Destacado en este post
The Complete Guide to OEE Software
The Complete Guide to OEE Software
23 Jun 2022
John McCurdy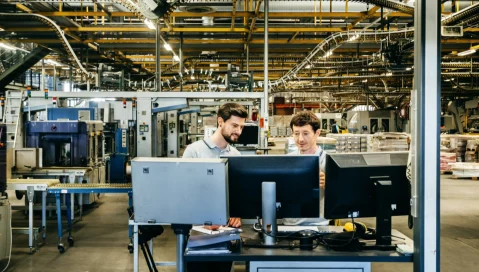
Across the many segments that make up the broader manufacturing industry, one truth is evident—productivity is king. While quality, safety, compliance, supply chain management and a host of other matters are critically important, the performance of your operations will always primarily be evaluated on how smoothly and quickly your lines are running to produce the goods your brand is known for.
The chief obstacles to productivity are unplanned downtime and inefficiencies. To some degree, these issues “come with the territory” of working in the manufacturing space, as it would be more or less impossible to avoid all equipment malfunctions and imperfections in your processes, but there are best practices and purpose-built solutions that can help immensely in your efforts to improve results.
These measures are all centered on the collection of data and using the information captured to derive actionable insights that lead to better outcomes. The digital platform that serves this purpose and is increasingly seen as a game-changer for manufacturing businesses is overall equipment effectiveness (OEE) software.
Here, we’re going to give you the complete rundown of these systems, their use cases, the advantages and features they offer and how to choose the right one for your company’s circumstances. With no further ado, let’s dive in.
What Is OEE Software?
Before you can understand OEE software, you first need to understand OEE as a metric and how OEE scores are calculated. Put simply, OEE is a measurement that allows manufacturers to compare their actual productive time against their available planned production time, and it is determined by multiplying three ratios (each expressed by a percentage):
Availability, which is the percentage of actual production time versus downtime and changeovers
Performance, which is the net production time versus idle time, shorts stops and reduced production speed
Quality, which is the production time without losses versus scrapped units and rework
Thus, OEE = Quality x Performance x Availability.
OEE software is designed to both capture the data necessary for these computations and automatically perform the calculations for you, giving you a highly visible and accessible figure by which to judge the performance of your equipment and processes. That, in turn, helps you identify issues that need to be addressed to drive continuous improvement.
Advanced OEE systems facilitate this process by integrating with your equipment and piping performance data into your platform in real time, which lets you make informed decisions on the fly and rectify problems as soon as they occur. This helps you get the most out of your time, machinery and materials, day in and day out.
What Are the Signs You Need an OEE Solution?
Now that you know what OEE software is, you may be wondering whether or not you need to implement such a solution at your facilities. These are some of the most common signs that you need to improve the overall effectiveness of your equipment with an industry-specific system:
Repeated failure to meet plan attainment either as a result of unplanned downtime or equipment malfunctions
Excessive rework and waste necessitated by products being compromised by faulty hardware or processes
Poor profitability and return on investment in raw materials
Lack of insight into what’s holding your operations back from peak performance
All of these are issues that can cripple a manufacturing business’s ability to remain financially sound, ensure customer satisfaction and determine root causes of the problems that are preventing the realization of better results. If you’re dealing with one or more of the above, now may well be the time to supercharge your digital transformation with an OEE solution.
What Kinds of Businesses Can Use OEE Software?
OEE systems are ideally suited for manufacturing companies, but that includes organizations across the full spectrum of that general category. The technology is equally applicable whether you engage in process manufacturing—that is, processes that involve recipes or formulas and result in goods that can’t be separated into their constituent parts—or discrete manufacturing, which involves a bill of materials (BOM) and industrial processes that create products that can be disassembled if necessary.
Your business can likely leverage this technology for improvement if you specialize in any of the following sectors:
Note that this list isn’t complete—there are many kinds of manufacturers, and just about as many different OEE solutions designed to be used by them. For optimal results, though, you’ll need to choose software that was designed specifically for organizations in your sector…but we’ll cover that point in more detail in one of the below sections.
What Are the Benefits of OEE Solutions?
The data and performance visibility that OEE software provides can lead to wide-ranging positive impacts, and not just in terms of productivity. Here are just a few of the benefits of these OEE solutions when they are put into practice and well-integrated in your day-to-day procedures:
Consistent plan attainment, leading to assured order fulfillment and better customer experiences
Greater efficiency in manufacturing processes through the identification and correction of equipment malfunctions and slow processes
Reduced scrap and wasted materials thanks to real-time monitoring of results that leads to immediate intervention in the case of an issue
Minimized idling time, short stops and losses in yield and at startup
Greater shop-floor accountability and a more connected workforce
It’s not too good to be true—your company can unlock all these advantages by deploying one streamlined solution and start seeing improvement with each successive production run. You do need to ensure that the OEE system you select offers the specific tools you need, so make sure to read on to the next section for a primer.
