Featured in this post
Boost Customer Experience With Uncompromising Food Quality Assurance
Boost Customer Experience With Uncompromising Food Quality Assurance
17 Oct 2023
John McCurdy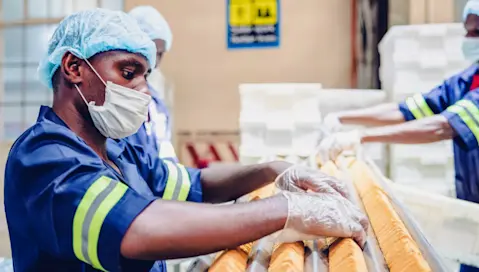
Think back to your most recent visit to the grocery store or supermarket. If you had to guess how many different brands were represented among all the items you passed by, what would your estimate be? Depending on the size of the retailer, the number could well be in the hundreds or thousands. Even within specific categories, it’s fairly unusual for there to not be a considerable range of choices.
The point being, consumers these days don’t want for options—and because they can easily switch to an alternative if your offering doesn’t satisfy them, food and beverage businesses must prioritize customer experience. That means ensuring the quality of your products, which requires attention to both a number of criteria as well as the expectations of the savvy, modern shopper.
With your organization’s profitability and market share potentially at stake, you can’t afford to build your quality assurance strategy on inefficient and error-prone manual processes. You need industry-specific software with purpose-built features to tackle the five major facets of food and beverage product quality—safety, taste, consistency, freshness and appearance.
To prepare you for the challenge of food quality assurance, we’re going to cover those five facets and share how the capabilities of food and beverage enterprise resource planning (ERP) solutions can aid your efforts. Consumers expect nothing less than excellence and will likely switch to another brand should your company fail to meet their standards, so now’s the time to get up to speed.
1. Safety
Considering the fact that guaranteeing your items are healthy and safe to eat is “table stakes” at this point, it might seem like safety can go unsaid when it comes to evaluating quality. But the reality is that food safety and quality assurance are inextricably linked, because without the former, the latter isn’t worth the time it takes—the product is already compromised.
To safeguard you on this front, food ERP software provides bidirectional traceability through lot and sublot management features. By maintaining a complete picture of the supply chain, including each transaction and the associated details, you can track the paths taken by your raw materials and finished products. Advanced systems allow you to drill down to the individual item level for granular data.
Additionally, ERPs for food manufacturers also offer functionalities to facilitate product recalls, streamlining the process of tracking affected items back to their origin or downstream at their destination. And for the critical processes of allergen screening and segregation, product specifications tools enable you to make declarations highly visible for users so that proper care can be taken.
2. Taste
Perhaps the most subjective aspect of quality, while simultaneously possibly being the most important, is taste. Obviously, there is no one “best” taste for a given item, but most have certain flavors with which they are associated, and how well the individual product conveys them tends to have an outsized impact on how much the consumer enjoys them.
Here, the recipe and formula management features of food and beverage ERP software can enhance your operation's ability to reliably execute the measurements and manufacturing processes that produce great-tasting results. With these tools at your fingertips, you can dial in ingredient levels; cooking temperatures and times; and other steps to follow with precision.
3. Consistency
Because food is associated with comfort and joy—and meals are frequently some of the high points of our days—consistency is critical for customer satisfaction, as even a single disappointing experience can lead buyers to select an alternative next time they’re shopping. Bad batches are bound to happen, but it’s in your best interest to keep them to a minimum if you want to maximize customer satisfaction.
Beyond the dependability that the aforementioned recipe and formula controls provide, food ERP systems come with non-conformance management functionalities that allow you to receive, document, categorize, process and follow up on complaints received. While these processes fall more under quality control due to their reactive nature, they can also inform continuous improvement in quality assurance.
4. Freshness
Just about every food and beverage product has a limited shelf life, and for some, their peak level of freshness is just a matter of days. Tracking the windows of viability for all of your goods at once to ensure that materials are used before they go bad and your finished goods are delivered fresh is no simple matter, but it’s necessary to maintain your business’s reputation for high quality.
