Want To Optimize Your Private Fleet? Know Your Average Trucking Cost per Mile
Want To Optimize Your Private Fleet? Know Your Average Trucking Cost per Mile
Want To Optimize Your Private Fleet? Know Your Average Trucking Cost per Mile
Nov 29, 2021
Jim Endres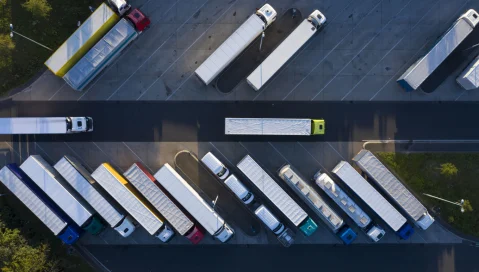
The latest data from the National Private Truck Council (NPTC) says the average trucking cost per mile in the U.S. for private fleets is $2.90. So, if one of your trucks drove 100,000 miles last year, you spent $290,000 to keep that single truck on the road. That’s after adding up all driver, fuel, equipment, insurance, repair, and other truck operating costs.
Every mile you can shave off the odometer adds dollars to your bottom line. But are fleet owners capitalizing like they should on fleet optimization technology that makes truck routes as efficient as possible? The answer, sadly, is no.
What Are the Costs To Operate a Truck?
Here’s NPTC’s breakdown of average trucking cost per mile, along with the percent of operating costs each component represents.
Average Motor Carrier Cost Per Mile 2021 (NPTC)
Source: National Private Truck Council 2021 Benchmarking Report, https://www.nptc.org
Bottom line: there are a lot of expensive trucks out there driving a lot of miles. These costs will vary somewhat based on mode–TL, LTL, or specialty carrier–but this is the average. Big rigs drive an average of 91,500 miles per year, while straight trucks log 20,500 miles.
Are You Driving Too Many Miles?
If your vehicles are making multiple stops during a day-long pick-up or delivery route, you are courting routing disaster if you’re not using some type of routing and scheduling software. While not all routing software is created equal, most use a similar approach to making sure trucks move along a route in the most efficient way possible.
The problems come when businesses plan vehicle routes manually–and a surprising number still do. In this environment, drivers are greeted in the morning with a stack of orders organized in sequence from the first delivery to the last. Such “plans” often ignore key data like historical road conditions and average speeds. And, once they pull away from the loading dock, drivers are pretty much free to dictate the delivery sequence and route with no means to monitor their performance.
In our more than 30 years of routing experience, Aptean has found that, on average, businesses that shift from manual to automated vehicle routing can cut route time and miles by 10-30%, with poorly managed operations being at the high end of that range.
What Are Excess Travel Miles Costing You?
Now let’s apply that math to an actual operation. Say you’re a food distributor with 10 tractor-trailers and 10 straight trucks in your fleet. Using the NPTC average for yearly miles and trucking costs per mile, your fleet will drive a total of 1,120,000 fleet miles at a fully burdened cost of $3,248,000. By reducing your fleet miles 15%, costs are reduced to $2,760,800 for a savings of $487,200.
These savings should be easy to track since expenses are all fleet-related and not dispersed across different departments. And remember, the savings are not a one-time event. They accrue, year after year, and increase as your business grows and continues to optimize.
The cost of route optimization software will vary depending on the complexity of your operation. But in this example, you would recoup your investment within 3 to 12 months of go-live. Not a bad ROI.
Warehouse Operators: Are They More Enlightened?
There is an interesting parallel between transportation operations and warehouse operations. Both share the same insidious enemy: Excess travel time. But warehouse operators seem to do a better job of controlling this costly expense.
In a non-automated warehouse, associates can walk five to ten miles a day back and forth to inventory aisles to pick products. Since labor is the largest warehouse expense after inventory, companies spend millions of dollars on warehouse management software and automated equipment to reduce this non-productive travel time in the warehouse. Many of those same companies won’t spend a fraction of that cost to rein in excess travel time and miles on the road.
Why?
It could be a case of “out of sight, out of mind.” Once they pull away from the loading dock, often route drivers are on their own and not really measured on route efficiency––only delivery success. In contrast, wandering warehouse workers are a constant, and very visible, reminder to management that they are paying for every second of that non-productive time.
What’s Your Average Trucking Cost Per Mile?
The good news is that route efficiency is possible with a relatively modest investment. To estimate your potential savings and ROI from fleet optimization software, start by calculating your average truck cost per mile. The NPTC chart gives you the components. You’ll need a calculator and some patience, but you’ll get there in short order.
From there, it’s a fairly simple question of evaluating the efficiency of your own operation and looking for common mistakes that fleet owners make, and how to avoid them.
After a high-level assessment, routing software providers like Aptean can model your operation, using your own transport data, to arrive at a more precise saving estimate. Ready to learn more? Find out how, now.
Empieza a transformar tu planificación de rutas hoy mismo
Si estás listo para llevar tu negocio de distribución al siguiente nivel, nos encantaría ayudarte.
