How to Best Use EAM Trends – Practical Advice to Improve Your Organization
How to Best Use EAM Trends – Practical Advice to Improve Your Organization
How to Best Use EAM Trends – Practical Advice to Improve Your Organization
Jun 26, 2020
Stephen "Stevie" Hay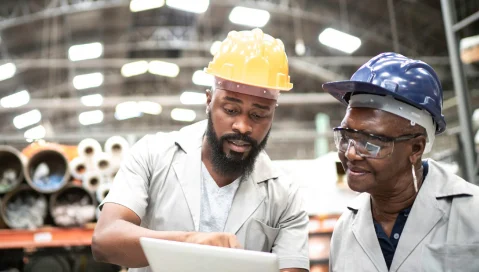
The world is going through rapid-pace change. You know this as well as we do. We’re all facing enormous industry pressures in our working lives. This means it’s more important than ever to try to future-proof your business so that you can stay solvent and relevant in the long-term. Though it seems like this is a storm that’s forever-lasting, there’s bound to be a break. Until then, please know that you’re not alone, and the challenges you’re facing are the same challenges many other enterprises are facing. We’ll weather the storm together.
So, where to focus your attention? That’s the next logical question. With so much to worry about, so much to attend to, and so many competing priorities, how do you focus on what’s meaningful? What priorities are going to change your business for the better?
We at Aptean believe that by focusing on data-driven decisions, asset transparency and IT/OT integration, you have the power to improve all facets of your business.
Why?
Because by focusing on these three components of your business, you’re growing your predictive maintenance maturity.
PwC surveyed 280 companies on their predictive maintenance practices. To best assess current practices, a framework was created to identify the levels of maturity along the predictive maintenance journey. Because as companies move through this framework—from Level 1 to Level 4—it grows its ability to make data-driven decisions, successfully assess transparency, and more fully integrate your IT and OT departments. Seventy percent of survey respondents were stuck at Levels 1 or 2, while 20% were at Level 3, and about 10% at Level 4.
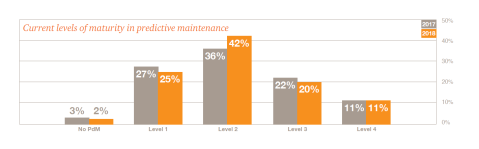
Let’s break down those levels a bit further.
Level 1 means you and your enterprise are making periodic inspections; there’s more reactive (rather than proactive) maintenance. Simply put, you’re in break/fix mode. There is likely old machinery, a non-integrated legacy enterprise asset management (EAM) solution and no overall equipment effectiveness (OEE) software. If you’re a level 1, no problem; everyone starts there. This is the first step in the journey everyone must travel to get to Level 4, which involves continuous, real-time analysis.
From buyers of EAM software, we often hear that users want to do three things: minimize equipment downtime, maximize equipment reliability, and optimize work order metrics. This all starts and ends with data collection and best utilizing that data across your entire enterprise.
Using standardized codes, for example, is a best practice. If you’re able to collect data in a standard way —in a way that everyone understands — you will undoubtedly organize and simplify communication across departments. Within an EAM system, there should be options that users can select as opposed to manual entry. Using standardized codes empowers everyone in the organization to do their jobs successfully and effectively. Who doesn’t want that?
At Level 2, there’s another piece added to the puzzle: OEE software. OEE is a way to benchmark production and measure manufacturing productivity. An excellent OEE score generally lies between 80% and 85%; a perfect OEE score means you’re operating at 100% and manufacturing all parts correctly as quickly as possible without any stoppage time. Many machines today can send signals that they’ve stopped, but those signals don’t tell you why. OEE software allows operators to enter those reasons easily so that you can get to the root cause much more quickly.
At this stage, as well, business intelligence (BI) is still used for reporting. It’s so important to remember that a report is a list of static data; it’s not something you can interrogate. Sending a report every day (from the BI tool) is not BI; it’s a report. You have to convert your data into information.
The next logical question, naturally, would be: how do I do that?
You give the tools to the site managers, crew managers, floor managers. You give the tools to the people who use them, who are affected by what that static data says and let them interrogate using those tools. They’re the best people in your business to identify and rectify which machines, shifts and crews are causing the problems. Not only does this increase visibility and transparency, but it also motivates users to become data-driven.
It’s simple: if you cannot measure it, you cannot improve it. Everyone knows there is downtime, but if you’re tracking that downtime, you can make positive data-driven changes. One company we spoke to about EAM software initially thought its changeover time was 12 hours, but after incorporating OEE software, realized its downtime was 13 hours. When every minute counts, that’s too long.
As you mature through the framework that PwC has created, your profitability is going to increase. So by the time you reach Level 3, you’re well on your way to becoming a data-driven enterprise. You’re encouraging your users to analyze and interrogate the data, to share what they realize, and through that, you’re making your organization better.
How does this work, exactly?
Provide the data to process engineers without confinement of a dashboard, and have them relay what they find to the team. IT and OT need to work together for an enterprise to become truly successful. Don’t enforce and systemize corrupt practices, put in the work to do it right, and as you integrate new software, look at your business process, look at what you can improve, analyze, and then you can improve your overall performance.
Level 4 means your monitoring and tracking your environment in continuous real-time, and you’re now successfully running your business with a predictive maintenance practice.
We’ve said it once, and we’ll repeat it here: a strong organization should emphasize progress, not perfection. Keep getting better. Incrementally. Empower your employees, support your teammates, and work for a better tomorrow today. Those areas for improvement are always there. Look for them, and keep on trying. If that’s your mentality, success won’t be far.
If you’d like to learn more about how enterprise asset management solutions like Aptean EAM can optimize maintenance operations for maximum efficiency, please reach out to us, we’d love to talk.
Empieza a transformar tu empresa hoy mismo
Si estás listo para llevar tu negocio de producción industrial al siguiente nivel, nos encantaría ayudarte
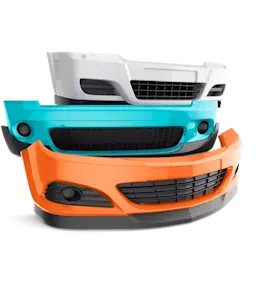