Ask Yourself These 6 Questions When Shopping For a MES
Ask Yourself These 6 Questions When Shopping For a MES
Ask Yourself These 6 Questions When Shopping For a MES
Mar 17, 2020
Joey Carabetta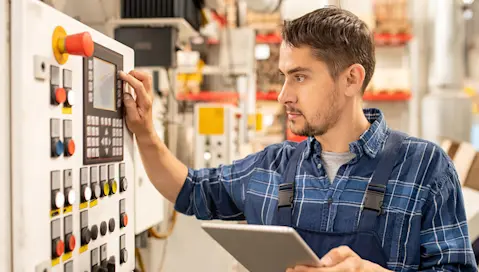
There’s nothing worse than buyer’s remorse, especially when it involves a purchase that’s not so easy to return, like business software. While shopping for business software may be a challenge, once you have it, you position your company to have a valuable advantage over your competitors.
We believe a manufacturing execution system (MES) can only help you—it’s a way to unify your data, run your plant more effectively, go paperless, scale with your growth, and control your shop floor.
Nonetheless, an MES is a big purchase, and it’s not one to be made lightly. And we take that just as seriously as you do. Which is why we came up with six questions we’d encourage you to consider before making your factory-changing buy.
1. What Types of Analytics and Reports Do You Want to Run?
Historically, the red book has been the central source for all factory information and data—shift changes, problem areas, protocols, shipping reports, open communications, product details, etc. It’s a time-consuming process to dig through that binder, and even then, you may not find exactly what it is you’re looking for.
When it comes to reporting and analytics, real-time metrics and easy-to-use technology are invaluable. With the right MES, everything is in one place; it’s easy-to-find, and it’s organized. Each user can quickly access their own dashboards and reports to find the information they need to perform tasks, solve issues and make smart decisions.
Your MES should be able to deliver real-time feedback on plan attainment and overall equipment effectiveness (OEE) to optimize your manufacturing operation across your entire value stream.
2. Can the MES Scale and Adapt With Your Business?
Because the needs of your business are unique to you, a one-size-fits-all MES solution won’t cut it. You need something specialized to your workflow, products and demands. A forward-thinking MES vendor should be able to supply you with a solution that’s not only tailored to your industry, but is also able to scale and adapt as your business grows.
If your business were to grow and you were to add plants and factories to your enterprise, you need to be able to easily integrate those additions into your MES solution. Having a solution that adapts to your business over the years—instead of you bending your business to fit within the confines of your system—paves the way for you to excel within your marketplace in the long-term.
3. Is There Key Functionality for Now and in the Future?
When shopping for an MES, there are several key functionalities that you should look for: collaboration; analytics, paperless quality check sheets, integrated continuous improvement project management, labor planning and tracking; visibility from batching all the way through to the final product, and the ability to integrate with your ERP system. Whatever MES solution you select should be able to evolve to meet your industry needs… both now and in the future.
It’s easy to be swayed by a really good sales pitch, providing you with all the add-ons and customizations that look good and shiny now, but what about ten years from now? You should ensure that you’re working with a vendor who is invested in your industry and will offer new features to meet business and industry changes in the future.
4. How Quick Is the Deployment?
Implementing an entirely new system into your warehouse is a really big deal. It’s a big project that, in all honesty, will take some time. Doing it the right way means dedicating the right amount of time to deployment. Think about your needs, what processes you want to automate and streamline, any integrations you may want to make (such as with an ERP), the people that need to be involved, and start realistically planning your deployment with your trusted vendor.
Having said that, however, an MES implementation shouldn’t be a long, drawn-out process. Anywhere from six to 12 weeks is appropriate, and Factory MES, in particular, can be deployed in as little as four weeks. We suggest you spend time mapping out your implementation timeline—including ample time for testing and training—and then adjust as needed along the way.
Be sure to ask your vendor what’s involved in the implementation process. Will there need to be coding or building? Does there need to be programming? Can the vendor offer best practices and industry expertise throughout the process? These are valuable questions to ask before you jump in.
5. How Do You Ensure You Meet Product Quality Compliances?
Shifting away from paper-based compliance to true paperless quality compliance is key. An effective MES will provide you with the ability to track compliance. An intuitive and easy-to-use dashboard should allow you to let go of monitoring line checks for completion and instead offer preventive controls that align to initiatives such as Safe Quality Food (SQF), Food Safety Modernization Act (FSMA), British Retail Consortium (BRC), and Global Food Safety Initiative (GFSI).
Earlier in this post, we asked you to consider the types of analytics and reports you want to run. The ability to do this in real-time time is essential in terms of quality compliance. It makes tracking a problem easier, and it makes management simpler.
6. Have You Considered Your Vendor Options?
This is one of the most valuable questions to ask before you buy an MES solution for your factory. When implementing a new software system, it’s beneficial for you to work with a partner that you trust and who understands not only your industry but your goals and expectations as an organization.
You not only want a vendor who’s with you throughout implementation but one who remains involved to the degree that you’re comfortable with, and offers the service and support you’ll need after the implementation.
Aptean Factory MES is purpose-built and designed with you in mind; the system itself fits within your existing work practices and is flexible to change as your business adapts, which makes it exceptionally easy to use. There’s no coding, no programming, and no workarounds. Aptean’s a trusted partner, a company that folks enjoy working with, and we’d love to put in that good, old-fashioned hard work for you and your business.
If you want to talk about how Factory MES can work for you and your business, reach out to our team of MES software experts. We’d love to chat.
¿Todo listo para transformar tu negocio?
Tenemos la solución MES especializada que necesitas para superar los desafíos de tu sector.
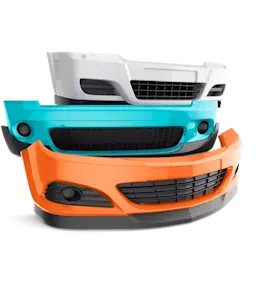