwelcome, which is why companies wisely choose to get CMMS software installed. CMMS stands for Computerized Maintenance Management System, and is a software intended to support as well as make it simpler for businesses to implement TPM. The CMMS software aims to bring the general goals of TPM more easily into the hands of businesses by simplifying data and turning TPM into something staff can see and track on their computers, tablets and other mobile devices.
Want to learn more about how CMMS/EAM or OEE solutions from Aptean can help your business form their TPM Solution? Read our blog if looking for Total Performance Management in an ERP for manufacturing.
Contact us today to chat with one of our experts or schedule a demo.
Related Content
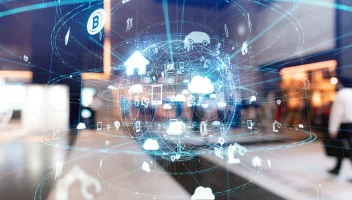
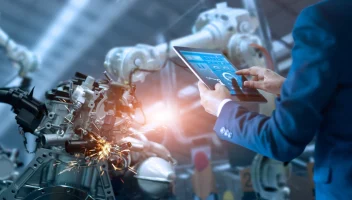
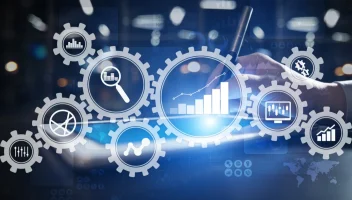
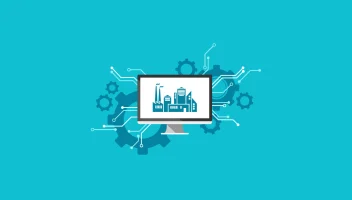

Discover industry-tailored software built by the experts
With deep technical know-how and a commitment to innovation, we deliver tailored software to businesses like yours. Reach out today for your free, no-obligation consultation with an industry expert.
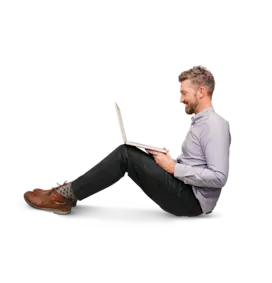