How to Boost Efficiency and Customer Service Levels for Multi-Depot Routing
How to Boost Efficiency and Customer Service Levels for Multi-Depot Routing
How to Boost Efficiency and Customer Service Levels for Multi-Depot Routing
28 Ene 2021
Jim Endres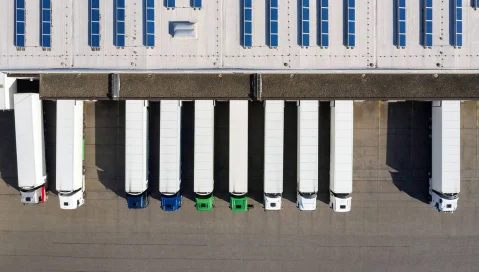
Most large distribution companies don't start large. They grow from smaller ones—either organically or via acquisition.
When it comes to delivery operations, most companies start with one distribution center (DC) and dispatch all trucks from this facility. Then comes expansion and the addition of DCs in different geographical areas—with separate fleets dispatched from each one.
In a perfect world, the DCs would be strategically located, and the fleets would be deployed with maximum delivery route efficiency in mind. But the truth is, distribution networks tend to evolve in a relatively haphazard way—meaning fleet operating costs skyrocket as a result.
So, how do you make sure you're achieving maximum efficiency in your multi-depot routing? And more importantly: can you drive efficiencies while improving customer service levels and even pushing back order cut-off times?
With advanced routing and scheduling software, the answer is yes.
Many routing software solutions are designed to treat each DC as a separate entity when planning routes and delivering orders. This means that orders must be assigned to specific DCs instead of allowing the system to determine the most efficient origin point for the delivery. But there's a smarter way.
A Holistic View of Routing, Even Into the Future
Advanced routing software, designed for multi-depot routing, allows your team to plan across an entire region. That way, planners can be confident they are assigning orders to the DC that gives them the most efficient, achievable route while also satisfying customer demands for tight time windows and reliable delivery scheduling.
To achieve this, multi-depot routing software uses sophisticated algorithms that dynamically assess myriad critical factors, such as available inventory, delivery quantities, customer addresses, time windows, truck sizes and driver shifts.
While trucks in each fleet continue to start at and return to the same depot, the depot boundaries automatically flex according to demand and resource availability. Because the software achieves this in minutes, it's possible to respond quickly and effectively to changes in delivery demands, continually optimizing resource usage across your entire operation.
The efficiencies gained with multi-depot routing software allow you to reduce delivery lead times, and offer customers later order cut-off times. It takes less time to plan routes, and the routes are also the fastest possible. More efficient use of your fleets means decreased overtime and spot-hire costs, too.
In fact, the software helps you take a holistic view of your entire delivery network, not just now but into the future. You can bid for new business, confident that you're offering the most efficient routes, plus you can carry out any amount of "what if" modeling to help determine the most economical location for future distribution centers.
When this kind of route planning functionality is available in the cloud, as it is with Paragon Routing & Scheduling Cloud from Aptean, your staff can access multi-depot routing capabilities from any location with an internet connection. This makes it easy to centralize or coordinate these functions without being tied to physical access points.
Routing software aids in dispatching orders from the most efficient DC and allows you to treat your vehicles as one shared fleet. With an integrated fleet routing strategy, you can reduce empty miles by assigning pick-ups and deliveries to the best-positioned vehicle and driver.
Real-life Examples
When Frozen Food Express centralized its route planning activities using Aptean Multi-Depot routing software, it discovered it could free up local staff to focus on operating the service centers instead of being under pressure to find time to plan deliveries. The company saw revenue increase by 9% in the first six months of implementation.
In another case, the Aptean Multi-Depot software streamlined operations for a distributor of fresh food based in Dallas with 14 DCs across the region. The company needed to serve a new customer in Atlanta. Their routing software couldn't plan for multiple DCs, so they created a best-guess model that involved picking orders in Nashville, TN, then cross-docking in Memphis for final delivery to Atlanta. To achieve this, the company was going to build a new cross-dock facility.
When they implemented Aptean Multi-Depot routing software, they made a surprising discovery—it was more efficient to deliver product direct from Nashville and Memphis. And most interestingly: some of the product was best delivered out of Jackson, MS, even though it was further away. By identifying these efficiencies, the food distributor avoided the cost of setting up a new cross-dock and saving on distribution costs.
At National Food Corporation, once the transportation manager implemented Aptean's Multi Depot functionality to automate planning, the resulting optimization of plans for the company's 2,500 weekly deliveries via 50 multi-stop routes could be achieved by a single person. The company is now "leading its industry with transportation cost savings," according to the CEO.
Would you like to know more about the benefits of using multi-depot delivery route planning to get a holistic view of all your distribution and fleet resources across your entire operations? Find out how, now.
¿Todo listo para transformar tu negocio?
Tenemos las soluciones TMS especializadas que necesitas para superar los desafíos de tu sector.
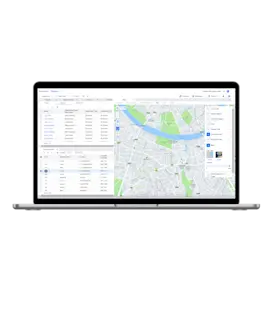