Before You Buy EAM Software, Ask Yourself These 4 Questions
Before You Buy EAM Software, Ask Yourself These 4 Questions
Before You Buy EAM Software, Ask Yourself These 4 Questions
3 Jun 2021
Fries Lefevere
Enterprise Asset Management (EAM) software is a big investment, so naturally you want a system that will deliver both immediate results and long-term value. But with so many solutions on the market, how can you be sure that you’re picking the right one?
EAM has the potential to drive major operational efficiencies for manufacturers, by digitizing your maintenance process. Well-chosen software will provide consistent product quality and minimize downtime, using built-in features and functions. And to help you find this software, these are the four questions you need to ask during the selection process.
1. What Do You Need EAM Software To Do for Your Business?
Fundamentally, every manufacturer invests in EAM software for the same reason: to manage the lifecycle of physical assets better. But the definition of ‘better’ is different for every business.
Maybe your primary motivation is to maximize asset use or reduce energy consumption. Maybe it’s to save money on maintenance costs. Alternatively, your core focus could be improving quality and efficiency, by identifying errors before they become a problem. Most likely, it’s a combination of all these things. But some will be more important than others.
Thinking strategically about your EAM program before it launches will give you a clear vision of how it fits into your operation. And you can use that focus to set up your new solution in a way that optimizes production steps cost-effectively, giving you greater piece of mind.
2. Where Are Your Biggest Weaknesses?
To help you prioritize maintenance improvements through EAM technology, you need to be honest about your current business challenges, as these will vary from plant to plant.
Consider your biggest vulnerabilities on both a macro and micro level. This shouldn’t be a decision motivated solely by the strategies of senior personnel; you need to talk to the people using the machinery to understand their daily work routines. They will tell you where everyday efficiencies can be achieved.
Bringing staff at all levels into the decision-making process will help you to choose EAM software that drives big results, and also gets everyone on board with change from the very beginning.
3. How Will the EAM Process Work Day-to-Day?
You’ll find some very sophisticated EAM solutions on the market that have great capabilities, but are incredibly complex to use. Ideally, you want software that can provide the functionality you need, in a way that’s easy for colleagues in all areas of the business to understand.
Look at the data you want to monitor, in order to keep maintenance running smoothly. This may include time-based indicators like real-time schedules, work order execution and preventative maintenance; materials indicators like spare part management; and budget trackers like cost control measurement. EAM software is also a way of safeguarding health, safety and the environment.
Consider too how your maintenance data will be delivered. Many manufacturers find mobile EAM software incredibly useful, as engineers can view and respond to notifications from any location and maximize asset performance anywhere in the business.
4. What Does a Successful EAM Software Implementation Look Like?
In order to prove that your manufacturing EAM software is a valuable investment, you need a measure of success. That means analyzing and reporting on maintenance data against a defined set of KPIs.
From energy output and machine uptime to engineer response times, there are a wide range of metrics you can include in your EAM program. And the results of these will feed into your wider business targets; whether that’s increasing reliability, improving regulatory compliance, or introducing more sustainable initiatives.
Find a Solution That Fits Your Business and Your Budget
The right EAM software is different for every manufacturer, as it depends on where your biggest weaknesses lie, and what you want to improve. By understanding your objectives in greater detail, you can select a solution that fits your business and your budget.
Whatever your priorities, one thing is common for all manufacturing companies: with an EAM solution in place, you will be able to track every single elements of your production, to ensure that everything is running smoothly. And the functionality it gives you will minimize unplanned repairs and extend asset life, to improve the customer service that your business can deliver.
Aptean’s EAM software gives manufacturers all the information you need to maximize the asset performance, control maintenance costs and improve operational efficiency. Discover How, Now.
Related Content
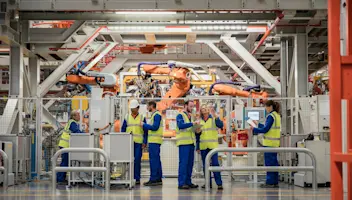

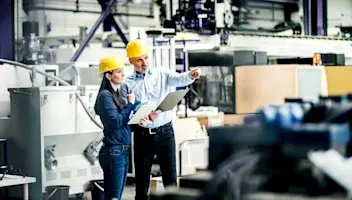

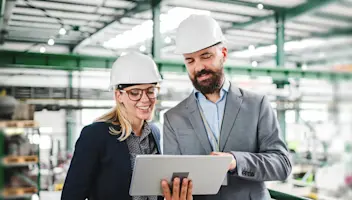
Start transforming your business today
If you’re ready to take your discrete and industrial manufacturing business to the next level, we’d love to help.
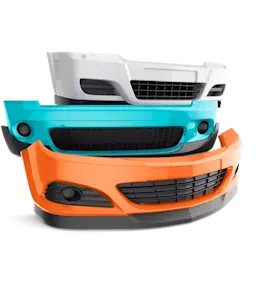