Key Features to Look for in OEE Software
Some functionalities are shared by all OEE solutions—for example, efficiency analytics are so central to the software’s purpose, you’d be hard-pressed to find a system that didn’t cover that in some regard. There are several features that set the best of the bunch apart, though, such as:
Visibility into real-time performance metrics via a user-friendly and intuitive interface
Robust visualizations that allow you to determine which processes are flowing smoothly and which are hindered by issues
Mobile accessibility for flexibility and informed decision-making on the go
Direct integration with equipment for up-to-date readings and results that lead to actionable insights
Cost and profitability monitoring that helps you understand where you’re losing money and where your big “wins” are
Operator reporting functions to give your key personnel agency and the ability to better connect operations and maintenance
For process manufacturers, paperless quality compliance with a full suite of statistical process control (SPC) tools to assure adherence to pertinent regulations and standards
With features like these on your side, you’ll be well-equipped to handle what comes your way in the dynamic and fast-paced environment that is your typical manufacturing facility. The sense of greater control and awareness allows for swift and confident action, helping you never miss a beat and stay on track despite a hectic pace and any unforeseen hurdles that must be overcome.
Identifying the Best OEE Solution for Your Business
To start the process of finding the right OEE system for your company’s situation, you need to answer some critical questions. This will help to ensure that you select software that can drive better outcomes in the areas that matter most for your organization while offering a comprehensive collection of tools that suit the nature of your procedures and goods.
Meet together with other key stakeholders to determine the following:
The goals you’re looking to achieve—this could be ramping up capacity, rooting out inefficiencies, reducing waste, fostering greater transparency or any of a number of other aims
The data you need to capture—be that efficiency metrics, the number of compromised items that have to be scrapped during each run, the effectiveness of your teams or the time taken during changeovers
The methods you’ll use to interpret the information—make sure that the analytic features of the solution produce easily interpretable and in-depth reports, charts and graphs
The primary users of the system—it’s vital that the interface is approachable, with dashboards that can be navigated without confusion or an undue number of prompts or inputs; and configurable, including options to filter data by type, date, product line and more
The plan should a problem arise—considering OEE platforms are designed to help you identify when something’s gone awry with your equipment or procedures, you’ll need to determine your course of action when this occurs so that the issue can be resolved quickly
Above all, keep in mind how crucial it is that you select a solution that is tailored to not just manufacturing businesses, but your specific segment within that broader classification. The OEE platform that claims to do everything for all varieties of operations may not have the specific tools needed to tackle your unique challenges, and adding special customizations to rectify that could be costly and problematic when updates need to be applied.
The Advantages of Aptean’s Overall Equipment Effectiveness Software
We recognize this is a lot of information to take in and that you’ll likely have further questions as you begin to examine the state of your manufacturing operations, determine how you can improve and assess the fit of OEE software for your business. And once you reach the stage where you’re researching the different options on the market, you may find yourself wondering what sets one package or vendor apart from another.
Here at Aptean, we develop our solutions with an in-depth understanding of the inner workings of manufacturing businesses like yours. That’s how we’ve tailored both Aptean Process Manufacturing OEE and Aptean Industrial Manufacturing OEE to align with the needs of such complex organizations and their highly specialized processes and carefully crafted finished goods.
Our teams have decades of collective experience and really “speak your language” when it comes to what you deal with on a daily basis. We know industry best practices well and have built our systems to help you implement them at your company, and we also bring true technical expertise when it comes to deploying and maintaining organization-wide platforms like OEE systems.
We’re ready to help you implement the OEE software that’s right for your circumstances. With a powerful set of features that are immediately accessible out of the box, our solutions empower you to collect critically important data, improve productivity and facilitate continuous improvement. Meanwhile, our dedicated IT teams will have your back, providing maximum uptime, effective troubleshooting and streamlined updates.
So, ready to hear more about what Aptean’s OEE solutions can do for your manufacturing business? Contact us today, or feel free to request a personalized demo to see the software in action.
¿Todo listo para transformar tu negocio?
Tenemos las soluciones OEE especializadas que necesitas para superar los desafíos de tu sector.