Thankfully, there’s a technological solution for this challenge, and that’s the expiration date management tools that ERP platforms for food and beverage businesses provide. These offer high-level visibility into freshness ranges and promote first-expiry, first-out (FEFO) consumption. Advanced solutions—like Aptean Food & Beverage ERP—can even deploy alerts when lots are nearing expiry.
5. Appearance
While most consumers can forgive some minor flaws, and food that doesn’t conform to the “normal” appearance for the product can still be delicious, the qualitative characteristics of your items still have a considerable effect on customer experience. Certain colors and shapes are expected for most items, so your approach to quality assurance must account for how your products look.
Food ERP software has dedicated quality management features that enable you to set the criteria that goods must meet upon inspection, as well as what deficiencies will trigger a hold or necessitate scrapping the item entirely. The system helps to ensure that each prescribed quality check is completed, prompting users at the appropriate time and preventing items from moving forward until they’re done.
Inspection status management features offer additional visibility into the state of your products and progress in quality assurance processes. These help to standardize and enforce the steps required to meet your brand’s quality standards, and all of the latest updates to statuses are reflected in the organization-wide system in real time, keeping everyone in the know.
Shine in Food Quality Assurance With Aptean Software
Quality assurance in the food industry is imperative, no doubt about it. To protect your reputation and maintain customer loyalty—not to mention promote profitability—your food and beverage business must do everything possible to consistently delight your customers, and that takes having both the right strategy and technology for outstanding food quality assurance.
ERP solutions for food and beverage companies have become so popular in no small part because they deliver the functionalities that organizations like yours need to succeed in this area. But beyond securing the right software, you should also seek to find a provider that’s more than just a vendor. Not all providers are created equal, and there are some compelling reasons to believe Aptean stands out.
Firstly, we strive to act as a partner for each of our customers, beginning with assistance in creating a project roadmap through to dependable service and support. We also know the food and beverage space well, as our team has collective decades of hands-on experience and can offer advice on best practices and how to overcome unique challenges.
What’s more, we also offer flexible cloud deployments on the Software as a Service (SaaS) model, which is increasingly the way to go given the greater scalability, enhanced data protection, stronger cybersecurity and broader accessibility the setup provides. Plus, Aptean Food & Beverage ERP is built on the Microsoft Dynamics 365 Business Central platform, giving it a user-friendly feel and interface.
Finally, we’re proud of the recognitions we’ve received, including Frost and Sullivan’s 2023 Customer Value Leadership Award in North American ERP Software for the Food and Beverage Industry. That’s proof of our commitment to not only our clients, but the wider food and beverage world, and a testament to the performance of our products.
Learn more about our food ERP and how it helps businesses like yours excel in multiple operational areas by reading our blog post on Building a Business Case for Food and Beverage ERP, and feel free to contact us with any questions.
Related Content
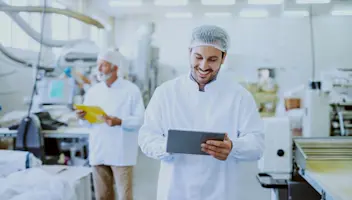
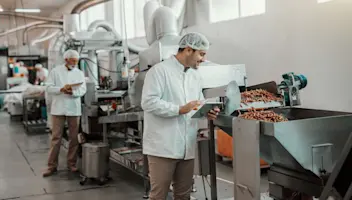
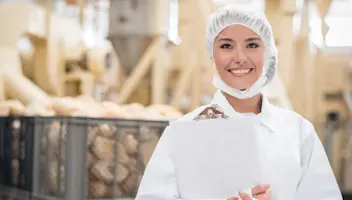
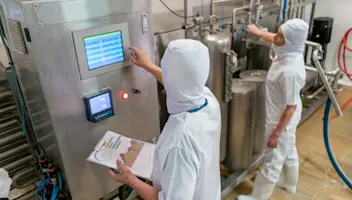
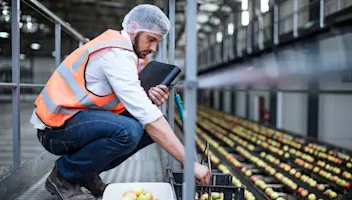
Get in touch today to speak with an expert in your industry
To grow your business, you need a food ERP built specifically for your industry challenges. We're ready to help—reach out today and we'll help you find the right solution.
